video
Profile
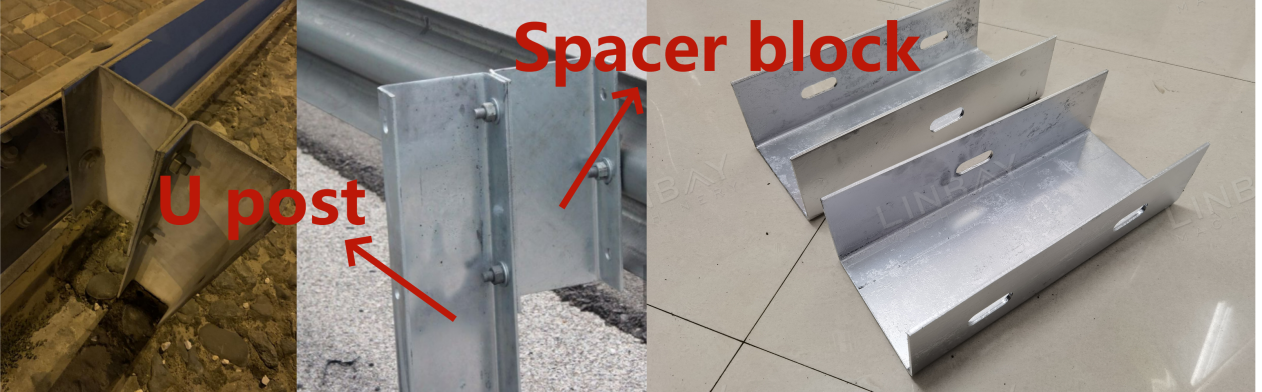
The profiles produced on this production line are all in U-shaped forms, specifically the U post and spacer block within the guardrail system. The spacer block acts as a resistance block positioned between the post and guardrail beam, offering cushioning upon impact.
Typically, U posts and spacer blocks are crafted from 5mm cold-rolled or hot-rolled steel, with hole punching conducted prior to the forming process. These holes are designated for screw and nut installation purposes.
Real case-Main Techinical Parameters
Flow chart

5T Hydraulic decoiler--Guiding--Leveling--Hydraulic punch--Roll forming machine--Hydraulic cut--Out table
Main Technical Parameters:
1. Line speed: Adjustable from 0 to 6m/min
2. Profiles: U post channel and Spacer
3. Material thickness: 5mm (for this application)
4. Suitable materials: Hot rolled steel, cold rolled steel
5. Roll forming machine: Cast-iron structure with a gearbox driving system
6. Number of forming stations: 16
7. Punching system: Hydraulic; roll former stops during punching
8. Cutting system: Hydraulic; roll former stops during cutting
9. PLC cabinet: Equipped with Siemens system
Real case-Description
Hydraulic decoiler
Engineered with both efficiency and safety in mind, the hydraulic decoiler is powered by a robust hydraulic station. Equipped with an outward coil retainer, it effectively prevents the steel coil from slipping off during operation. Additionally, the press arm securely holds the coil in place, thereby ensuring worker safety by preventing any unexpected spring-ups.
Leveler
By alleviating internal stress within the coils, the leveler optimizes them for punching and forming processes. Integrated with the forming machine base, the leveler not only improves efficiency but also saves valuable floor space and reduces land costs in your production line setup.
Hydraulic punch
The hydraulic punch can efficiently punch holes in steel coils up to 5mm thick, preparing them for screw installations. Connected to the roll forming machine base, it guarantees precise operations, albeit requiring brief pauses during punching.
For enhanced production speeds, a standalone hydraulic punch solution is also available.
Roll forming machine
At the core of the production line is the roll forming machine, boasting a robust cast-iron structure capable of effortlessly handling 5mm thick steel coil forming. All roll forming rollers are powered by the gearbox system and crafted from Gcr15, a high-carbon chromium-bearing steel, providing exceptional hardness and wear resistance, further augmented by chrome plating. Additionally, heat-treated 40Cr shafts ensure durability and reliability even under the most demanding conditions.
Encoder & PLC
Precision and control are seamlessly integrated with the encoder and PLC system. Converting steel coil length into electrical signals, the encoder offers accurate feedback to the PLC control cabinet. Parameters such as production speed, quantity per cycle, and cutting lengths can all be configured on the PLC control cabinet, ensuring cutting errors are limited within ±1mm. Customers can set the cutting length according to their requirements through the operation panel.
Hydraulic cut
Each cut yields smooth, burr-free edges, eliminating waste and ensuring impeccable precision, which ultimately saves costs for customers. It's worth noting that the roll forming machine pauses during each cutting operation.
We also provide a higher-speed solution where the roll forming machine does not stop during cutting, should you require it.
Hydraulic station
Efficiency combines with reliability through our cutting-edge hydraulic station. Featuring cooling electric fans, it effectively dissipates heat, sustaining optimal working temperatures for prolonged operations. With minimal failure rates, our hydraulic stations ensure durability and longevity, guaranteeing uninterrupted production workflows.
1. Decoiler
2. Feeding
3.Punching
4. Roll forming stands
5. Driving system
6. Cutting system
Others
Out table