video
Profile
The upright offers vertical support and structural integrity to shelving and racking systems. It is designed with perforations for adjustable beam placement, enabling flexible shelf heights. Uprights are usually made from cold-rolled or hot-rolled steel, with a thickness ranging from 2 to 3mm.
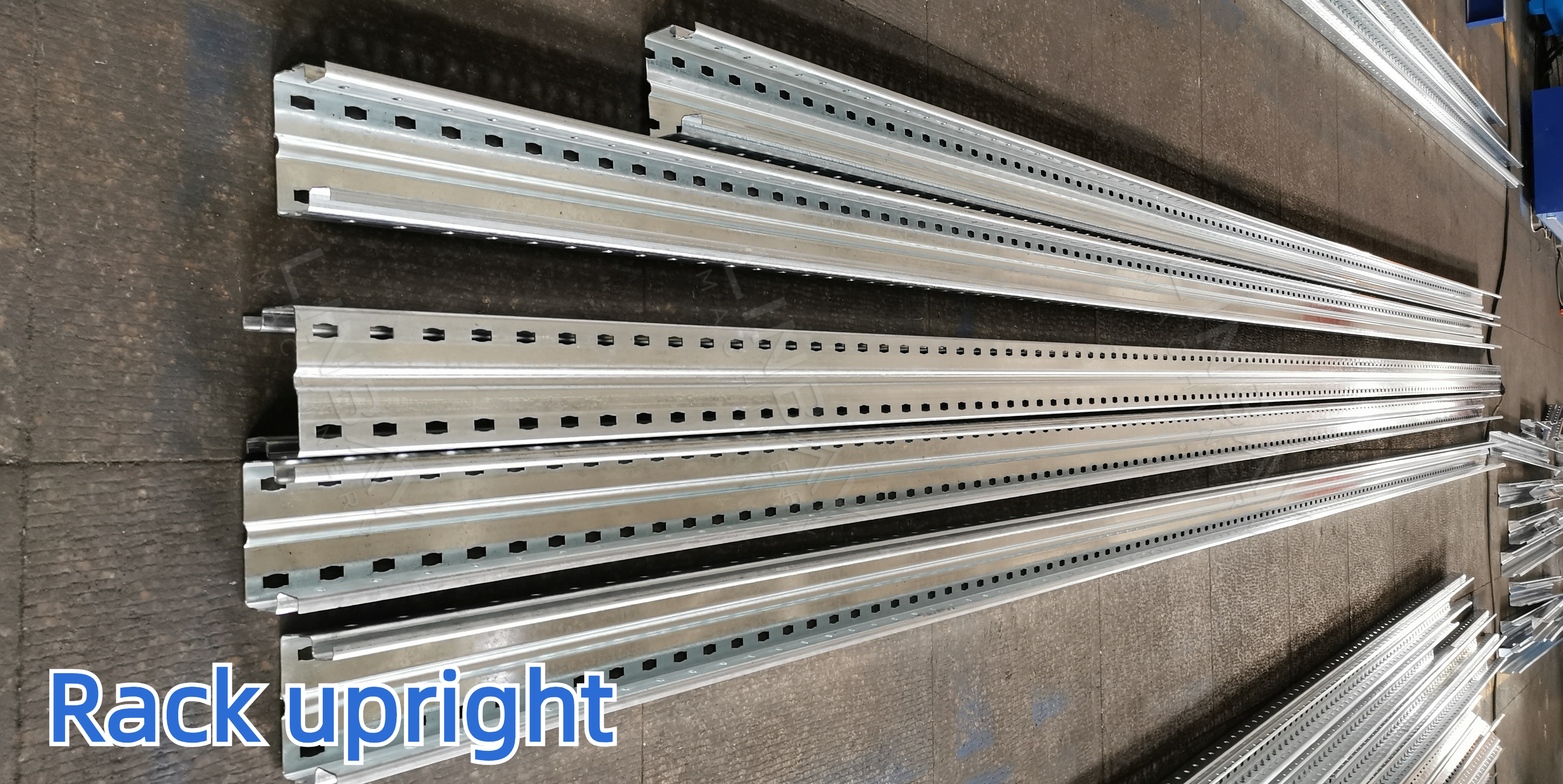
Real case-Flow chart
Flow chart: Hydraulic decoiler--Leveler--Servo feeder--Hydraulic punch--Limiter--Guiding--Roll forming machine--Flying hydraulic cutting--Out table

Real case-Main Technical Parameters
1.Line speed: 0-12m/min, adjustable
2.Suitable material:Hot rolled steel, cold rolled steel, galvanized steel
3.Material thickness:2-3mm
4.Roll forming machine: Cast-iron structure
5.Driving system: Gearbox driving system
6.Cutting system: Flying cutting machine, the roll forming machine doesn’t stop when cutting.
7.PLC cabinet: Siemens system.
Real case-Machinery
1.Hydraulic decoiler*1
2.Leveler*1
3.Servo feeder*1
4.Hydraulic punch machine*1 (Typically, each size requires a separate mold.)
5.Roll forming machine*1
6.Hydraulic cutting machine*1 (Typically, each size requires a separate blade.)
7.Out table*2
8.PLC control cabinet*1
9.Hydraulic station*2
10.Spare parts box(Free)*1
Real case-Description
Hydraulic Decoiler
The hydraulic decoiler automates the coil unwinding process, minimizing manual intervention and enhancing efficiency. It is equipped with advanced safety features, such as the press-arm and coil outward retainer, which prevent the steel coil from falling off or springing up.
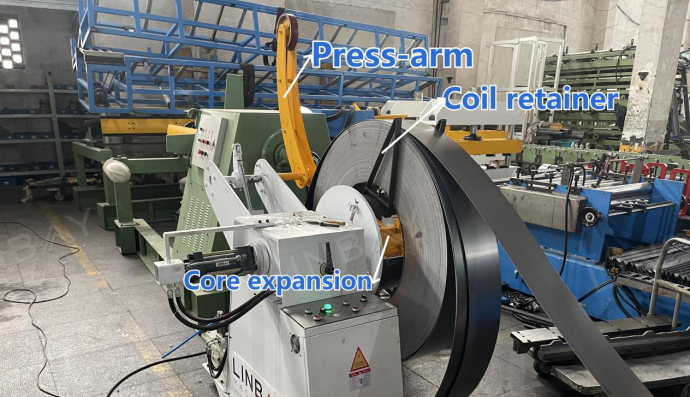
Leveler
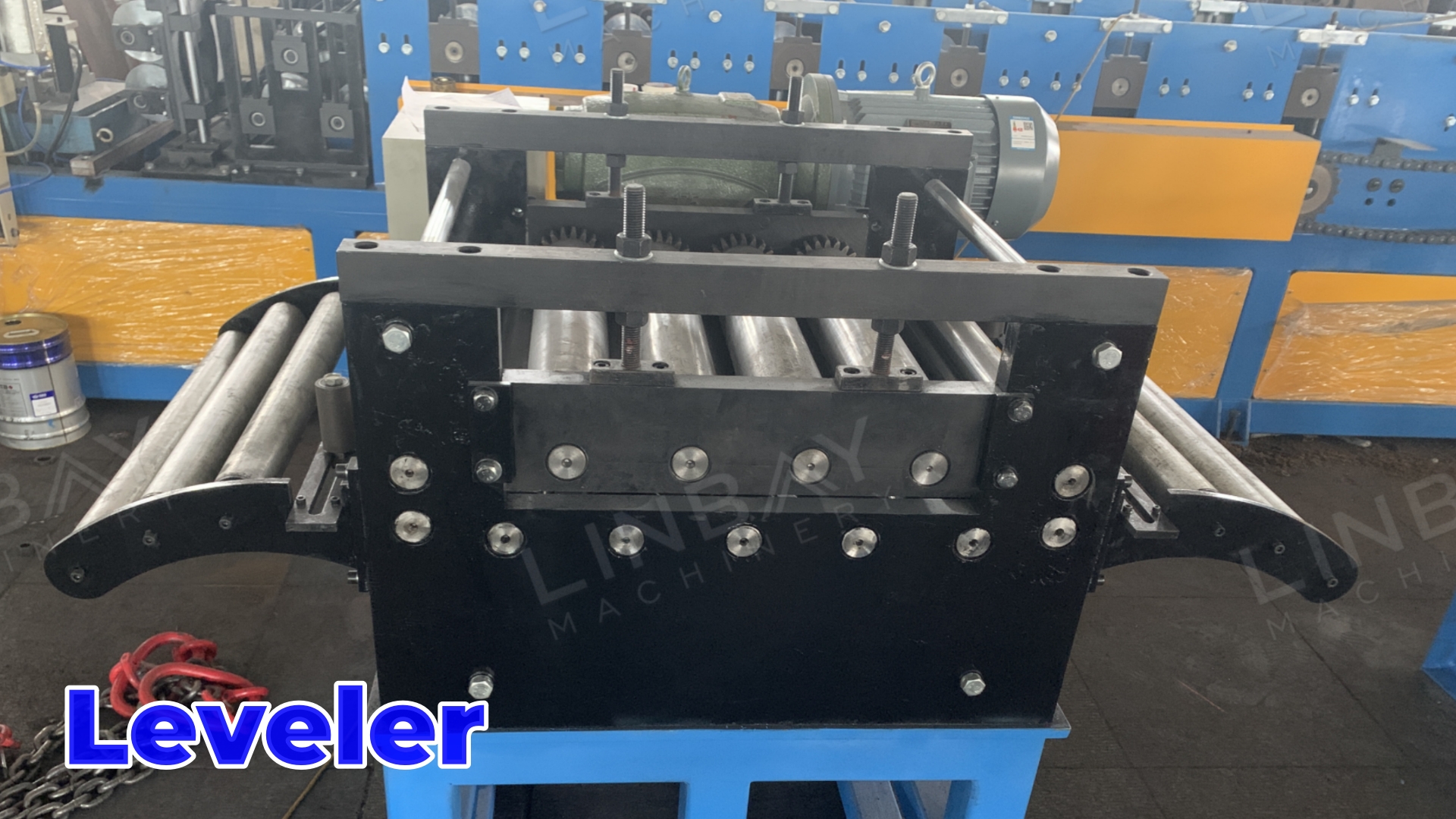
The leveler smooths out the steel coil and releases internal stress, aiding in shape forming and precise punching. The shape of the rack upright significantly influences its load-bearing performance.
Hydraulic Punch & Servo Feeder
The feeder is powered by a servo motor, ensuring minimal start-stop time delay and precise control of the steel coil's forward length, accurately spacing each hole. Inside the feeder, pneumatic feeding is used to protect the surface of the steel coil from scratches.
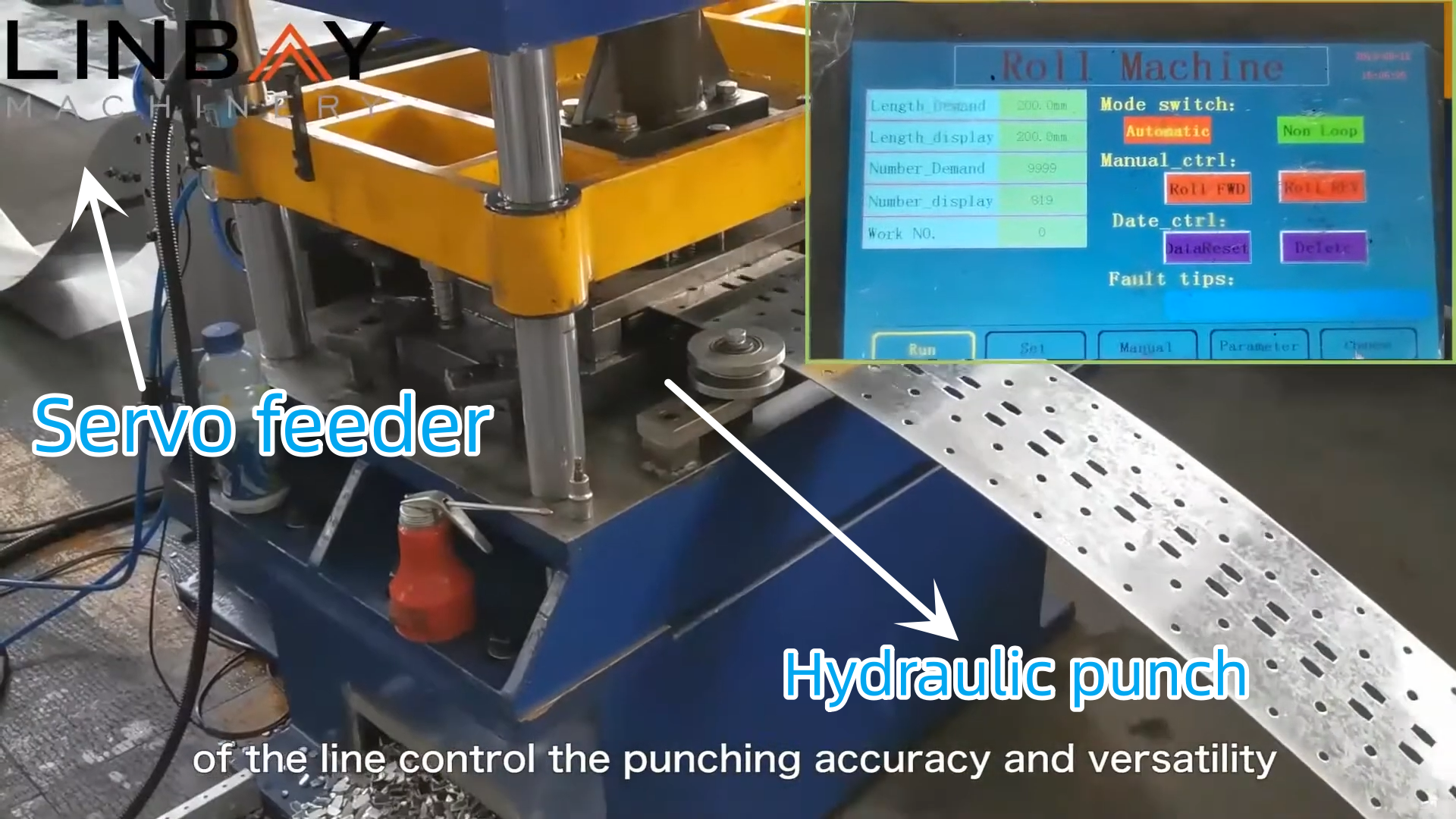
The hydraulic punch operates using power from a hydraulic station. When the standalone hydraulic punch machine is in use, other parts of the production line can continue to function without interruption.
The standalone hydraulic punching machine provides space to store the steel coil between the punching and forming stages. While punching, the forming machine can continue operating, thereby enhancing the overall efficiency and output of the production line. It is important to note that when producing uprights of different sizes, the molds must be changed accordingly.
Guiding
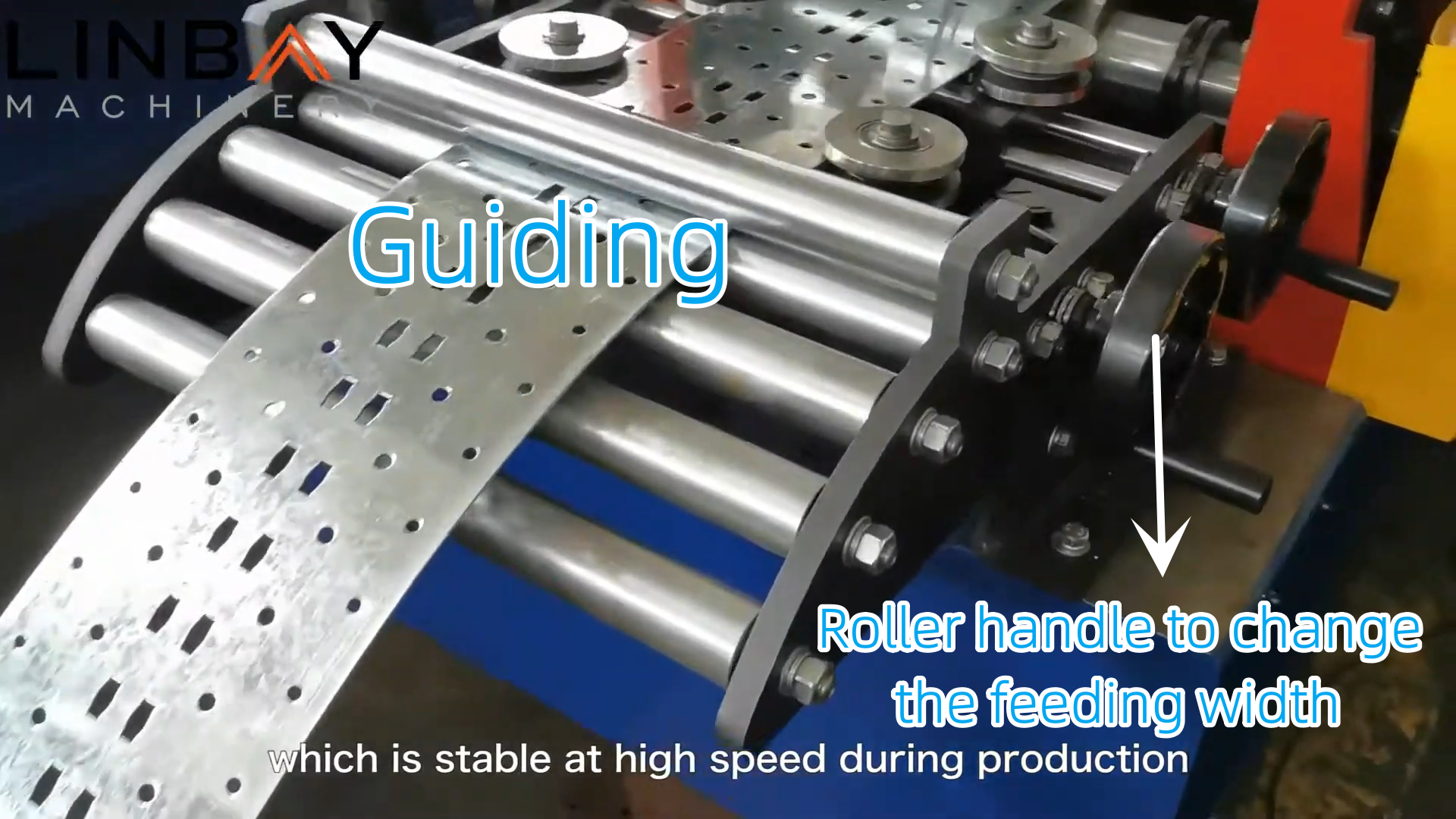
Guiding rollers keep the steel coil and machine aligned along the same centerline, preventing distortion during the forming process. The upright is a crucial component that supports the stability of the rack frame, and its straightness directly impacts the overall stability of the shelf.
Roll Forming Machine

This roll forming machine features a cast-iron structure and a gearbox driving system. It can produce multiple sizes by manually adjusting the rollers. Additionally, we offer more automated solutions where the forming stations automatically adjust to change sizes.
Regardless of the automation level, our forming machines are capable of producing rack uprights with high straightness and precise alignment with the drawings.
PLC Control Cabinet & Encoder&Flying Hydraulic Cutting Machine
Encoders play a crucial role in delivering essential feedback on position, speed, and synchronization. They convert the measured length of the steel coil into electrical signals, which are then transmitted to the PLC control cabinet.
The control cabinet display allows adjustment of production speed, output per cycle, cutting length, and other parameters. Thanks to precise measurements and feedback from the encoder, the cutting machine can maintain a cutting accuracy within ±1mm.
This hydraulic cutting machine generates no waste with each cut, helping to save on material costs. However, each size of upright requires a separate blade.
The cutting machine moves back and forth at the same speed as the roll forming machine, allowing the production line to operate continuously without interruption.
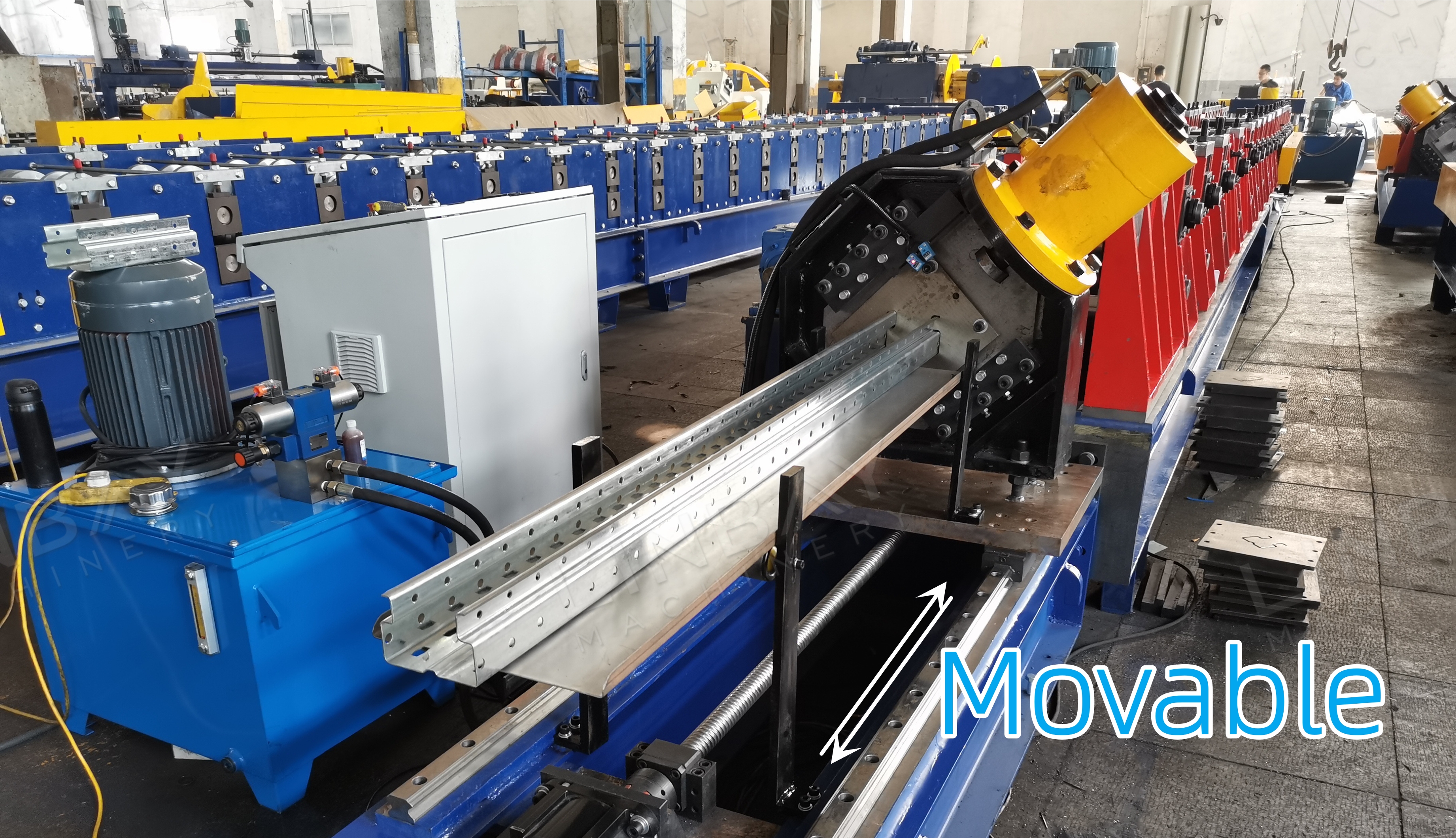
Hydraulic Station
The hydraulic station supplies essential hydraulic power for operating equipment such as the hydraulic decoiler and cutter. Equipped with cooling fans for effective heat dissipation, it ensures continuous operation and enhances productivity. Known for its reliability and low failure rates, this hydraulic station is built for durability and long-term performance.
In hot climates, we recommend expanding the hydraulic reservoir size to enhance heat dissipation and increase the volume of fluid available for effective heat absorption.
By adopting these measures, the hydraulic station can maintain a stable operating temperature even during extended use, ensuring the roll forming production line's reliability and efficiency.
1. Decoiler
2. Feeding
3.Punching
4. Roll forming stands
5. Driving system
6. Cutting system
Others
Out table