PROFILE
A metal gutter serves as a crucial drainage component installed along roof edges to capture and direct rainwater away from the structure, helping to prevent water-related damage. Gutters are commonly constructed from materials like aluminum, galvanized steel, color-coated steel, copper, and galvalume, with thicknesses ranging between 0.4 and 0.6 mm.
This production line features a dual-row structure, allowing for the manufacture of two different gutter sizes on the same line, though not at the same time. This design optimizes space utilization and lowers machinery costs for the client.
REAL CASE-MAIN TECHNICAL PARAMETERS
Flow chart: Decoiler--Guiding--Roll former--Swag punching--Hydraulic cutting--Out table

REAL CASE-MAIN TECHNICAL PARAMETERS
· Line Speed: Adjustable, ranging from 0-12m/min.
· Compatible Materials: Aluminum, galvanized steel, color-coated steel, galvalume, copper.
· Material Thickness: 0.4-0.6mm.
· Roll Forming Machine: Double-row design with a wall-panel structure.
· Drive System: Chain-driven system.
· Cutting System: Stop-and-cut method, where the roll former pauses during cutting.
· PLC Control: Siemens system.
REAL CASE-MACHINERY
1.Hydraulic decoiler*1
2.Roll forming machine*1
3.Hydraulic swag punch machine*1
4.Hydraulic cutting machine*1
5.Out table*2
6.PLC control cabinet*1
7.Hydraulic station*2
8.Spare parts box(Free)*1
REAL CASE-DESCRIPTION
Hydraulic Decoiler
· Frame: The sturdy frame is engineered to reliably support steel coils, with a hydraulic-powered decoiler that boosts efficiency and safety during coil feeding into the production line.
· Core Expansion Mechanism: The hydraulic-driven mandrel (or arbor) adjusts to accommodate steel coils with inner diameters of 490-510mm, securing the coil for smooth and steady uncoiling.
· Press Arm: A hydraulic press arm ensures the coil stays in position, mitigating the risk of sudden recoil due to internal stress and safeguarding worker safety.
· Coil Retainer: Secured to the mandrel blades with screws and nuts, the coil retainer keeps the steel coil from slipping off, and is easy to install or remove as needed.
· Control System: Equipped with a PLC and control panel that includes an emergency stop button, enhancing operational safety.
· Decoiler Options for Dual-Row Roll Forming: For dual-row roll forming machines, a single-shaft decoiler can be used and repositioned to save costs, though it requires more time. Alternatively, two single-shaft decoilers or a double-shaft decoiler can be used for more efficient production.
Guiding Bars
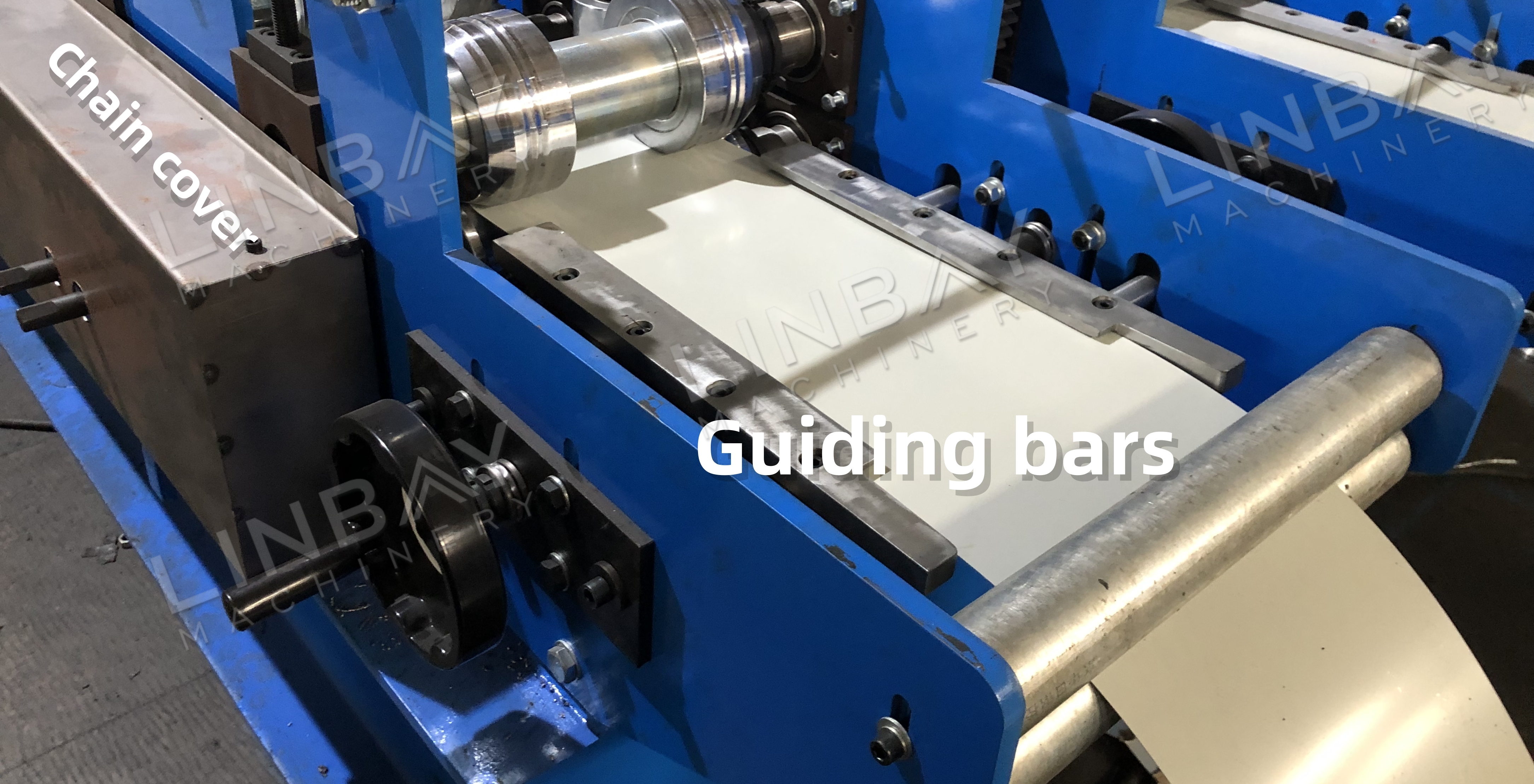
· Alignment: Ensures that the steel coil is properly centered with the machine’s axis, preventing feed issues that could lead to twisting, bending, burrs, or dimensional inaccuracies in the finished product.
· Stability: Stabilizing the material is key, with guiding bars ensuring a consistent feed, which is vital for producing high-quality roll-formed components.
· Direction: They direct the material smoothly into the initial set of forming rollers, which is critical for accurate initial shaping.
· Maintenance: It’s important to regularly recalibrate the guiding devices, especially after transport or extended use. Before dispatch, Linbay records the guiding width in the user manual, allowing for precise calibration when the customer receives the equipment.
Roll Forming machine
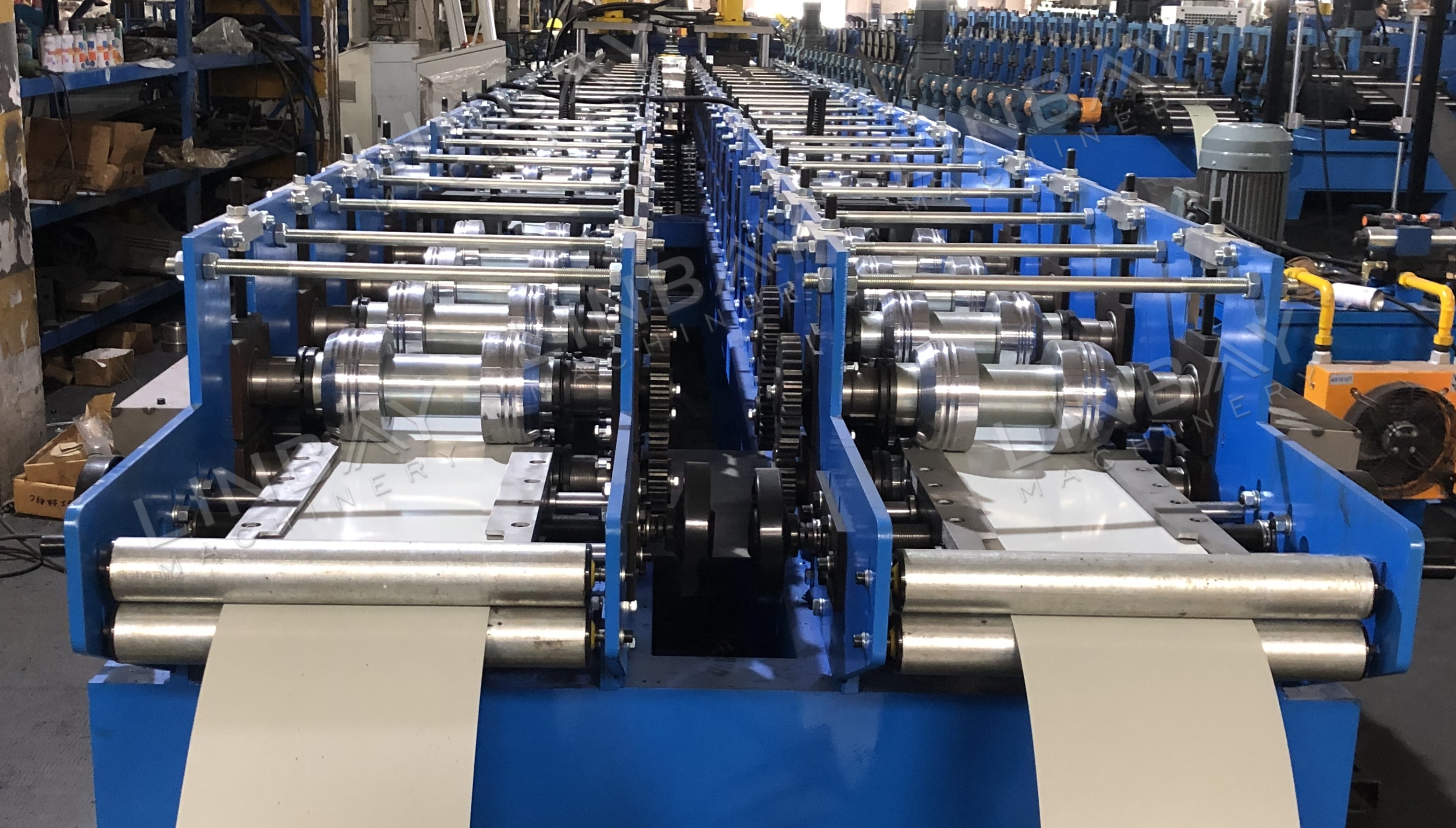
· Cost-Effective for Gutter Manufacturing: Incorporates a wall-panel design with a chain-driven system.
· Versatility for Multiple Sizes: The dual-row setup supports the production of two different gutter sizes, optimizing space and reducing machinery expenses.
· Chain Protection: Chains are enclosed within a metal casing, ensuring worker safety and shielding the chains from damage due to airborne debris.
· Improved Efficiency: Minimizes setup time compared to single-row systems requiring manual changeovers.
· Forming Rollers: Equipped with 20 forming rolls, including 2 angled rolls for enhanced small wave formation as shown in the accompanying image.
· Durable Rollers: Rollers are chrome-plated and heat-treated for corrosion and rust resistance, contributing to a longer service life.
· Main Motor: Standard specification is 380V, 50Hz, 3-phase, with options for customization available.
Swag Punching
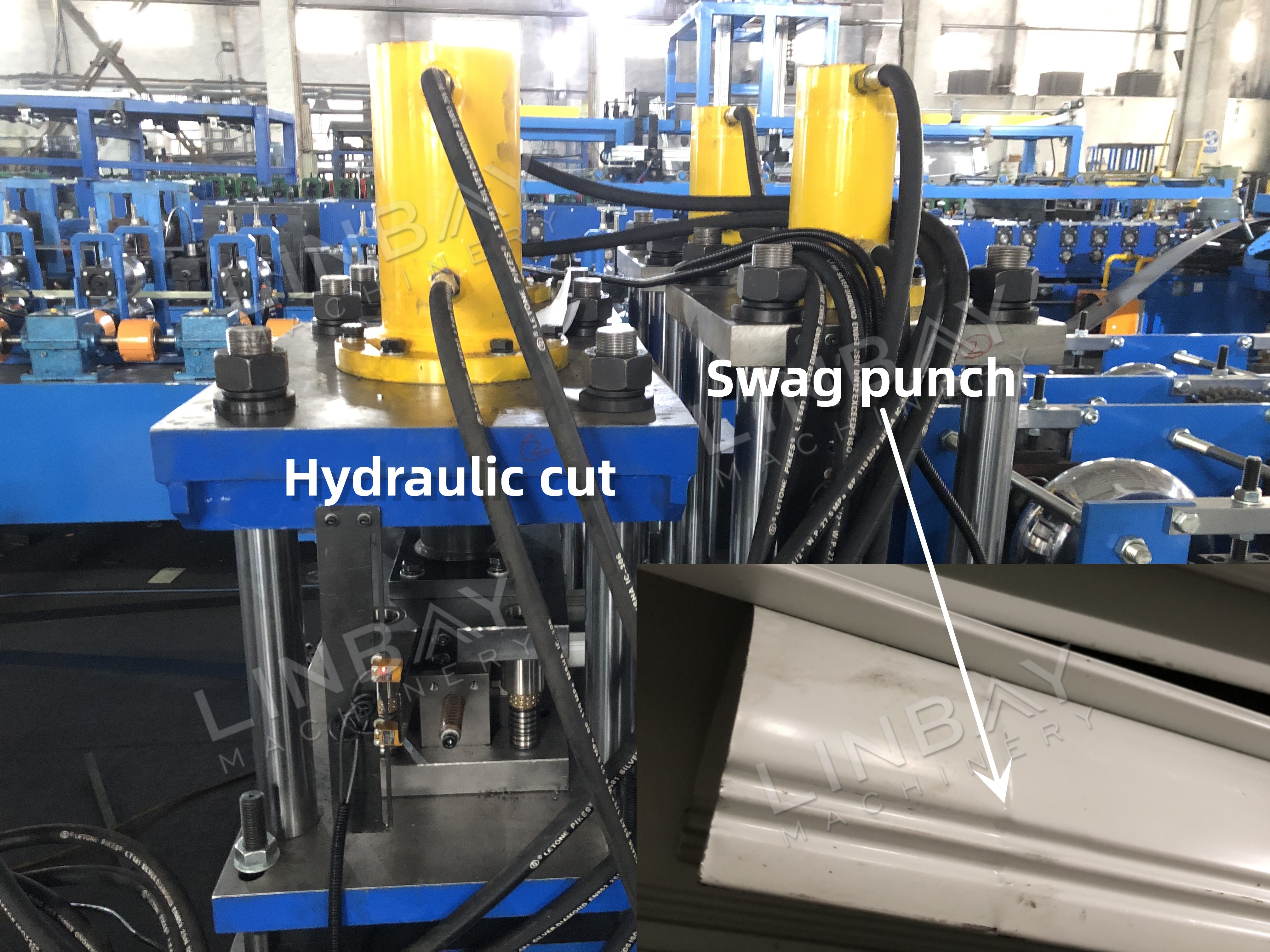
· Gutter Configuration: The end of the metal gutter is tapered to decrease its diameter, enabling it to slide into another gutter section for a secure fit.
· Machine Capability: Utilizes a hydraulic punching die to form the end connection, ensuring a smooth and secure joint between two gutter segments.
Hydraulic Cutting
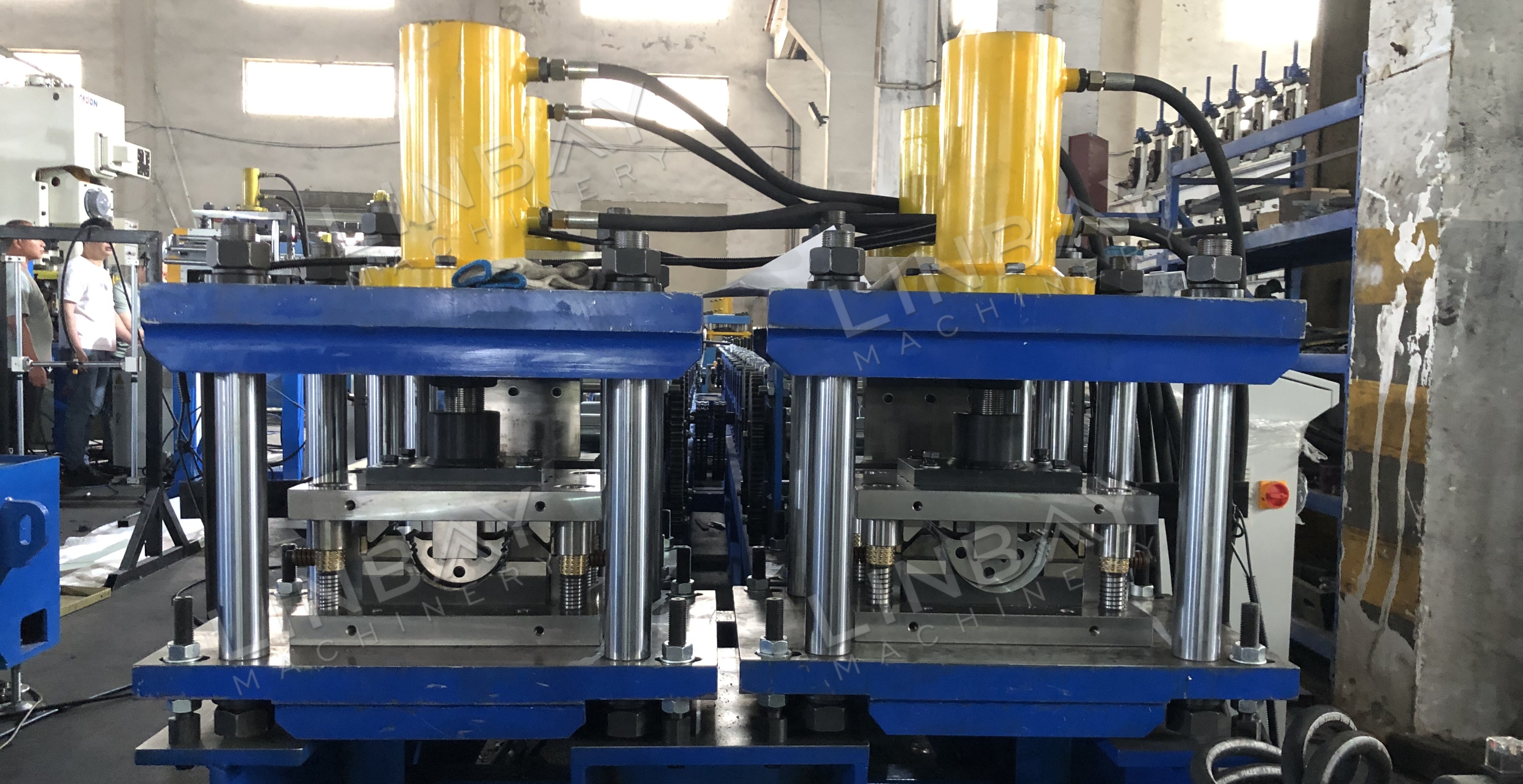
· Custom Blades: Engineered to fit the gutter profile, ensuring clean cuts without deformation or burrs.
· Accurate Cutting Length: Maintains a tolerance of ±1mm. This precision is achieved through an encoder that measures the steel coil's movement, converting this data into electrical signals sent to the PLC cabinet. Operators can adjust cutting length, production quantity, and speed via the PLC interface.
1. Decoiler
2. Feeding
3.Punching
4. Roll forming stands
5. Driving system
6. Cutting system
Others
Out table