video
Profile
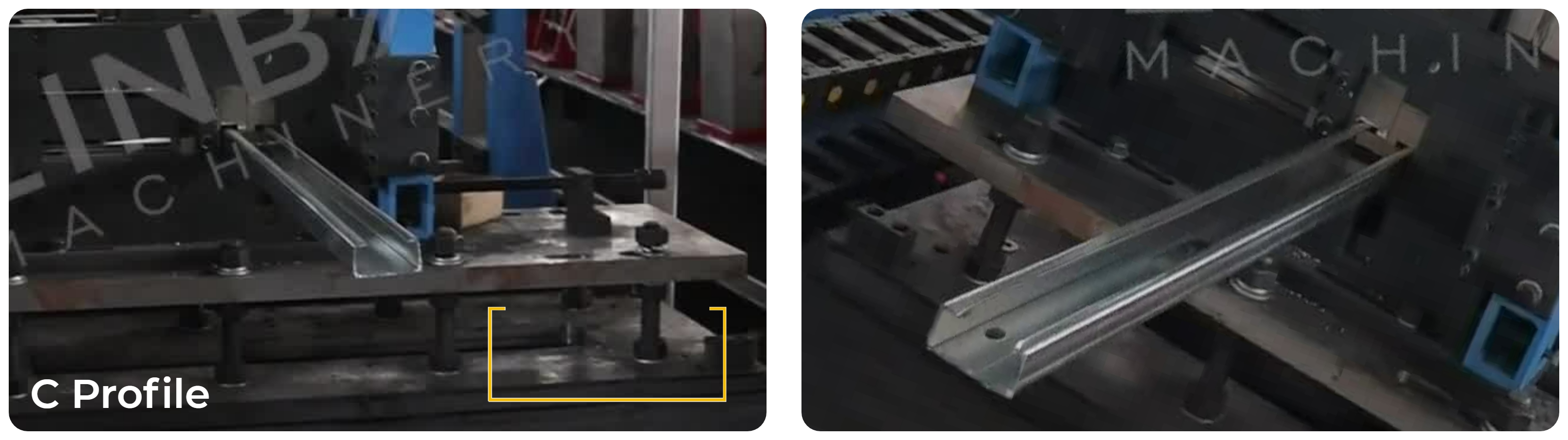
Flow chart

Hydraulic decoiler-Guiding-Levler-Hydraulic punch-Pre cut-Roll former-Flying universal cut-Out table
5 Ton Hydraulic Decoiler
First, we place the steel coil on this 5-ton hydraulic decoiler. The hydraulic station provides power to expand the inner support rod, which then rotates to unwind the coil. We've also added a press-arm to secure the coil and prevent sudden unwinding during changes. The outward coil retainer protect against coil slippage, all designed with worker safety in mind. The hydraulic decoiler is more efficient and reduces labor costs compared to manual decoilers.
Guiding & Leveler
After passing through guiding rollers, the steel coil enters the leveler. Multiple guiding rollers keep the coil aligned with the machine's centerline, preventing distortion in the final product. When the steel coil's thickness exceeds 1.5 millimeters or its yield strength surpasses 300 MPa, a leveler is essential. It eliminates irregularities, enhancing the coil's flatness and parallelism, thus improving the quality of the coil and the final purlin product.
Encoder & Hydraulic Punch
The steel coil then moves to the hydraulic punching machine, known as the "Flying Hydraulic Punch," with "Flying" indicating that the machine moves in coordination with the forming speed, increasing production efficiency. Before this, the steel coil passes through an encoder and guiding rollers. The encoder converts sensed coil length into electrical signals sent to the PLC control panel, enabling precise control of punching location within a 1mm deviation.
Pre-cut
To facilitate the change of steel coils with different widths for various size production and save on raw material waste, we've designed a pre-cut device.
Roll Former
This is the most critical part of the entire production line. We've adopted a cast-iron structure, a solid and stable single-piece steel construction. The machine is equipped with a gearbox and universal joint, enabling efficient rotation of the forming rollers and handling the 4mm thick steel coil forming work. Three motors on either side of the machine provide power to the reducer, allowing the forming station to move back and forth on the rails, adjusting the gap between the rollers, resulting in the production of purlins of different sizes, ranging from 100 to 400mm in width and 40 to 100mm in height. Workers can simply input commands on the PLC control screen for automatic adjustments. Transitioning from C to Z profiles is straightforward, requiring a manual 180° rotation of 2-3 forming stations.
Flying Universal Hydraulic Cut
This cutting machine only requires one set of blades to cut purlins of different sizes smoothly and without burrs.
PLC
In the control panel, we use international brand electrical components, such as Yaskawa from Japan, Siemens from Germany, and Schneider from France, ensuring high-quality electrical components that are easy to maintain. We also offer customization of the PLC screen language in English, Spanish, Russian, French, and other languages.
1. Decoiler
2. Feeding
3.Punching
4. Roll forming stands
5. Driving system
6. Cutting system
Others
Out table