video
Profile
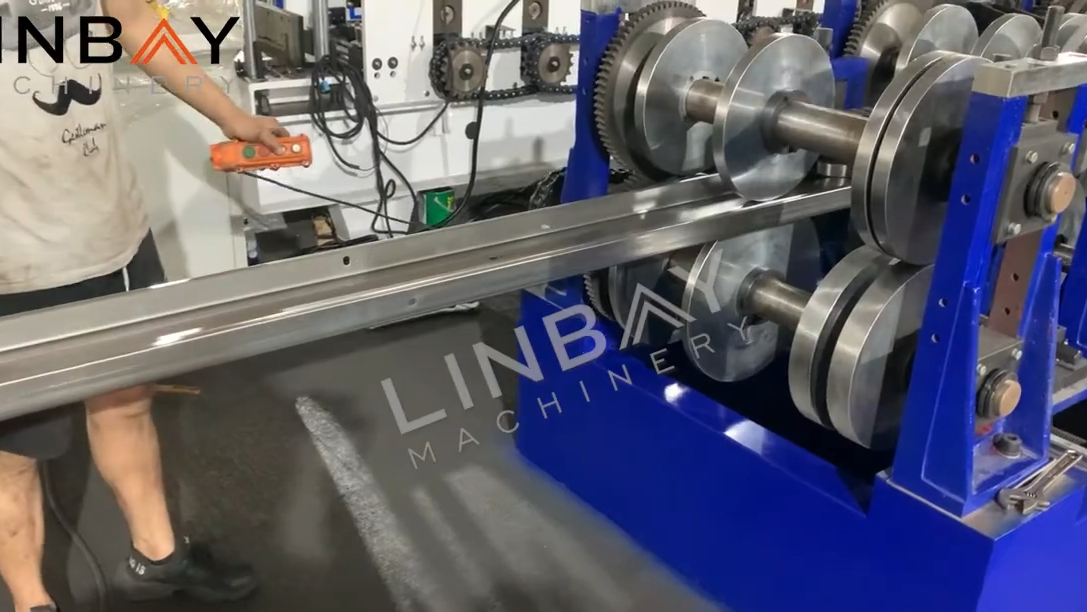
This production line can produce different sizes of C-type, Z-type, and M-type purlins with a high degree of automation. It is a cost-effective investment choice.
Flow chart

Decoiler
We install a press-arm on the decoiler to hold the steel coil in place when changing coils, preventing sudden release and potential harm to workers. Additionally, steel protective leaves are installed to prevent coil slippage during uncoiling. This design not only protects the steel coil and the machine but also ensures safety.
Guiding&Leveler
Guiding rollers keep the steel coil and the machines on the same center-line to prevent distortion of the formed profiles. Multiple guiding rollers are strategically placed along the entire production line. And then, the steel coil enters the leveler, which removes any irregularities, enhancing the flatness and parallelism of the steel coil. This, in turn, improves the quality of both the coil and the final purlin product.
Hydraulic punch
The hydraulic punching machine comes with three sets of dies and corresponding oil cylinders. These dies can be quickly and easily adjusted to meet customer specifications, providing excellent flexibility. The die changeover process is efficient and typically completed within 5 minutes.
Pre cutting
To facilitate the easy replacement of different coil widths for producing various sizes and to save raw material, a pre-cutting device is designed for efficiency, reducing waste.
Leveler, punching machine and cutting machine are integrated with the roll forming machine, which is a very cost-effective design.
Roll former
The roll forming machine features a cast-iron structure and chain driving system. The cast-iron structure is a solid piece of iron, ensuring sturdiness and stability. This machine is capable of producing C, Z, and Sigma purlins. The first four rollers are used for Sigma shape, and they are raised when forming C or Z shapes. Additionally, by manually rotating 2-3 forming stations by 180°, you can switch between producing C and Z purlins. The forming stations on one side of the machine move on rails to produce purlins of different widths. It's important to note that, upon request, we can also manufacture purlin machines that vary in both height and bottom width simultaneously.
Hydraulic station
Our hydraulic station is equipped with a cooling fan that helps maintain optimal operating temperatures, ensuring increased efficiency during continuous operation.
Encoder&PLC
Workers can control the machine through the PLC screen, adjusting production speed, setting production dimensions, and cutting lengths, etc. An encoder is integrated into the production line, converting sensed steel coil length into electrical signals relayed to the PLC control panel. This allows our machine to maintain cutting precision within 1mm, guaranteeing high-quality products and minimizing material waste due to cutting errors.
We offer customization services, including but not limited to motor models, brands, electronic component brands, and PLC control panel language.
1. Decoiler
2. Feeding
3.Punching
4. Roll forming stands
5. Driving system
6. Cutting system
Others
Out table