Profile
DIN rail is a standardized metal rail commonly used in electrical engineering. Its design facilitates the easy installation and removal of components, typically featuring a series of slots or holes for attachment using screws or snap-on mechanisms. The standard dimensions of DIN rails are 35mm x 7.5mm and 35mm x 15mm, with a standard thickness of 1mm.
Real case-Main Technical Parameters
Flow chart: Decoiler--Guiding--Hydraulic punch--Roll forming machine--Hydraulic cutting machine
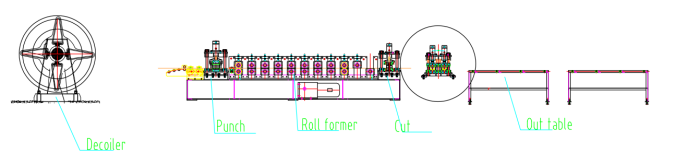
1.Line speed: 6-8m/min, adjustable
2.Suitable material:Hot rolled steel, cold rolled steel
3.Material thickness:The standard thickness is 1mm, and the production line can be customized within a thickness range of 0.8-1.5mm.
4.Roll forming machine: Wall-panel structure
5.Driving system: chain driving system
6.Cutting system: Stop to cut, roll former stops when cutting.
7.PLC cabinet: Siemens system.
Machinery
1.Decoiler*1
2.Roll forming machine*1
3.Out table*2
4.PLC control cabinet*1
5.Hydraulic station*1
6.Spare parts box(Free)*1
Container size: 1x20GP
Real case-Description
Decoiler
The decoiler is the initial component of the production line. Given the relatively small thickness and size of DIN rails, manual decoilers are adequate to meet production requirements. However, for higher production speeds, we also provide solutions with electric and hydraulic decoilers.
Hydraulic punch
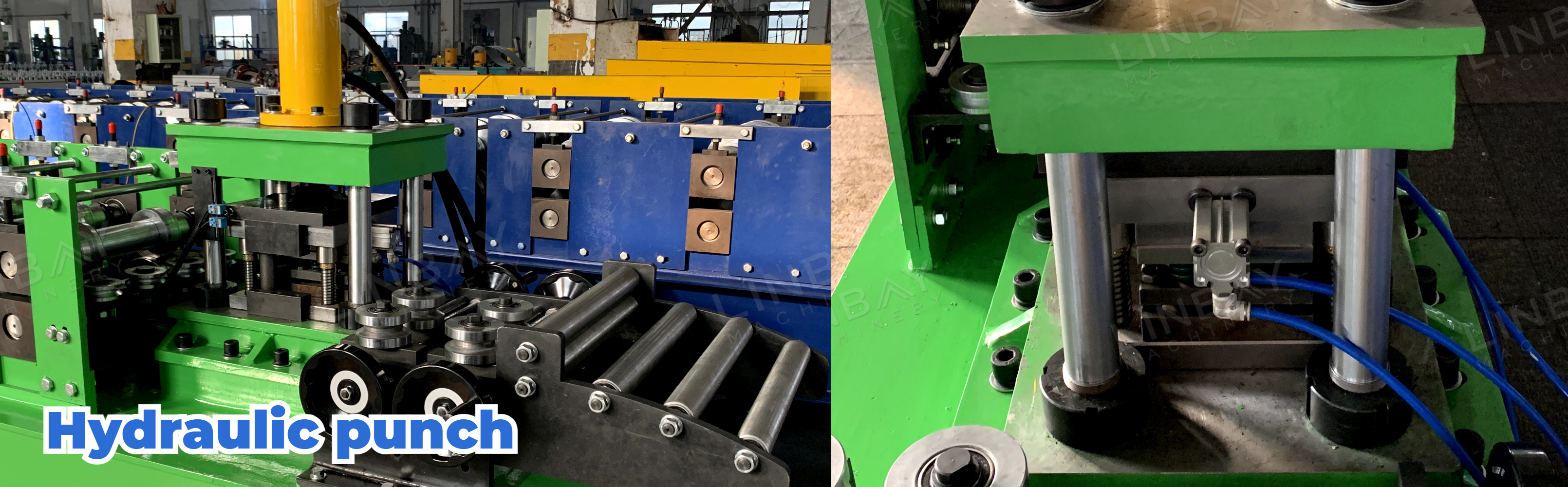
In this setup, the hydraulic punch is integrated with the main forming machine, sharing the same base. During punching, the steel coil temporarily stops entering the forming machine. For applications requiring higher production speeds, standalone hydraulic punch machines are available.
Guiding
The guiding rollers ensure alignment between the steel coil and the machine, preventing distortion during the forming process.
Roll forming machine
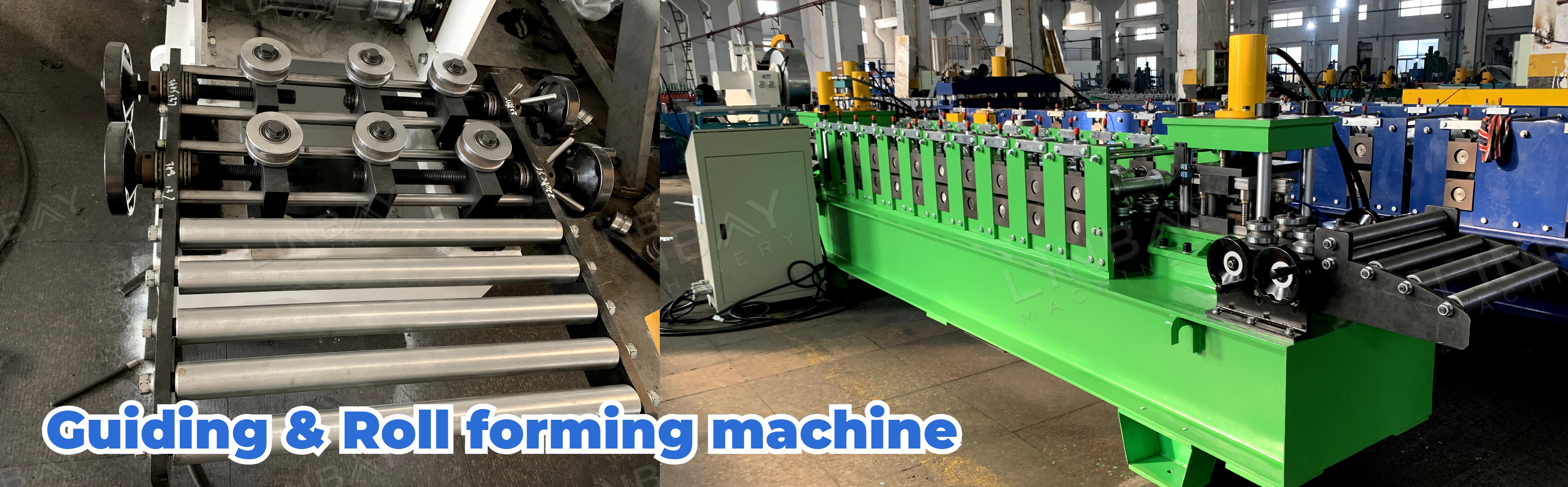
This roll forming machine employs a wall-panel structure and a chain driving system. Its dual-row design enables the production of two sizes of DIN rail. However, it should be noted that both rows cannot operate simultaneously. For higher production demands, we recommend setting up a separate production line for each size.
It should be emphasized that the cutting length precision of the roll forming machine with a double-row structure is within ±0.5mm. If your precision requirement is less than ±0.5mm, it is not recommended to use the double-row structure. Instead, the solution of having an independent production line for each size is more suitable.
Hydraulic cutting machine
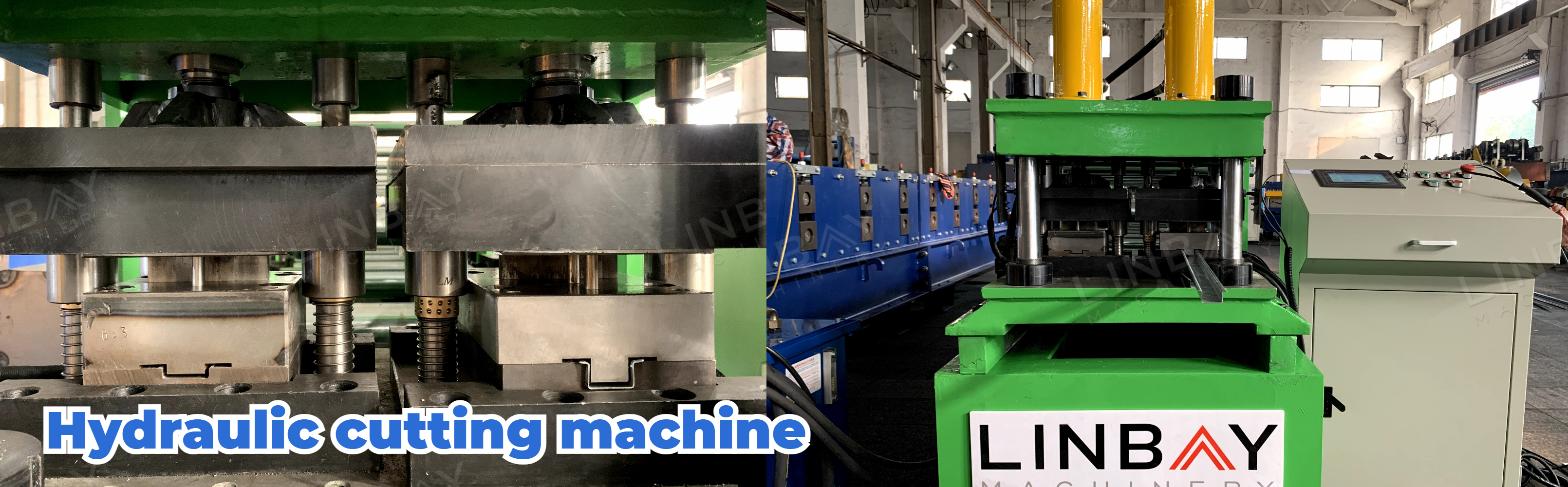
The base of the cutting machine remains stationary during operation, causing the steel coil to pause its advancement during cutting.
To achieve higher production speeds, we provide a flying cutting machine. The term "flying" indicates that the cutting machine's base can move back and forth. This design enables the steel coil to advance continuously through the forming machine during cutting, eliminating the need to stop the forming machine and thereby enhancing the overall production line speed.
The cutting blade molds at the end of each row are customized to match the shape of the respective size of DIN rail.
1. Decoiler
2. Feeding
3.Punching
4. Roll forming stands
5. Driving system
6. Cutting system
Others
Out table