video
Profile
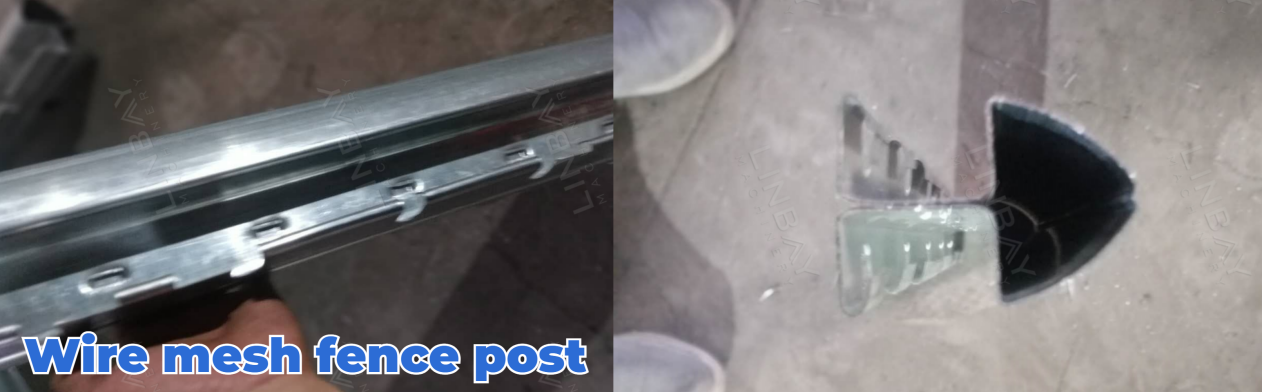
The wire mesh fence post, often referred to as a peach post, earns its name from its outer shape resembling that of a peach. Usually crafted from low-carbon or hot-rolled steel coils, the peach post undergoes cold rolling to achieve its distinctive shape.
The edges of the steel coil are bent outward to form a U-shaped hook, improving stability when securing the wire mesh. Notch slots are strategically positioned on both sides of the peach post to facilitate the installation of the metal wire mesh, with the slot dimensions customized to fit the mesh size.
The complete production line comprises notch punching and roll forming processes. The forming rollers and punch dies are tailored to ensure accurate shaping and precise notch placement.
Real case-Main Techinical Parameters
Flow chart
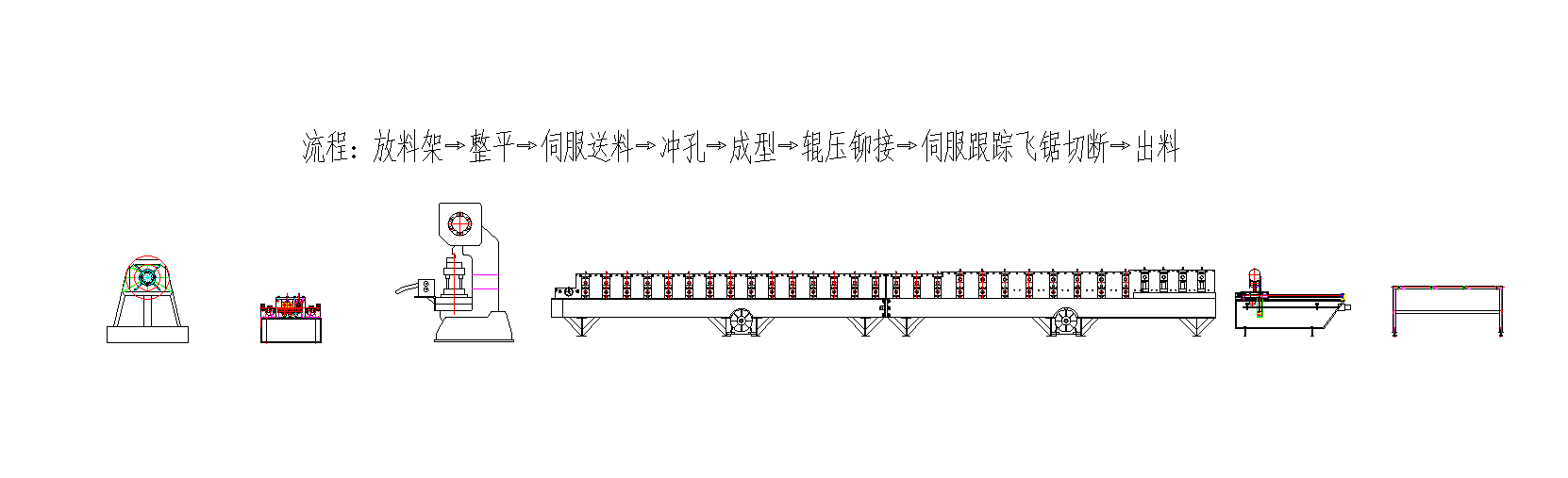
Hydraulic decoiler-Leveler-Servo feeder-Punch press-Pit-Roll former-Flying saw cut-Out table
Main Technical Parameters:
1. Line speed: Adjustable from 0 to 6 m/min
2. Profiles: Single size of mesh fence post
3. Material thickness: 0.8-1.2mm (for this application)
4. Suitable materials: Hot rolled steel, cold rolled steel
5. Roll forming machine: Wall-panel structure with a chain driving system
6. Number of forming stations: 26
7. Riveting system: Roller type; roll former remains operational during riveting
8. Cutting system: Saw cutting; roll former remains operational during cutting
9. PLC cabinet: Equipped with Siemens system
Real case-Description
Hydraulic decoiler
The decoiler provides versatility with options for manual, electric, and hydraulic operation. The choice of type depends on the coil weight and thickness to ensure smooth and seamless uncoiling.
This hydraulic decoiler boasts a robust loading capacity of 5 tons and is outfitted with outward coil retainers to prevent slippage. The motor drives the expansion device, allowing for expansion and contraction to accommodate various coil inner diameters ranging from 460mm to 520mm.
Leveler
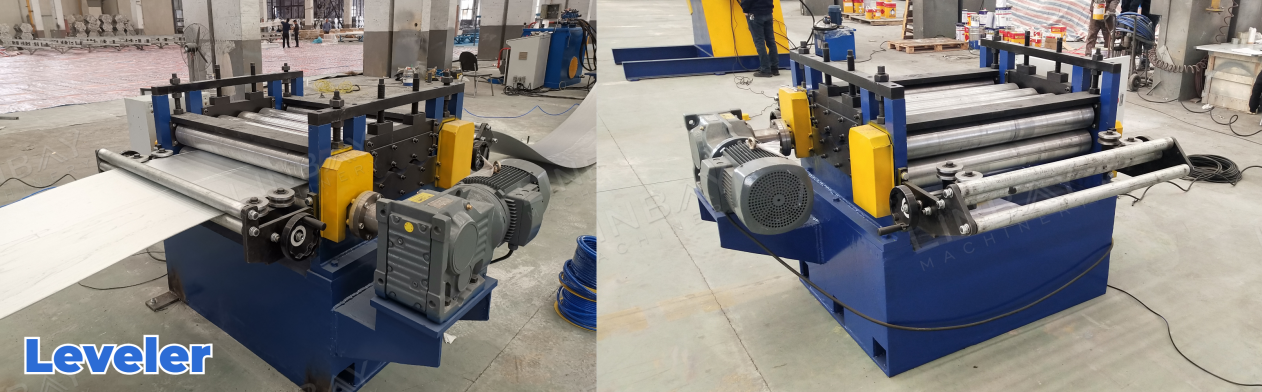
The leveler efficiently flattens the coil, relieving internal pressure and stress, thereby enhancing the punching and forming processes.
Servo feeder & Punch press
Our servo feeder, characterized by minimal start-stop delays, offers precise control over the feeder. This ensures accurate coil feed length and punch positions, enhancing overall production accuracy and efficiency.
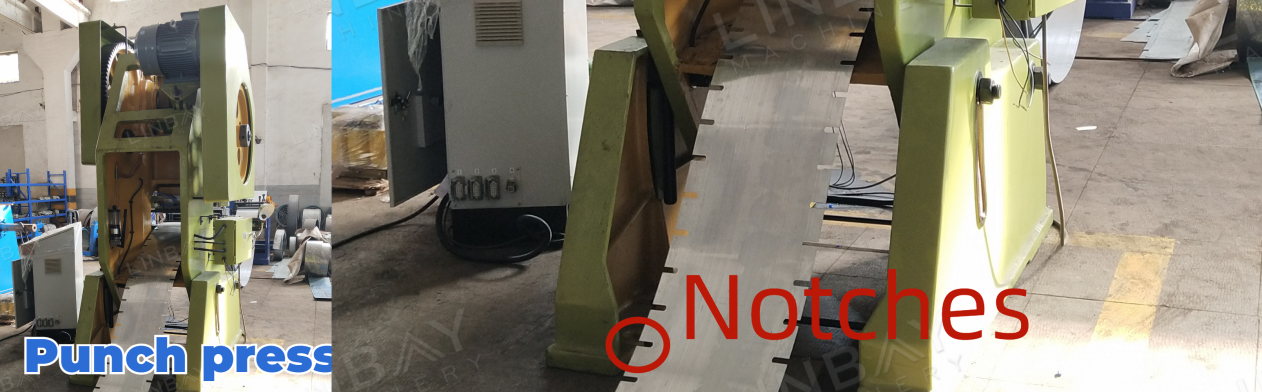
Finished wire mesh fence posts are equipped with numerous notches designed for wire mesh connections.
Roll forming machine
This roll forming machine is constructed with a wall-panel structure and operates using a chain drive system. Throughout the forming process, the coil gradually deforms under force, adhering to the specified "Peach shape" outlined in the provided drawings.
To prevent coil separation at the post junction during extended use, precautionary measures are implemented. Following roll forming, riveting rollers press the coil overlap, creating rivet impressions that bolster post stability and increase lifespan.
Furthermore, due to the circular design of the riveting rollers, the roll former can seamlessly continue its operation as the coil advances during riveting, eliminating the need for setting another moving base for the riveting device.
Flying saw cut
Due to the enclosed shape of the peach post, saw cutting emerges as the most suitable method, preventing any coil deformation at the cut edges. Moreover, the cutting process does not generate waste. To optimize production line capacity, the cutting machine's base can be adjusted backward and forward to synchronize with the roll forming machine's speed, ensuring uninterrupted operation.
1. Decoiler
2. Feeding
3.Punching
4. Roll forming stands
5. Driving system
6. Cutting system
Others
Out table