video
Profile
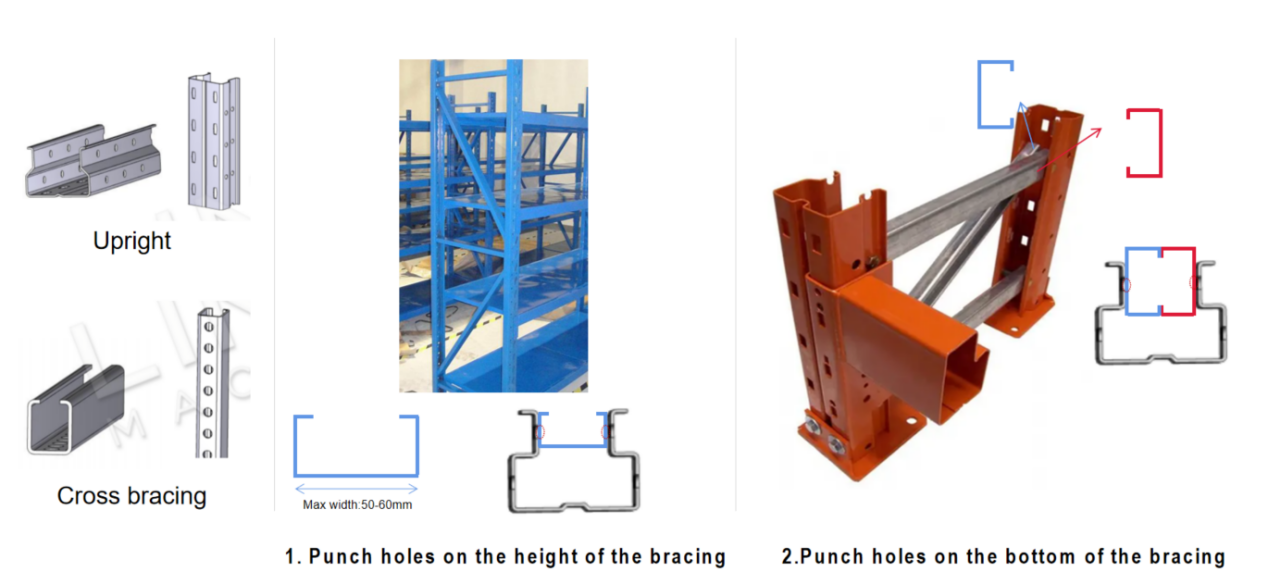
Cross bracing plays a pivotal role in shelving systems, reinforcing the overall shelf structure. Positioned within the rack upright, it offers supplementary support. Depending on the installation method chosen, connection holes are strategically placed for secure attachment.
*Installation Method 1: A single brace is installed within the rack upright, requiring pre-punched holes at the height of the bracing for screw installation.
*Installation Method 2: Two bracings are installed within the rack upright, also requiring pre-punched holes at the bottom of the bracing for screw installation.
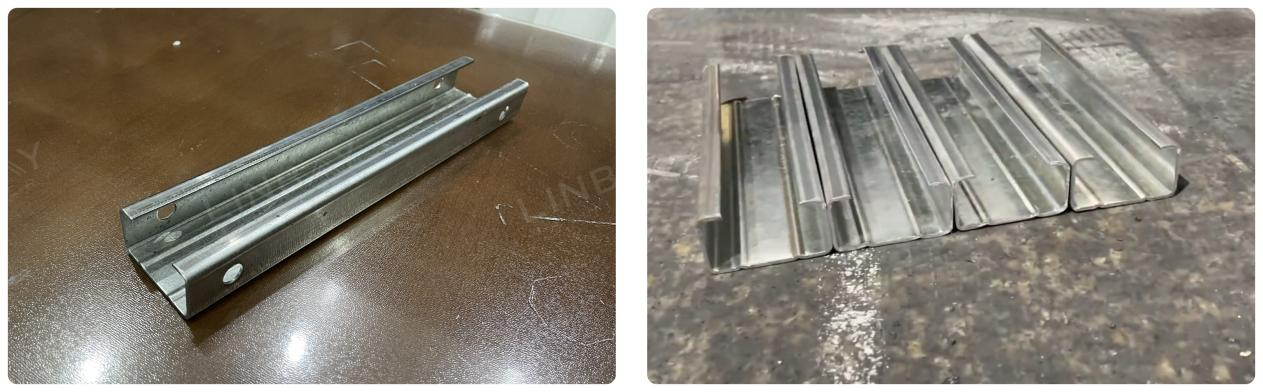
In this case, we used the installation method 1. We also offer a customizable solution allowing simultaneous punching at the bottom and high sides of the bracing for increased flexibility.
Description
Flow chart
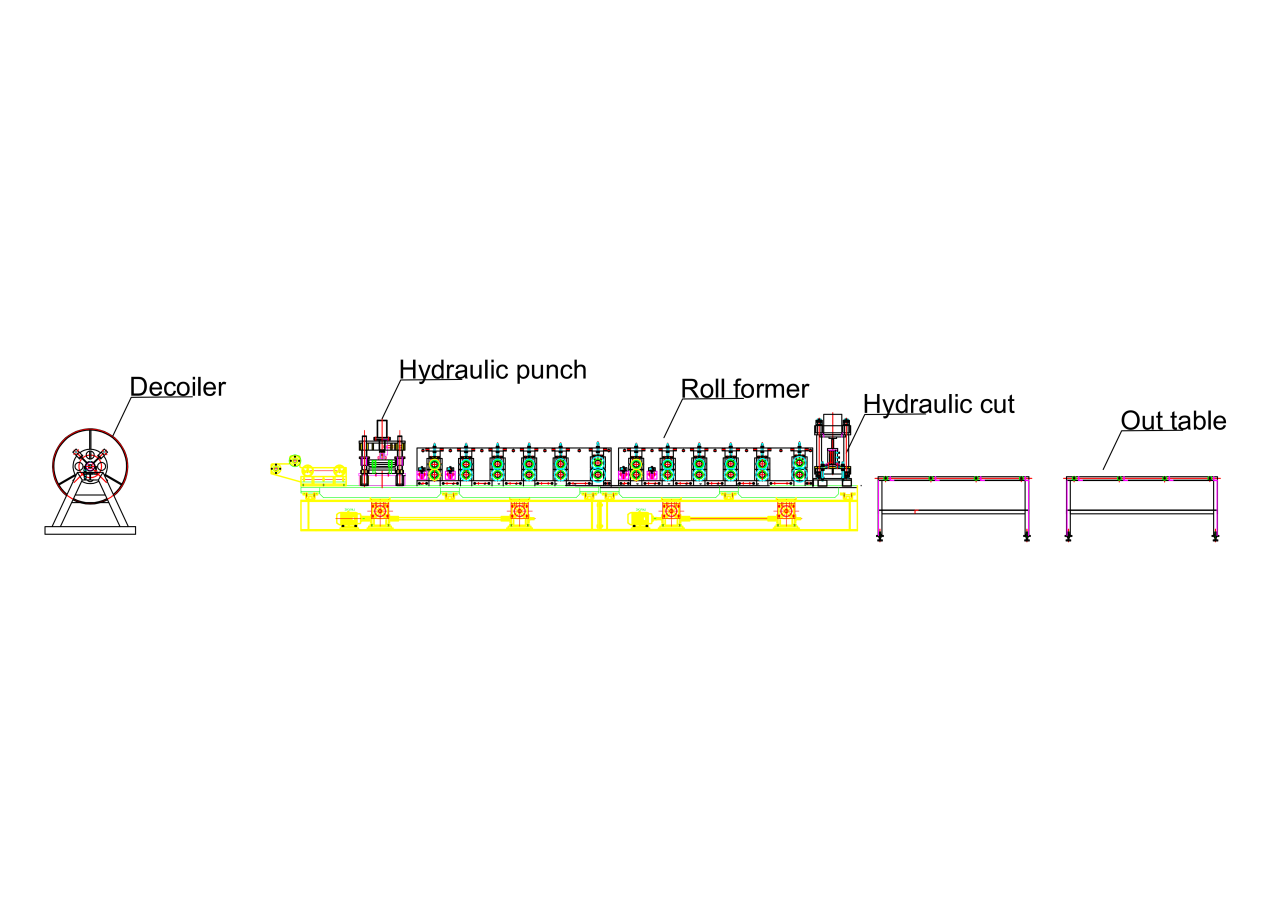
Decoiler--Guiding--Leveler--Hydraulic punch--Roll forming machine--Hydraulic cutting--Out table
Decoiler
The decoiler is equipped with a press arm to firmly secure the steel coil during replacement, minimizing the risk of sudden release and potential injury to workers. It also features a brake device that regulates the tension of the feeding rollers, ensuring a steady uncoiling speed. Moreover, steel protective blades are incorporated to prevent the steel coil from slipping during the decoiling process, enhancing both safety and cost-effectiveness.
Guiding
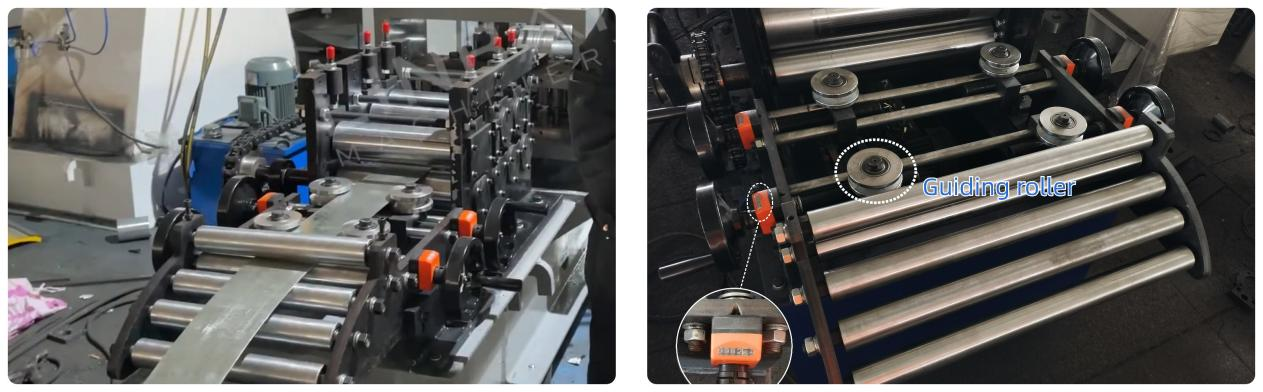
Guiding rollers play a crucial role in ensuring alignment between the steel coil and the machine, maintaining them along the same centerline to prevent distortion of the formed profiles. These rollers are strategically positioned not only at the entry point but also throughout the entire forming line. The distances from each guiding roller to the edge are meticulously recorded in the manual, enabling workers to make precise adjustments based on the data provided. This ensures accurate alignment, even if slight displacement occurs during transport or production adjustments made by workers.
Leveler
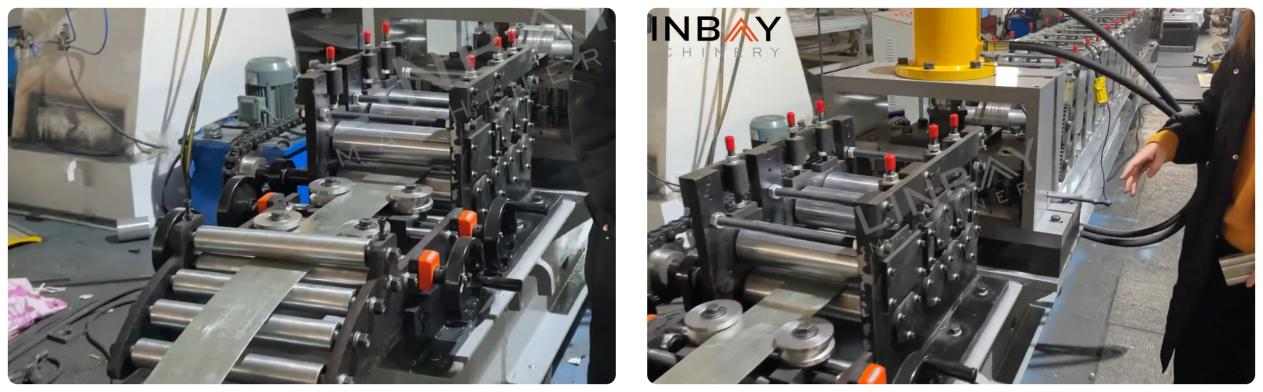
The leveling machine plays a vital role in improving the flatness and parallelism of the steel coil, ensuring high-quality production outcomes. Integrated into the roll forming machine, it comprises 2 upper leveling rollers and 3 lower leveling rollers. Alternatively, customers seeking higher speed capabilities can opt for a standalone leveling machine, albeit with a slightly larger production line footprint.
Hydraulic Punch
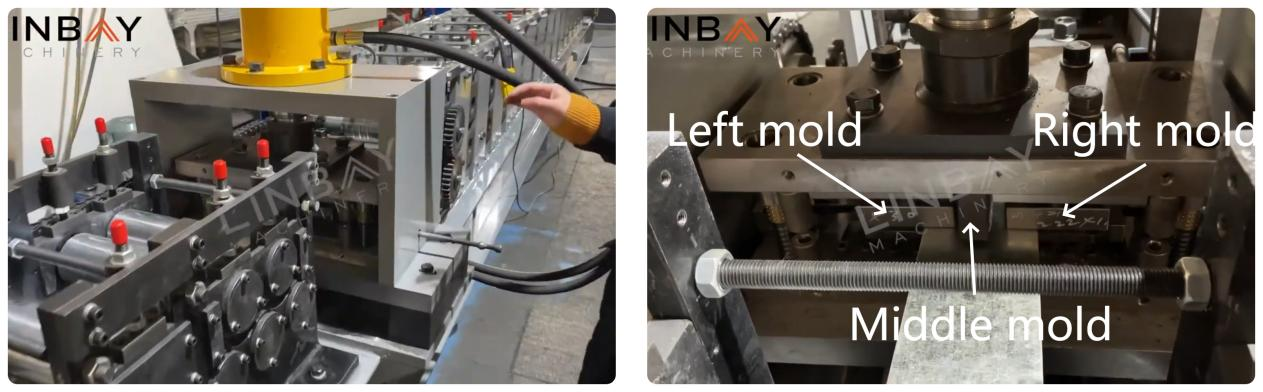
The hydraulic punch machine, powered by a hydraulic station, utilizes left and right molds to punch holes precisely at the centerline of the height sides after forming. Following cutting, two holes are present at each end of a cross bracing for screw installation. Additionally, the middle mold on the hydraulic punch can imprint the customer's logo on the steel coil without penetrating, facilitating brand promotion and market expansion.
Roll Forming Machine
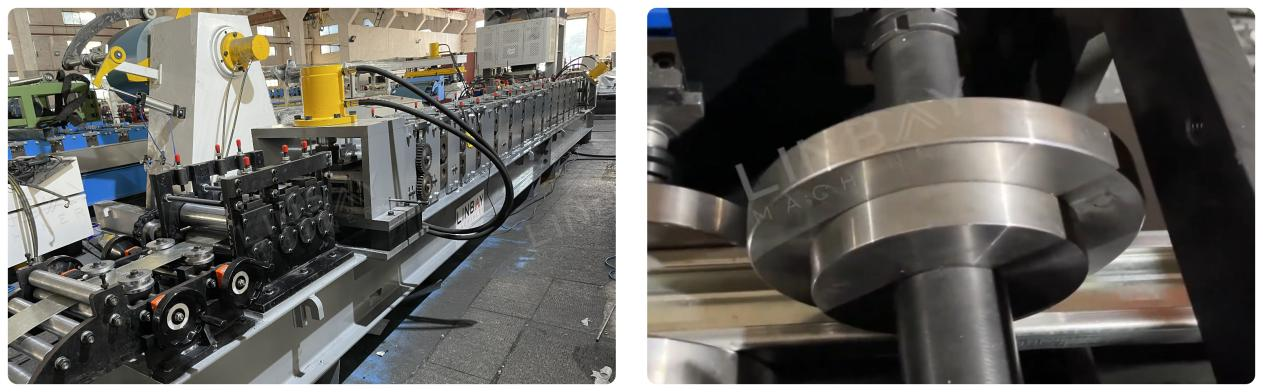
The roll forming machine, featuring a wall-panel structure and chain driving system, plays a crucial role in the production line. Configured for customers utilizing 450MPa yield strength steel coils, it consists of 22 forming stations. To ensure immediate production convenience upon delivery, the roll forming machine is tested using steel coils with the same yield strength (450MPa) as those used in customer production.
The forming rollers are crafted from Gcr15, a high-carbon chromium-bearing steel renowned for its exceptional hardness and wear resistance. Chrome plating on the roller surface prolongs its lifespan, complemented by shafts made of heat-treated 40Cr material.
Hydraulic Cutting & Encoder
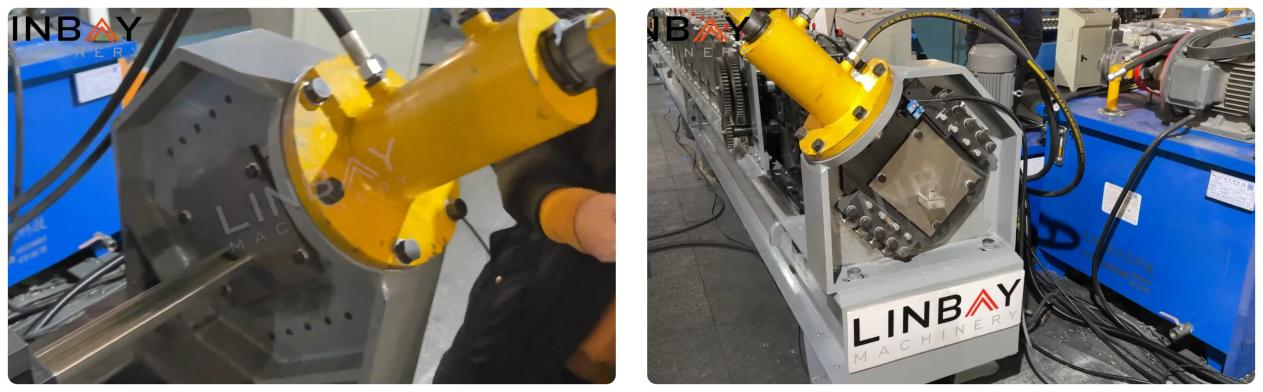
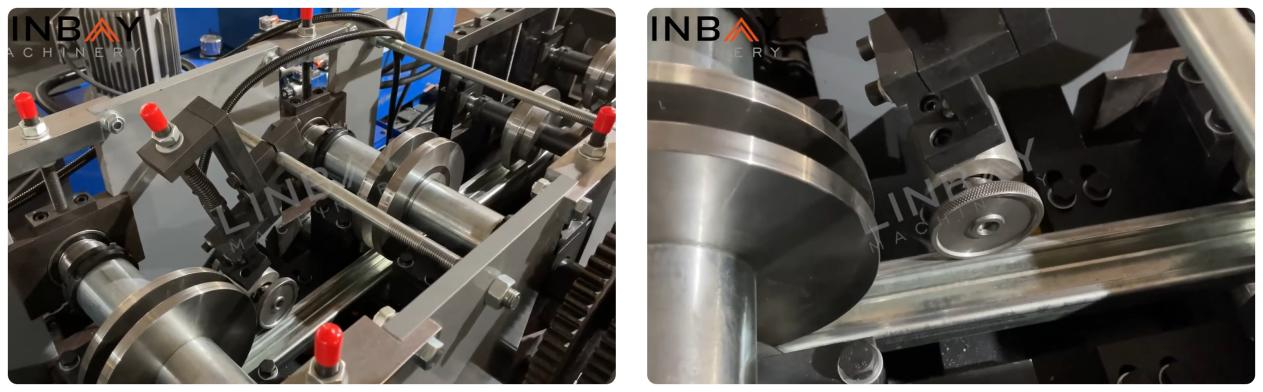
The integration of a Japanese Koyo encoder allows for the conversion of sensed steel coil length into electrical signals, transmitted to the PLC control cabinet. This precise system ensures cutting accuracy within 1mm, thereby guaranteeing high-quality products while minimizing waste resulting from incorrect cuts.
Hydraulic Station
The hydraulic station is equipped with a cooling fan for efficient heat dissipation, ensuring prolonged, low-fault operation and durability.
PLC Control Cabinet
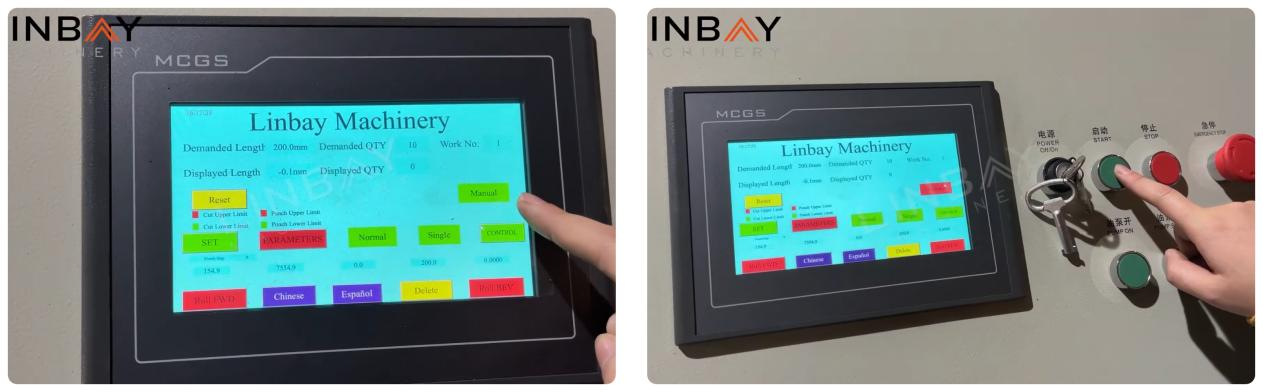
Operators have the capability to manage production speed, establish production dimensions, and determine cutting lengths via the PLC screen. The PLC control cabinet is equipped with protective features like overload, short circuit, and phase loss protection. Additionally, the language displayed on the PLC screen can be tailored to specific languages or multiple languages to meet the preferences of the customer.
Warranty
The delivery date is indicated on the nameplate, starting the two-year guarantee for the entire production line and a five-year warranty for rollers and shafts.
1. Decoiler
2. Feeding
3.Punching
4. Roll forming stands
5. Driving system
6. Cutting system
Others
Out table