SQUARE TUBE ROLL FORMING MACHINE
This production line is tailored for creating square tubes with a thickness of 2mm, and dimensions ranging from 50-100mm in width and 100-200mm in height.
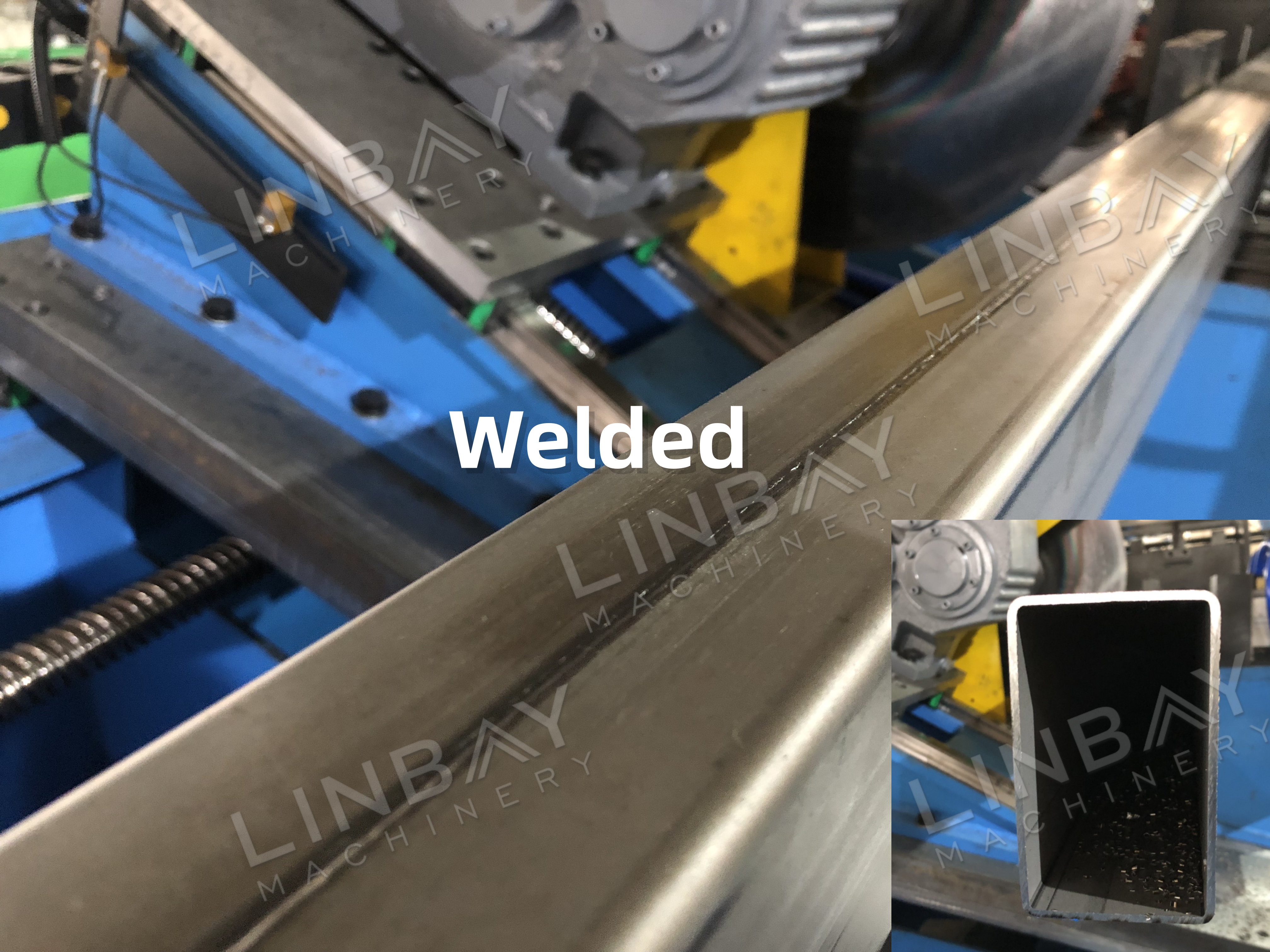
The production line encompasses several key processes: decoiling, pre-punch leveling, punching, post-punch leveling, roll-forming, laser welding, fume extraction, and cutting.
Featuring a comprehensive setup and advanced automation, this production line offers a superior alternative to conventional welding tube machines, particularly for lower production volumes.
REAL CASE-MAIN TECHNICAL PARAMETERS
Flow chart: Hydraulic decoiler with loading car--Leveler--Servo feeder--Punch press--Hydraulic punch--Limiter--Guiding--Leveler--Roll former--Laser weld--Flying saw cut--Out table

REAL CASE-MAIN TECHNICAL PARAMETERS
· Adjustable line speed: 5-6m/min with laser welding
· Compatible materials: Hot-rolled steel, cold-rolled steel, black steel
· Material thickness: 2mm
· Roll forming machine: Cast iron structure with a universal joint
· Drive system: Gearbox-driven system featuring a universal joint cardan shaft
· Cutting system: Flying saw cutting, with the roll former continuing operation during cutting
· PLC control: Siemens system
REAL CASE-MACHINERY
1.Hydraulic decoiler*1
2.Standalone Leveler*1
3.Punch press*1
4.Hydraulic punch machine*1
5.Servo feeder*1
6.Integrated Leveler*1
7.Roll forming machine*1
8.Laser welding machine*1
9.Welding Fume Purifier*1
10.Flying saw cutting machine*1
11.Out table*2
12.PLC control cabinet*2
13.Hydraulic station*3
14.Spare parts box(Free)*1
REAL CASE-DESCRIPTION
Hydraulic decoiler
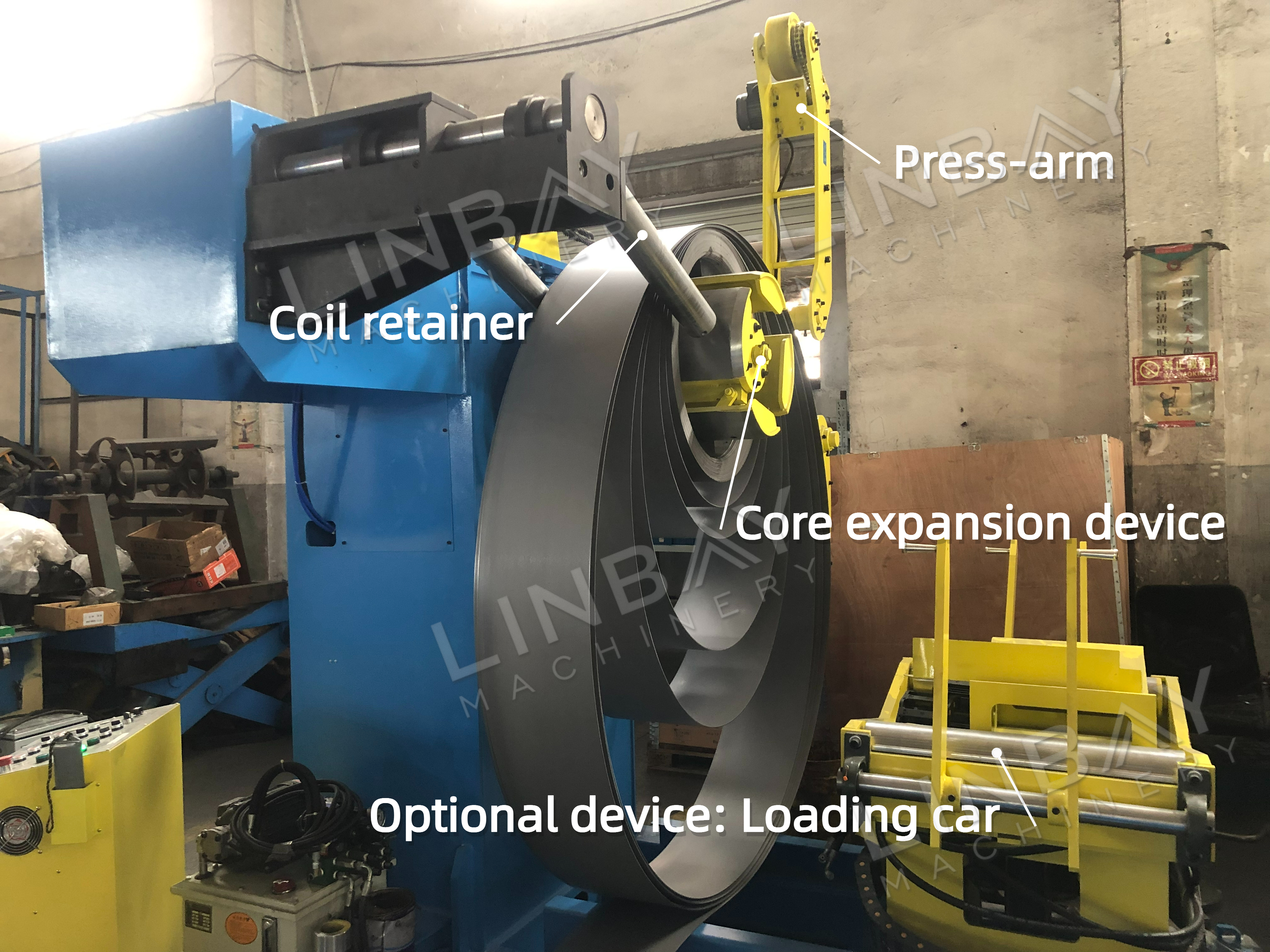
• Function: The sturdy frame is built to support steel coil loading. The hydraulic decoiler enhances efficiency and safety in feeding steel coils into the production line.
• Core Expansion Device: The hydraulic mandrel or arbor adjusts to fit steel coils with an inner diameter of 490-510mm, expanding and contracting to firmly hold the coil and ensure smooth decoiling.
• Press-arm: The hydraulic press arm secures the steel coil, preventing abrupt uncoiling due to internal stress and safeguarding workers from potential injuries.
• Coil Retainer: The design ensures the coil remains securely in place while allowing for easy installation and removal.
• Control System: The system features a PLC and control panel, which includes an emergency stop button for added safety.
Optional Device: Loading Car
• Efficient Coil Replacement: Helps in changing steel coils more safely and efficiently, reducing labor costs.
• Hydraulic Alignment: The platform can be hydraulically adjusted up and down to align with the mandrel. Additionally, the loading car, which is fitted with wheels, can move electrically along the tracks.
• Safety Design: The concave design firmly grips the steel coil, preventing any sliding.
Optional machine: Shearer Butt Welder
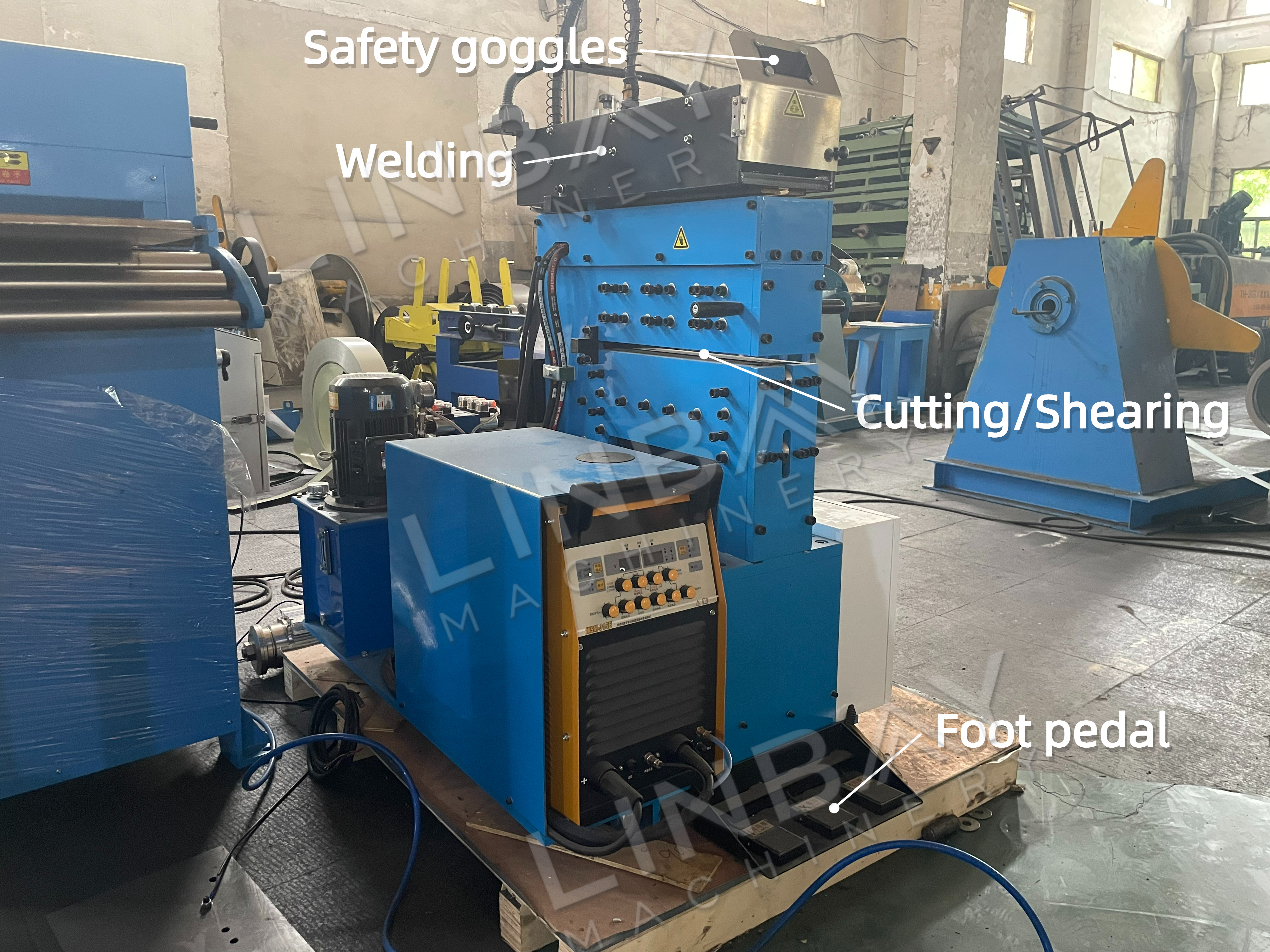
· Connects the last and new steel coils, minimizing feeding time and adjustment steps for new coils.
· Reduces labor costs and material waste.
· Ensures smooth, burr-free shearing for accurate alignment and welding.
· Features automated TIG welding for consistent and strong welds.
· Includes safety goggles on the welding table to protect workers' eyes.
· Foot pedal controls make coil clamping easier.
· Customizable for different coil widths and can be easily integrated into various production lines within its width range.
Standalone Leveler
· Reduces stress and surface imperfections in steel coils through plastic deformation, preventing geometric errors during the forming process.
· Leveling is crucial for coils thicker than 1.5mm that need to be punched.
· Unlike integrated levelers combined with decoilers or roll forming machines, standalone levelers operate at higher speeds.
Punching Part
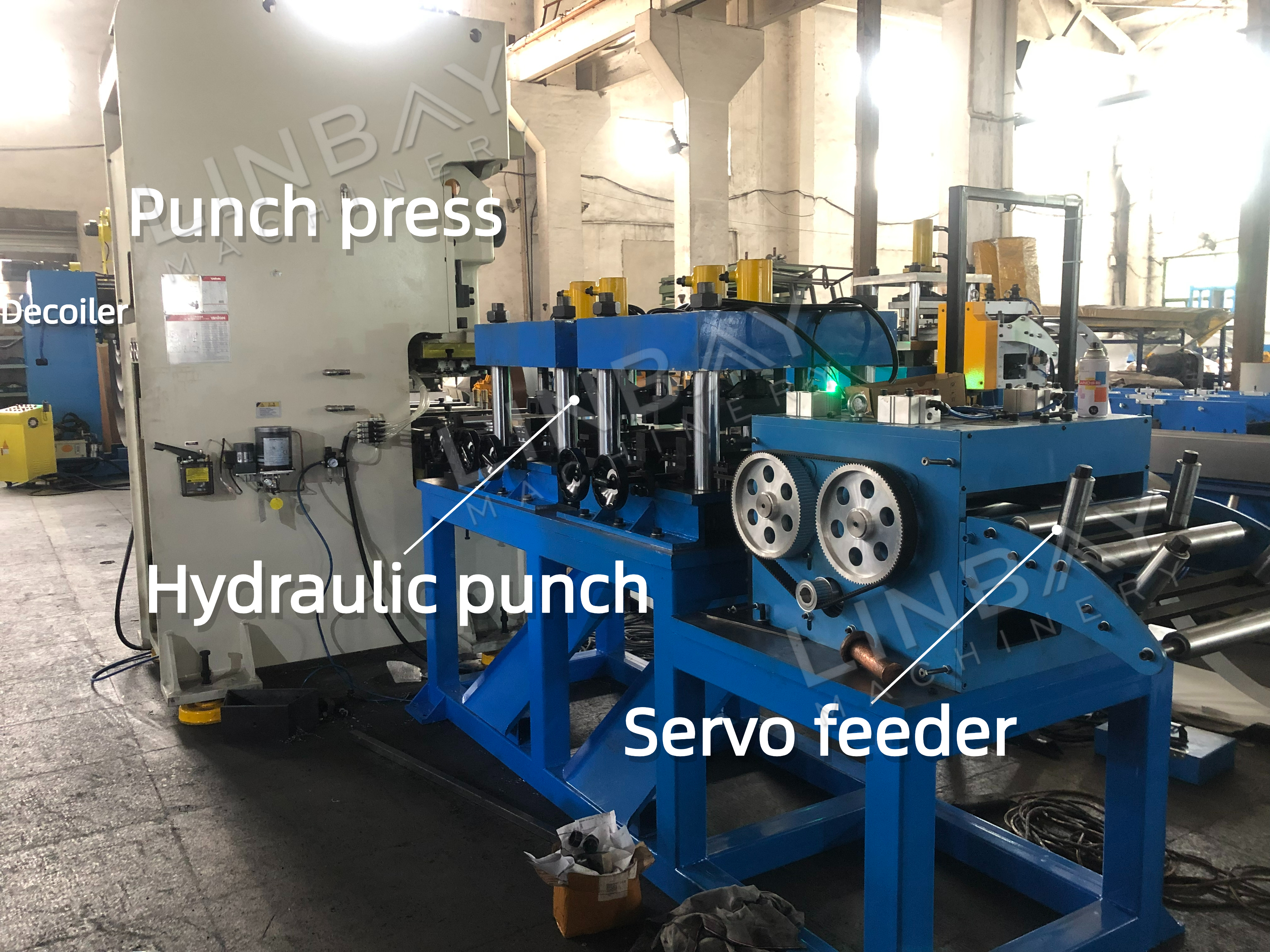
• In this production line, we utilize a combination of punch press and hydraulic punch for hole punching. Our engineering team has crafted an optimal approach for handling complex hole patterns, balancing efficiency and cost by integrating the advantages of both punching machines.
Punch Press
· Fast operation.
· High accuracy in hole spacing during punching.
· Ideal for fixed hole patterns.
Hydraulic Punch
• Offers greater flexibility for various hole patterns. The hydraulic punch can adapt to different hole shapes, adjusting the punching frequency accordingly and selectively punching different shapes with each stroke.
Servo Feeder
The feeder, driven by a servo motor, precisely controls the feeding of steel coils into the punch press or individual hydraulic punch machine. With quick response times and minimal start-stop delays, servo motors ensure accurate feed lengths and consistent hole spacing, greatly reducing waste from misaligned punches. This system is also energy-efficient, drawing power only during active operation, and conserving energy during idle periods. The feeder is fully programmable, allowing for swift adjustments in step distance and punching speed, cutting down on setup times when switching punch molds. Additionally, the internal pneumatic clamping mechanism protects the steel coil’s surface from any potential damage.
Limiter
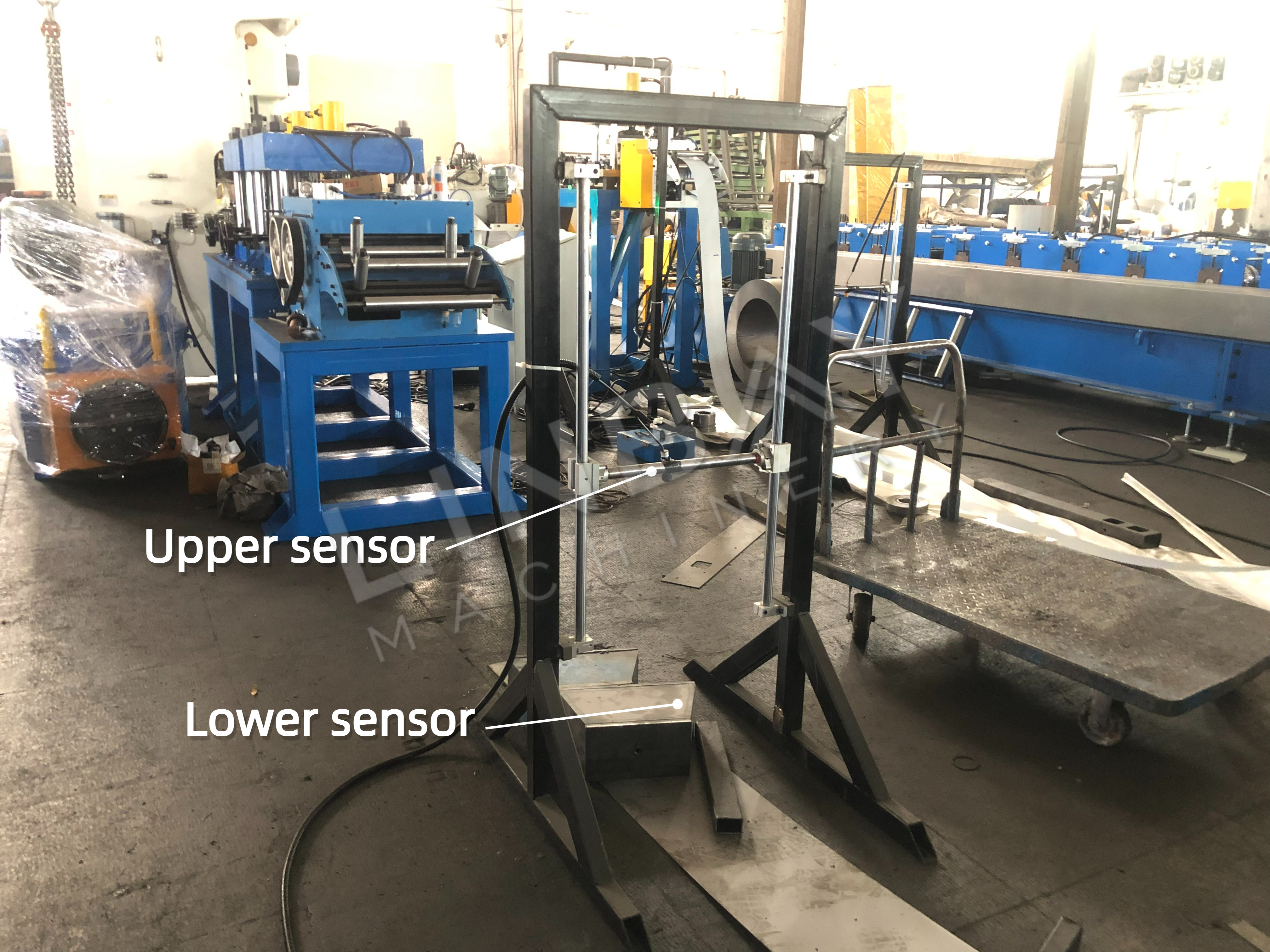
Regulates the pace of production to enhance efficiency and maintain safe operation of both the steel coil and machinery. If the coil comes into contact with the lower sensor, it means that the uncoiling, leveling, and punching processes ahead of the limiter are operating faster than the subsequent forming, welding, and cutting stages. These earlier processes should pause to balance the production flow; otherwise, coil buildup may occur, obstructing its smooth entry into the forming machine and potentially causing deformation. Conversely, if the coil touches the upper sensor, it signals that the later stages are moving faster than the earlier ones, requiring a pause in the processes after the limiter. Failure to do so could result in the coil being pulled into the roll forming machine too quickly, risking damage to the punching machine and forming rollers. Any pause will trigger a notification on the corresponding PLC cabinet display, allowing workers to resume operations by acknowledging the prompt.
Guiding
Primary purpose: Ensures the steel coil is properly aligned with the machine's centerline, avoiding issues like twisting, bending, burrs, and dimensional inaccuracies in the finished product. Guiding rollers are strategically placed at the entry point and within the forming machine. It’s essential to calibrate these guiding devices regularly, especially after transport or prolonged use of the roll forming machine. Prior to dispatch, Linbay's team measures the guiding width and includes this information in the user manual, allowing clients to calibrate the machine upon delivery.
Secondary Leveler (Set on the same base with roll forming machine)
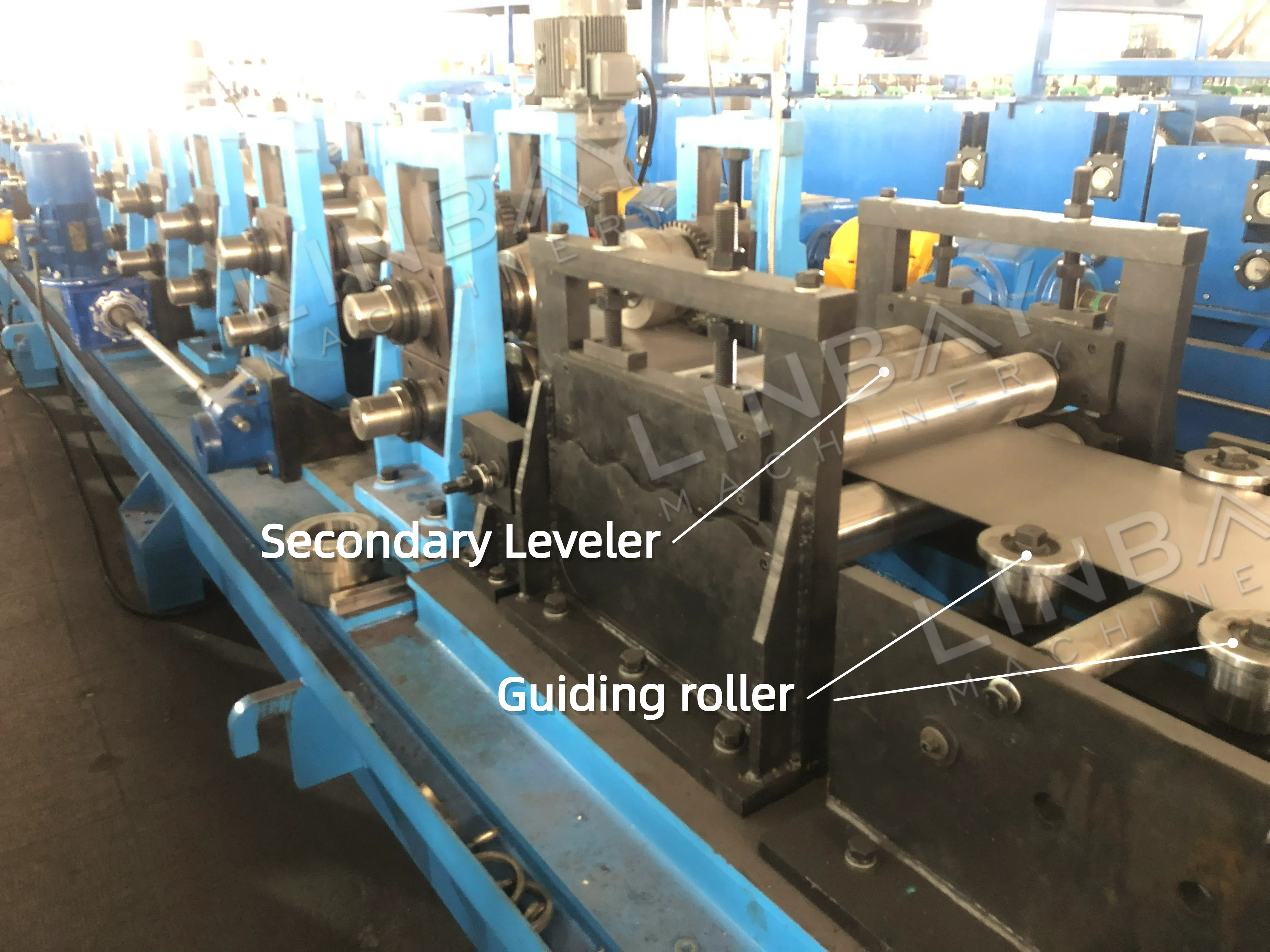
A smoother coil ensures superior seam alignment post-forming, which greatly aids in the welding process. Secondary leveling serves to further improve the leveling quality and reduce stress at punched points. As a supplementary measure, positioning this leveler on the forming machine's base offers a cost-effective and suitable approach.
Roll Forming Machine
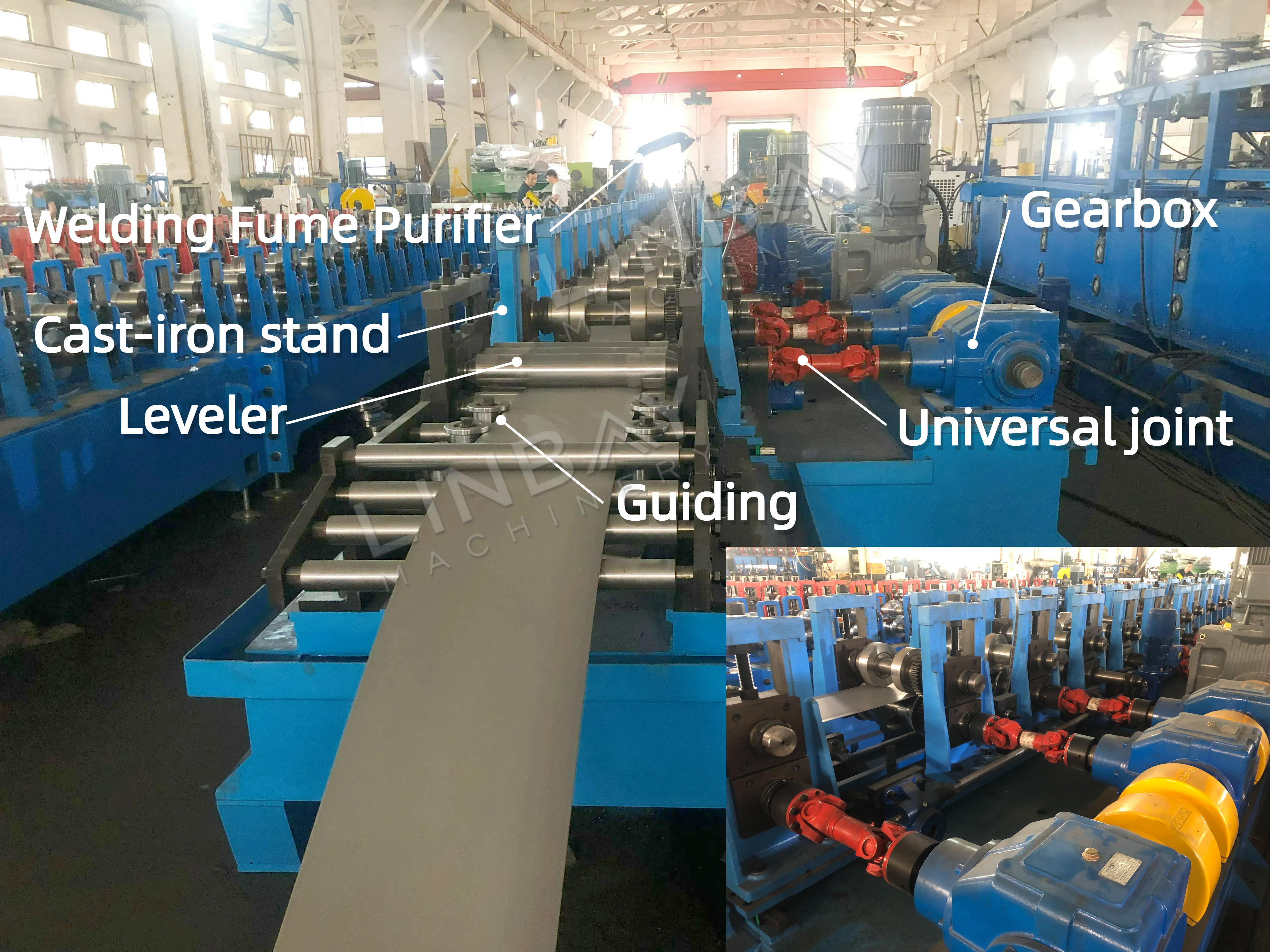
· Versatile Production: This line is capable of manufacturing square tubes with dimensions ranging from 50-100mm in width and 100-200mm in height. (Linbay can also offer customization for other size ranges.)
· Automated Size Change: By setting and confirming the desired size on the PLC screen, the forming stations automatically shift laterally along the guide rails to the precise positions, adjusting the forming point accordingly. This automation enhances accuracy and convenience, reducing the need for manual adjustments and associated costs.
· Lateral Movement Detection: The encoder precisely tracks the lateral movement of the forming stations and instantly relays this data to the PLC, maintaining movement errors within a 1mm tolerance.
· Safety Limit Sensors: Two safety limit sensors are positioned on the outer sides of the guide rails. The inner sensor prevents the forming stations from moving too close together, avoiding collisions, while the outer sensor ensures they don’t move too far out.
· Sturdy Cast-iron Frame: Featuring an independent upright frame made from cast iron, this solid structure is ideal for high-capacity production requirements.
· Powerful Drive System: The gearbox and universal joint deliver robust power, enabling smooth operation when advancing coils thicker than 2mm or at forming speeds exceeding 20m/min.
· Durable Rollers: Chrome-plated and heat-treated, these rollers resist rust and corrosion, ensuring a longer lifespan.
· Main Motor: The standard configuration is 380V, 50Hz, 3-phase, with options for customization available.
Laser Weld
· Enhanced Quality and Precision: Delivers superior accuracy and a robust connection.
· Neat and Polished Joint: Ensures a clean, smooth finish at the joint.
Welding Fume Purifier
• Odor and Fume Control: Effectively captures and removes odors and fumes produced during welding, ensuring a safer factory environment and safeguarding workers' health.
Flying Saw Cut
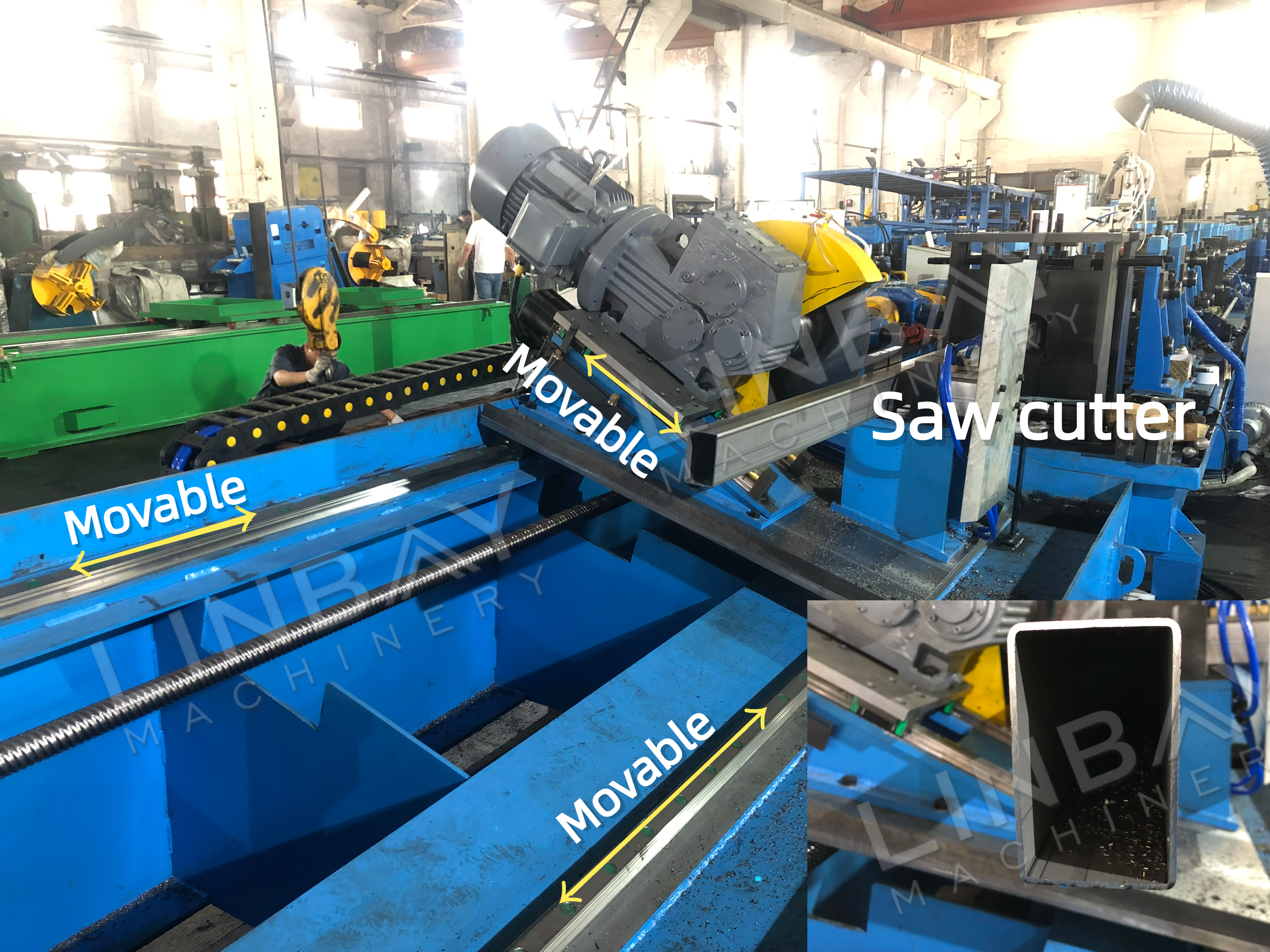
· Flying Cut: The cutting unit synchronizes with the roll forming machine’s speed during operation, boosting production efficiency and output.
· Precision Cutting: With a servo motor and motion controller, the cutting unit maintains an accuracy of ±1mm.
· Sawing Method: Delivers precise cuts without deforming the edges of the square-closed profiles.
· Material Efficiency: Each cut generates minimal waste, reducing material costs.
· Flexible Operation: Unlike other cutting methods that require specific blades for different sizes, saw cutting is adaptable, offering cost savings on blades.
1. Decoiler
2. Feeding
3.Punching
4. Roll forming stands
5. Driving system
6. Cutting system
Others
Out table