video
Profile
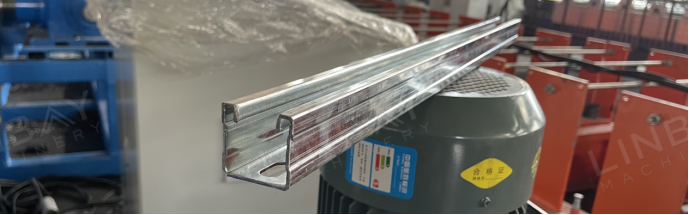
Strut channels are frequently utilized in applications such as solar panel mounting, plumbing and piping, and HVAC systems. Standard strut channel heights include 21mm, 41mm, 52mm, 62mm, 71mm, and 82mm. The diameter of the forming rollers changes with the height of the strut channel, with taller channels requiring more forming stations. These channels are typically manufactured from hot-rolled steel, cold-rolled steel, galvanized steel, or stainless steel, with thicknesses ranging from 12 gauge (2.5mm) to 16 gauge (1.5mm).
Note: Due to the higher yield strength of stainless steel, the forming force needed is greater compared to low-alloy steel and regular carbon steel of the same thickness. Therefore, the roll forming machines designed for stainless steel differ from those used for regular carbon steel and galvanized steel.
LINBAY provides production lines capable of producing various dimensions, which are classified into manual and automated types depending on the level of automation required for dimension adjustments.
Real case-Main Technical Parameters
Flow chart: Decoiler--Servo feeder--Punch press--Guiding--Roll forming machine--Flying saw cutting--Out table
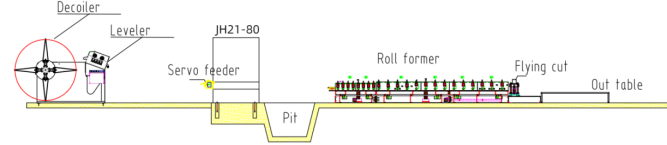
Real case-Main Technical Parameters
1.Line speed: 15m/min, adjustable
2.Suitable material:Hot rolled steel, cold rolled steel, galvanized steel
3.Material thickness: 1.5-2.5mm
4.Roll forming machine: Cast-iron structure
5.Driving system: Gearbox driving system
6.Cutting system: Flying saw cutting. Roll forming machine doesn’t stop when cutting
7.PLC cabinet: Siemens system
Real case-Machinery
1.Hydraulic decoiler with leveler*1
2.Servo feeder*1
3.Punch press*1
4.Roll forming machine*1
5.Flying saw cutting machine*1
6.PLC control cabinet*2
7.Hydraulic station*2
8.Spare parts box(Free)*1
Container size: 2x40GP+1x20GP
Real case-Description
Decoiler with Leveler
This machine integrates the functions of a decoiler and a leveler, optimizing floor space usage. Leveling steel coils thicker than 1.5mm is crucial, particularly for the continuous punching of holes in strut channels. The leveler ensures the steel coil is smooth and relieves internal stress, facilitating easier shaping and straight forming.
Servo Feeder
A servo feeder is named for its use of a servo motor. Thanks to the servo motor's minimal start-stop delay, it offers exceptional precision in feeding steel coils. This precision is essential for maintaining tight tolerances and minimizing steel coil waste during strut channel production. Additionally, pneumatic clamps within the feeder advance the steel coil while safeguarding its surface from scratches.
Punch Press
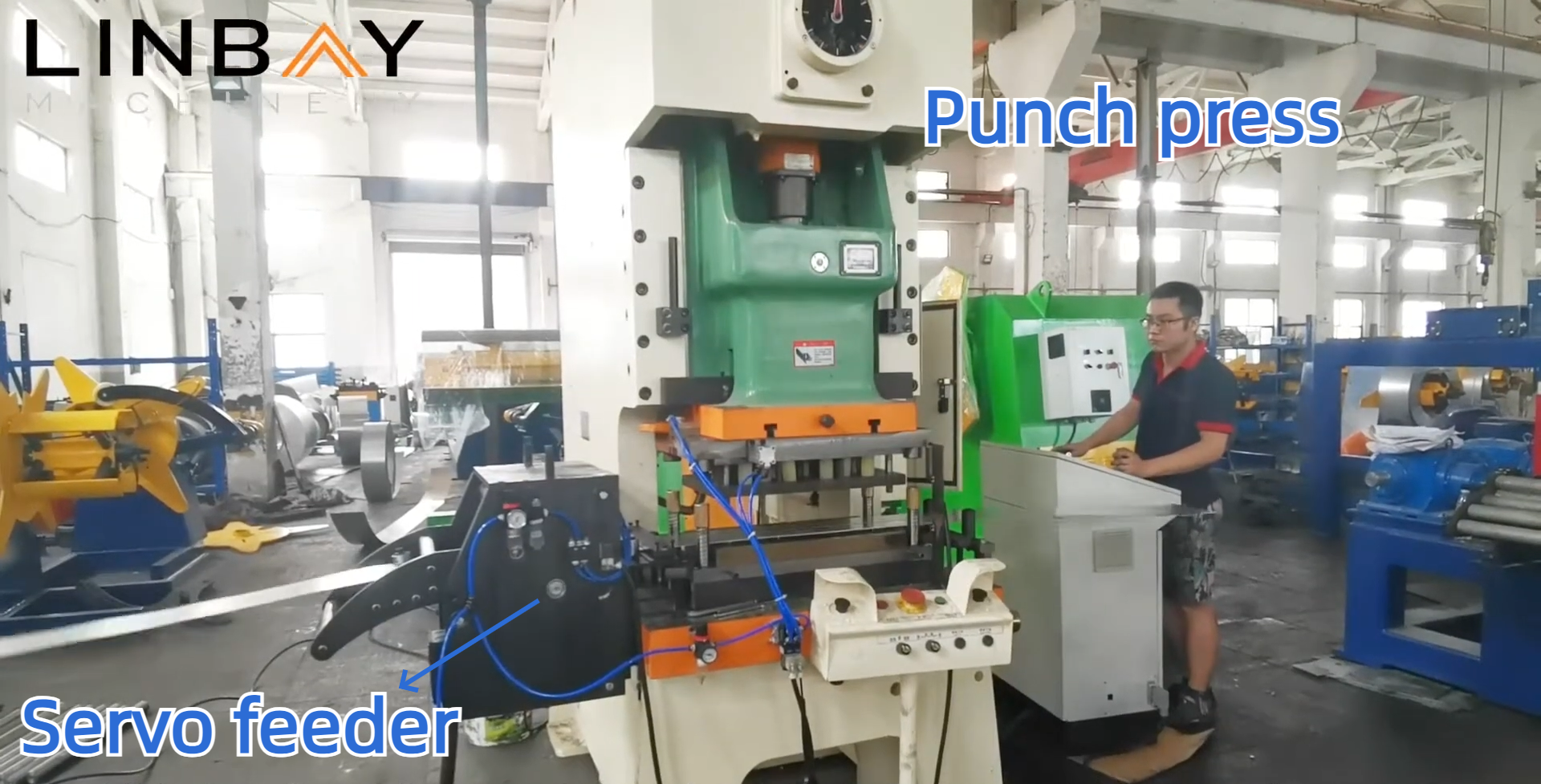
A punch press is employed to create holes in the steel coil, essential for attaching screws and nuts to secure the strut channels. This punch press operates more rapidly than an integrated hydraulic punch (mounted on the same base as the roll forming machine) and a standalone hydraulic punch. We utilize punch presses from the well-known Chinese brand Yangli, which has multiple global offices, ensuring convenient after-sales service and easy access to replacement parts.
Guiding
Guide rollers keep the steel coil and machines aligned along the same centerline, ensuring the straightness of the strut channel. This alignment is crucial for matching the strut channels with other profiles during installation, directly impacting the stability of the entire construction structure.
Roll Forming Machine
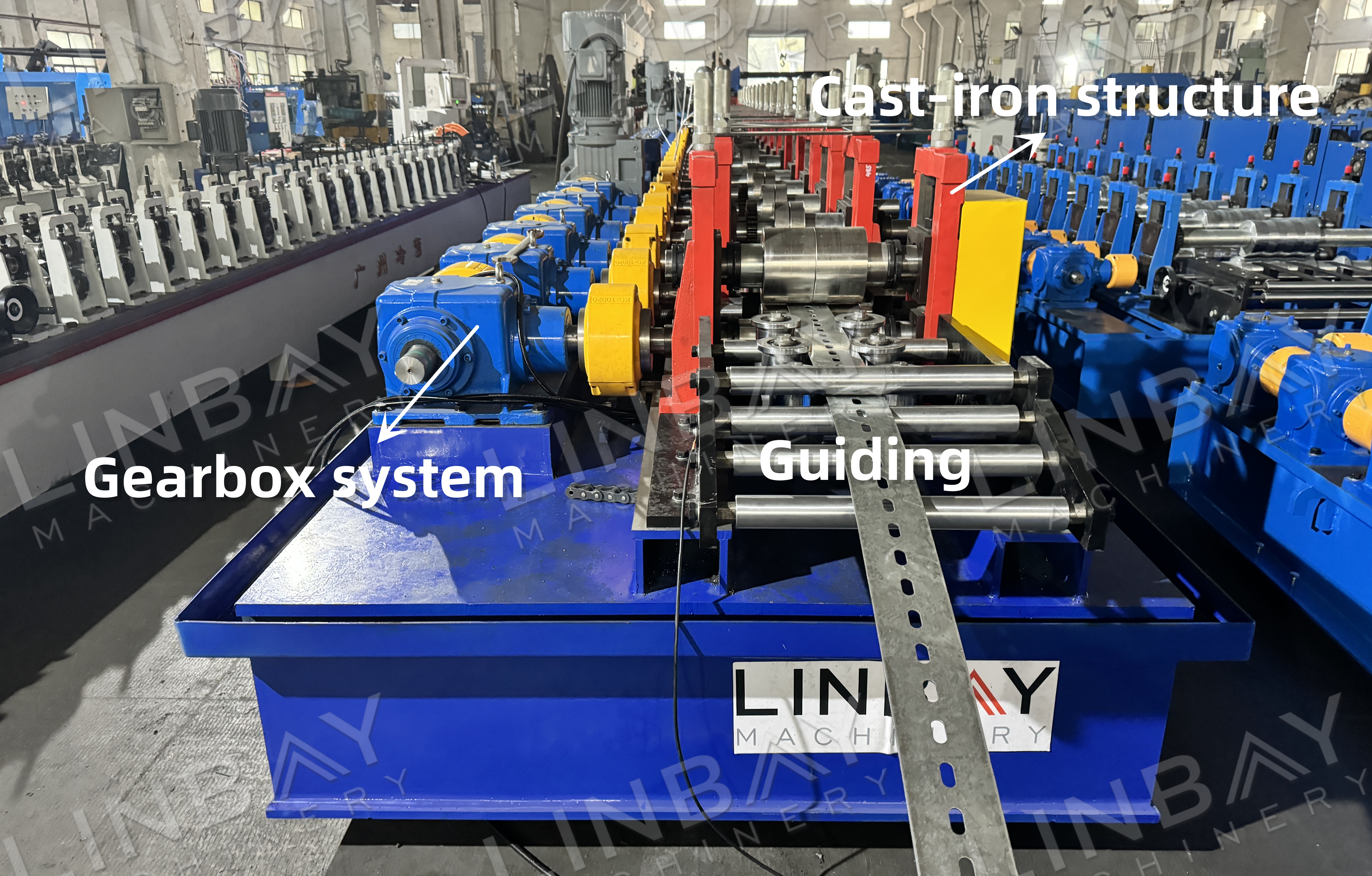
The roll forming machine boasts a cast-iron structure made from a single piece of steel, providing exceptional durability. The upper and lower rollers exert force to shape the steel coil, driven by a gearbox to deliver sufficient power for the forming process.
Flying Saw Cutting
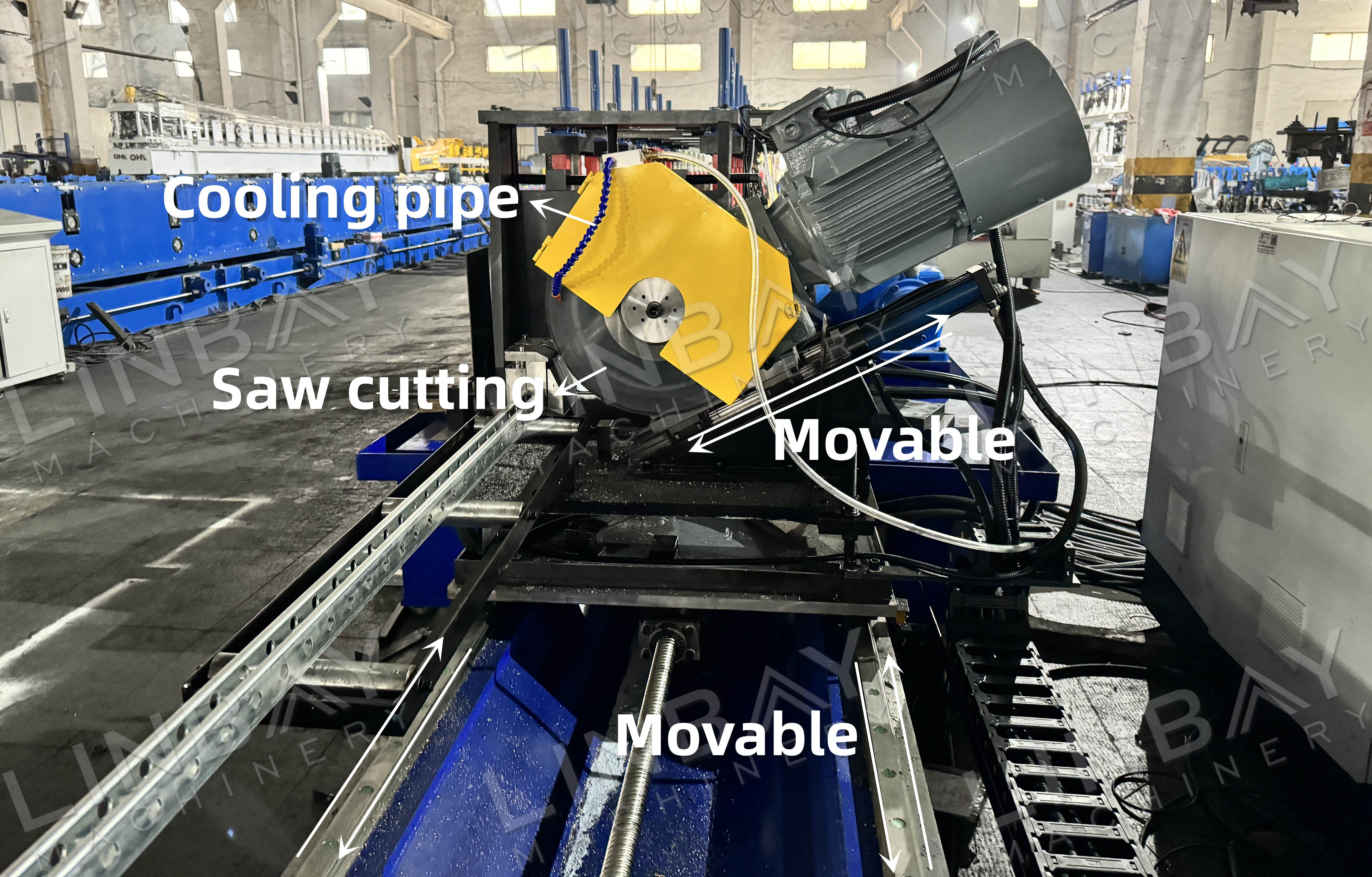
The flying saw cutter's carriage accelerates to synchronize with the speed of the moving strut channels, which is also the speed of the roll forming machine. This enables cutting without halting the production process. This highly efficient cutting solution is perfect for high-speed operations and generates minimal waste.
During the cutting process, pneumatic power moves the saw blade base towards the strut channel, while hydraulic power from the hydraulic station drives the rotation of the saw blade.
Hydraulic Station
The hydraulic station supplies the power needed for equipment like the hydraulic decoiler and hydraulic cutter and is equipped with cooling fans to ensure effective heat dissipation. In hot climates, we suggest enlarging the hydraulic reservoir to improve heat dissipation and increase the volume of fluid available for cooling. These measures help maintain a stable operating temperature during prolonged use, thereby ensuring the reliability and efficiency of the roll forming production line.
PLC Control Cabinet & Encoder
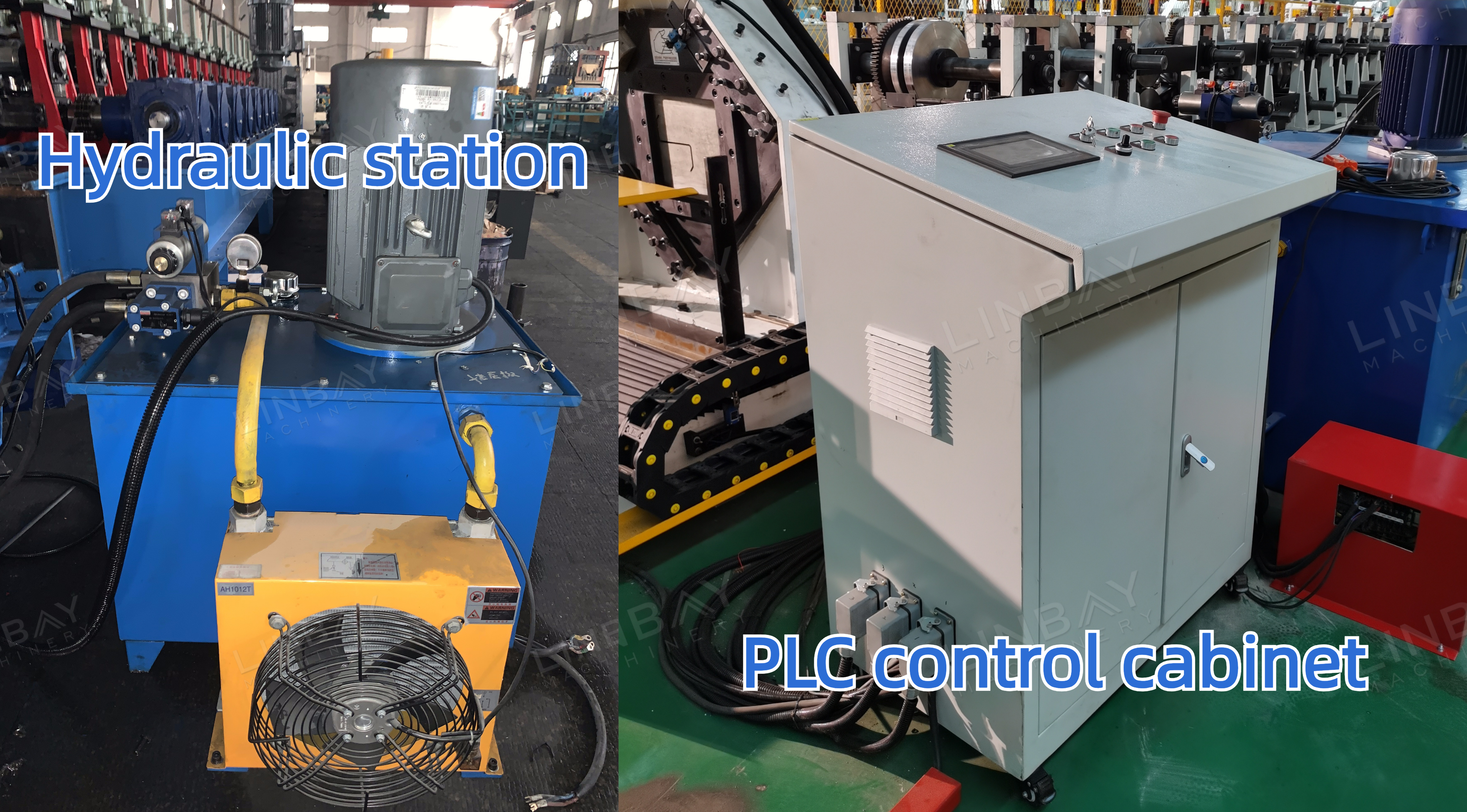
Encoders play a crucial role in delivering feedback on position, speed, and synchronization. They transform the measured length of the steel coil into electrical signals, which are then sent to the PLC control cabinet. Operators use the control cabinet display to adjust parameters such as production speed, output per cycle, and cutting length. Thanks to the precise measurements and feedback from encoders, the cutting machine can achieve a cutting accuracy within ±1mm.
Flying hydraulic cutting VS Flying saw cutting
Cutting Blade: Each dimension of the flying hydraulic cutter requires a separate standalone cutting blade. However, saw cutting is not restricted by the dimensions of the strut channels.
Wear and Tear: Saw blades generally experience faster wear compared to hydraulic cutting blades and require more frequent replacement.
Noise: Saw cutting tends to be louder than hydraulic cutting, which may necessitate additional soundproofing measures in the production area.
Waste: A hydraulic cutter, even when properly calibrated, typically results in an unavoidable waste of 8-10mm per cut. On the other hand, a saw cutter produces nearly zero waste.
Maintenance: Saw blades require a coolant system to manage heat generated from friction, ensuring continuous and efficient cutting. In contrast, hydraulic cutting maintains a more consistent temperature.
Material Limitation: Stainless steel possesses a higher yield strength than regular carbon steel. When working with stainless steel, only saw cutting is suitable for processing the material.
1. Decoiler
2. Feeding
3.Punching
4. Roll forming stands
5. Driving system
6. Cutting system
Others
Out table