Profile
The ridge cap secures the seam where the two roof slopes meet, effectively shielding the area from rain and dust. These caps are available in various shapes to complement different styles of metal roofing panels and are made from 0.3-0.6mm color-coated steel, PPGI, and galvanized steel.
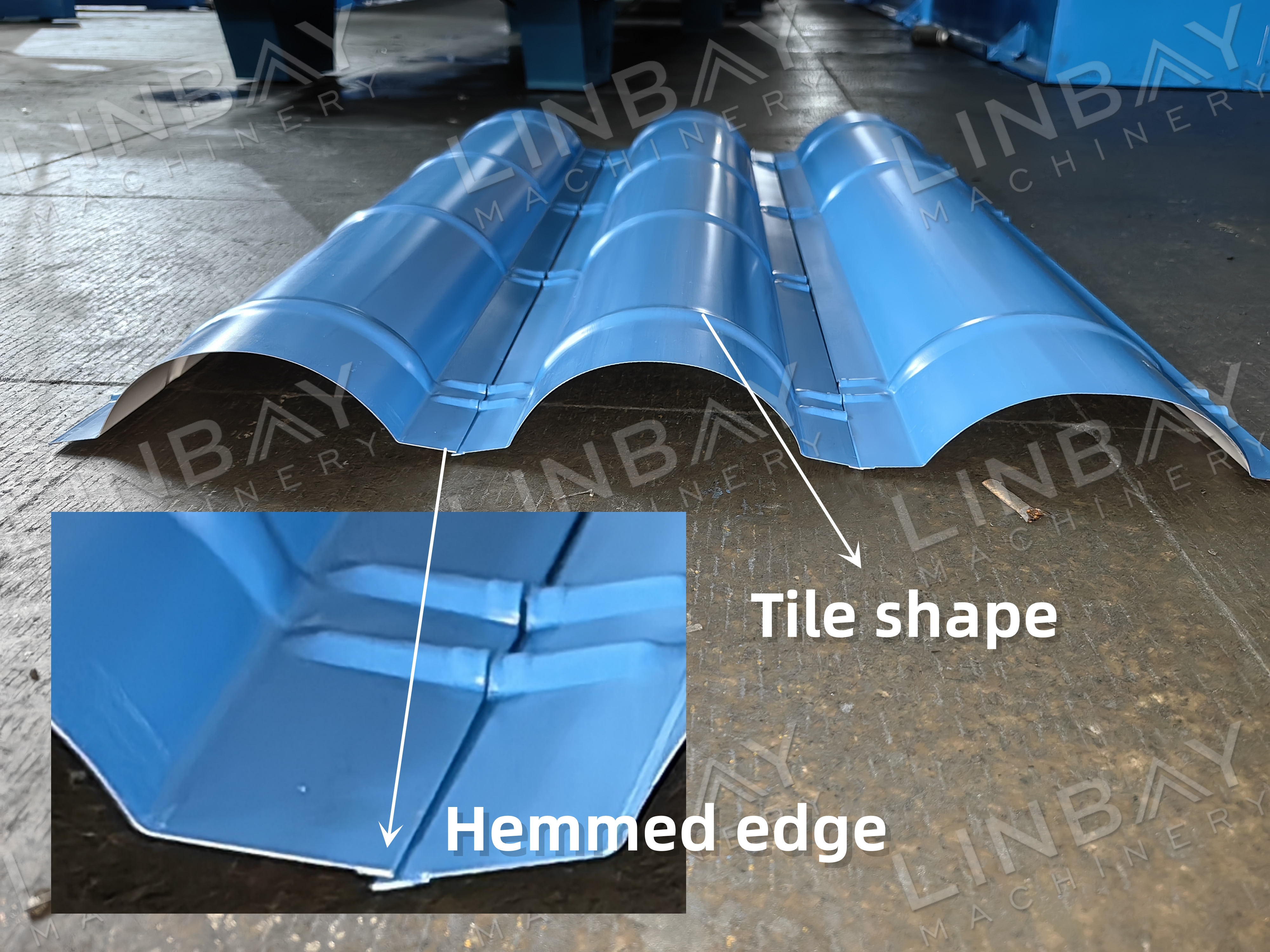
Real case-Main Techinical Parameters
Flow chart: Decoiler--Guiding--Roll forming machine--Hydraulic punch--Hydraulic cut--Out table

Real case-Main Technical Parameters
· Adjustable line speed: 0-10m/min
· Compatible materials: Color-coated steel, galvanized steel, and PPGI
· Material thickness range: 0.3-0.6mm
· Roll forming machine type: Wall-panel structure
· Drive system: Chain mechanism
· Cutting system: Hydraulic cutting, with the roll former halting during the cutting process
· PLC control: Siemens system
Real case-Machinery
1.Manual decoiler*1(We also offer electrical and hydraulic decoiler, know more in DESCRIPTION below)
2.Roll forming machine*1
3.Hydraulic punch machine*1
4.Hydraulic cutting machine*1
5.Out table*2
6.PLC control cabinet*1
7.Hydraulic station*1
8.Spare parts box(Free)*1
Real case-Description
Decoiler
The decoiler is available in manual, electric, and hydraulic versions, selected according to the steel coil's thickness, width, and weight. A manual decoiler is adequate to securely support a 0.6mm thick coil, ensuring smooth and steady uncoiling.
The central shaft of the uncoiler, also known as the core expansion device, is designed to hold the steel coil, with the ability to expand or contract to accommodate inner diameters ranging from 460-520mm, ensuring secure and smooth uncoiling. Additionally, an outward coil retainer is included to prevent the coil from slipping off, enhancing worker safety.
Guiding
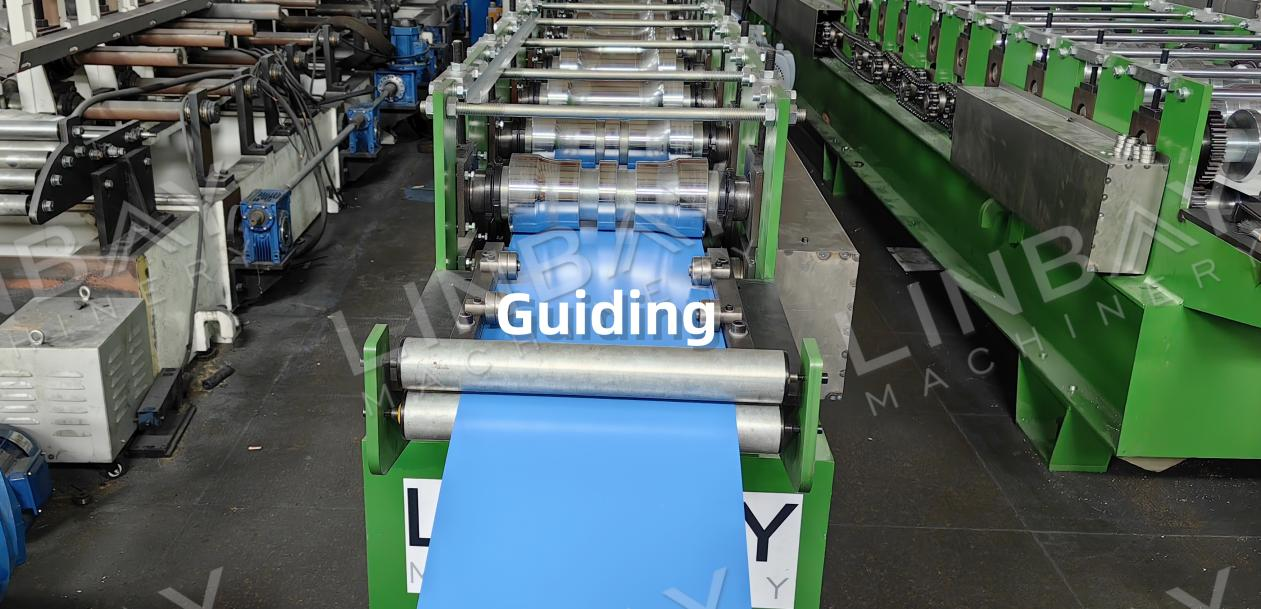
Guide rollers help the steel coil smoothly enter the roll forming machine, ensuring alignment with the centerline of the other machines. This alignment is crucial for maintaining the straightness of the ridge cap and ensuring precise forming pressure points.
Roll forming machine
The wall panel structure combined with the chain-driven system efficiently shapes thin sheets ranging from 0.3-0.6mm in thickness, offering a cost-effective solution. The chain is enclosed in an iron casing, providing protection for workers and shielding the chains from debris damage. As the steel coil passes through the forming rollers, it is subjected to pressure and tensile forces, resulting in the desired shape.
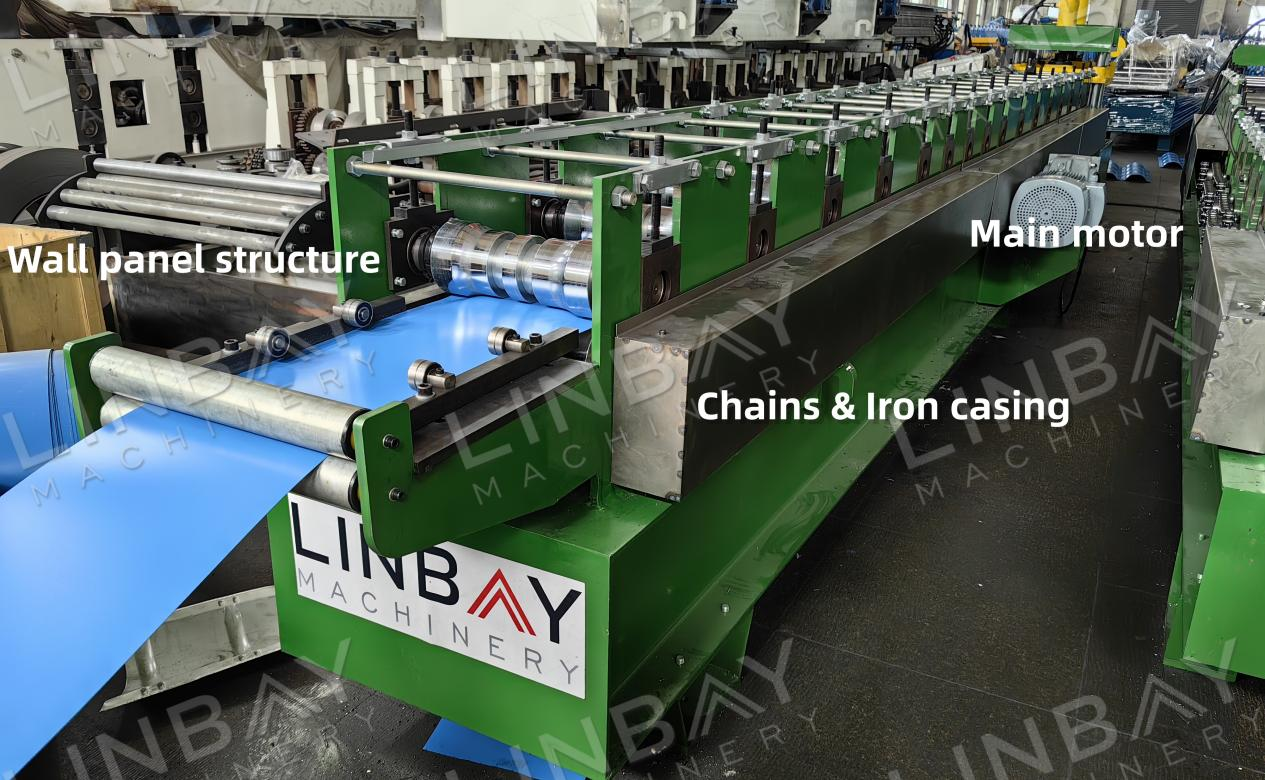
The system includes 16 forming stations, each precisely crafted based on the client's specifications, taking into account the wave height, arc radius, and straight edges on both sides of the ridge cap. These stations are designed to prevent any scratching of the coil surface or damage to the paint coating.
This ridge cap includes hemmed edges to enhance safety by reducing sharpness and protecting workers from injury. The hemmed design also hides the metal edge, preventing edge creep and reducing the risk of rust formation at the ridge cap edge.
Stamping
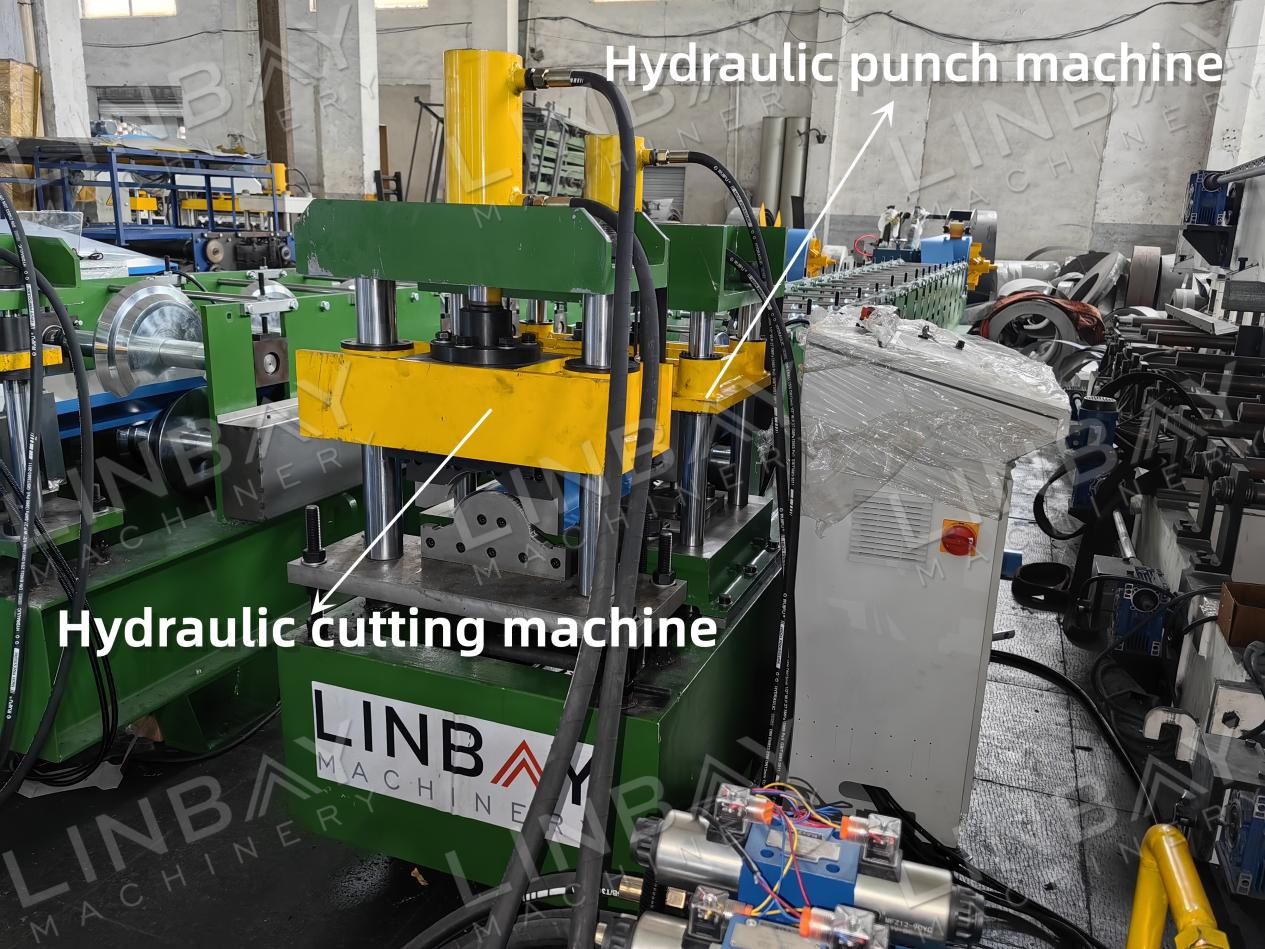
Once formed, the steel coil takes on a semi-circular shape. Next, a hydraulic punch machine is employed to stamp the raised pattern onto the tile. This process not only shapes the tile but also enhances the longitudinal strength of the ridge cap. The stamping frequency can be adjusted via the PLC screen, and the stamping mold can be customized to match your specifications.
Encoder, PLC Control Cabinet, & Hydraulic cutting
The encoder accurately measures the advancing steel coil's length and converts this measurement into an electrical signal sent to the PLC control cabinet. Operators can configure production speed, batch size, and cutting length directly from the PLC cabinet screen. Thanks to the precise feedback from the encoder, the hydraulic cutting machine can maintain a cutting length error within ±1mm. Additionally, the cutting blades are custom-designed according to the provided drawings, ensuring clean, deformation-free edges and eliminating burrs.
1. Decoiler
2. Feeding
3.Punching
4. Roll forming stands
5. Driving system
6. Cutting system
Others
Out table