PROFILE
Awning round tubes are essential components for awnings, typically constructed from aluminum or galvanized steel. Standard diameters include 60/63/70/78/80/85mm, and they are commonly available in lengths of 4, 5, 6, or 7 meters.
Conventional production method: Steel coils are wound around a cylindrical mold and then compressed to form a round tube. This approach results in uneven force distribution, low efficiency, and limitations on both tube length and minimum diameter. Furthermore, it is difficult to create tubes with non-standard rounded edge designs, as shown in the image below.
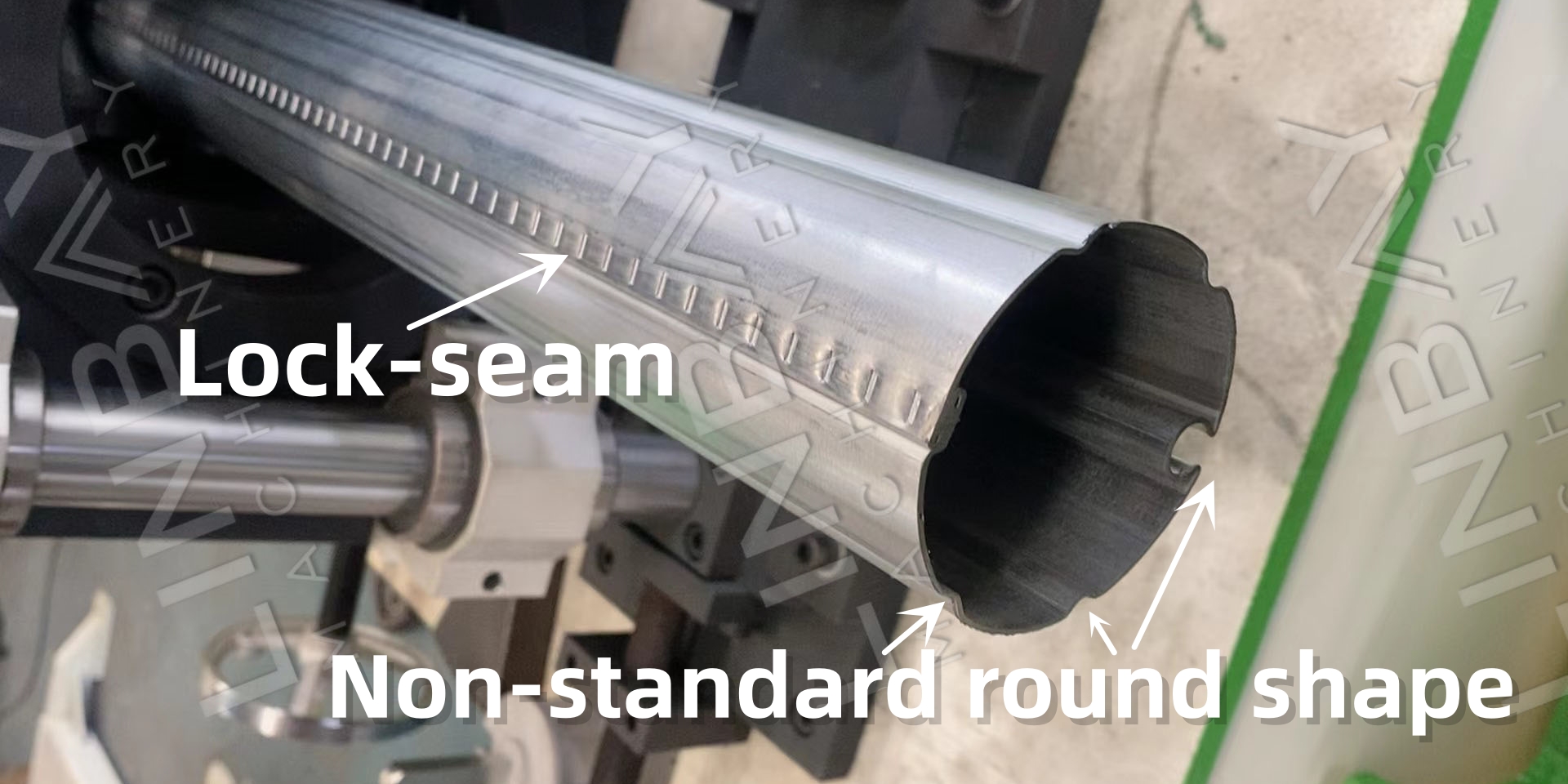
New Approach: Roll Forming Machine. The roll forming process gradually shapes the material with each roller, incrementally bending it until it becomes a round, lock-seamed tube. This uniform force distribution minimizes springback. Steel coils can be continuously fed without needing manual pre-cutting, and the tube lengths can be precisely cut with an accuracy of ±1mm. This method is ideal for producing smaller diameter tubes and custom edge designs. It's an efficient and economical solution for clients.
REAL CASE-MAIN TECHNICAL PARAMETERS
Flow chart: Decoiler--Guiding--Roll former--Flying saw cut--Out table
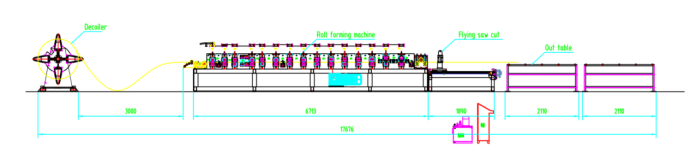
REAL CASE-MAIN TECHNICAL PARAMETERS
1.Line speed: 0-10m/min, adjustable
2.Suitable material: Galvanized steel, aluminum
3.Material thickness: 0.8-1mm
4.Roll forming machine: Cast-iron structure
5.Driving system: Gearbox driving system with universal joint cardan shaft.
6.Cutting system: Flying saw cut, roll former doesn’t stop when cutting.
7.PLC cabinet: Siemens system.
REAL CASE-MACHINERY
1.Manual Decoiler*1
2.Roll forming machine*1
3.Flying saw cutting machine*1 (Including saw blade*1)
4.Out table*2
5.PLC control cabinet*1
6.Hydraulic station*1
7.Spare parts box(Free)*1
REAL CASE-DESCRIPTION
Manual Decoiler
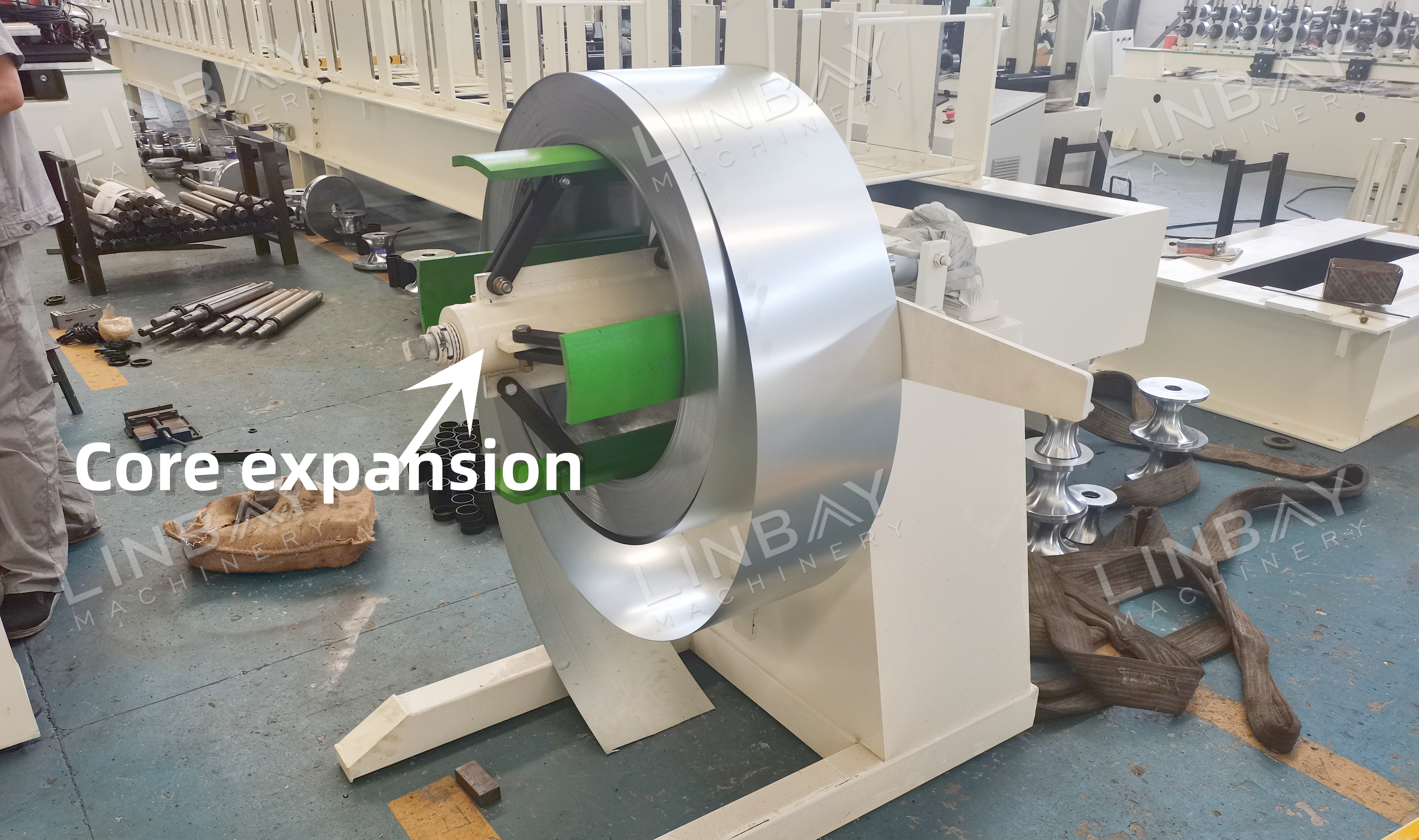
· Sturdy Frame: The frame is built to be strong and stable, specifically engineered to support steel coils securely.
· Mandrel Expansion: The mandrel or arbor can be manually adjusted to expand and accommodate steel coils with an inner diameter ranging from 490-510mm. This ensures the coil is held firmly for smooth decoiling.
· Coil Retainer: This component is designed to prevent the steel coil from slipping off the mandrel. It's simple to attach and remove.
· Available Options: For enhanced power and automation, electric or hydraulic versions of the core expansion device are available. However, the manual version is preferred for awning round tubes due to the thinner and narrower steel coils involved.
Guiding
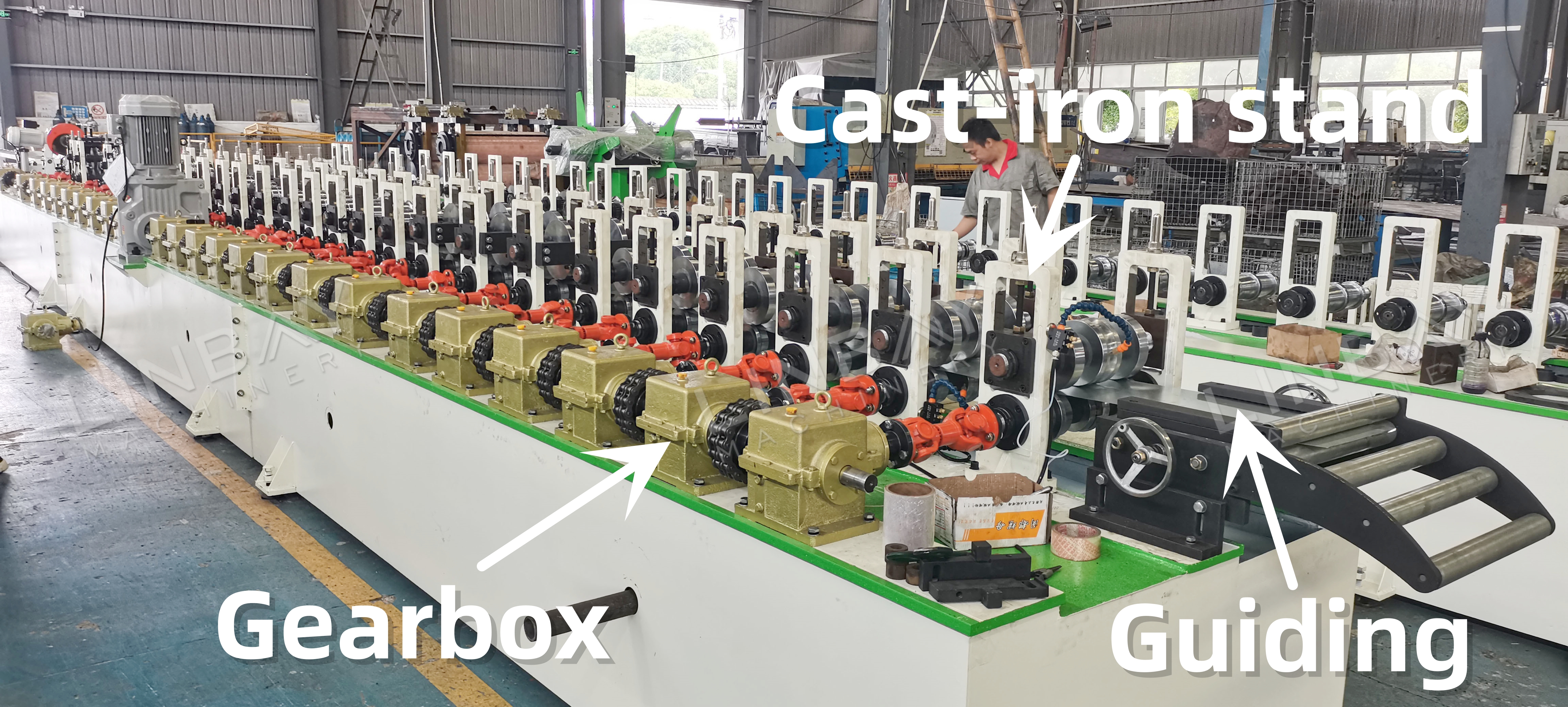
· Primary Role: Maintains precise alignment of the steel coil with the machine's centerline, preventing issues like twisting, bending, and burr formation. Accurate alignment is crucial for ensuring that the seams of the awning round tubes are tight and secure.
· Multiple Guiding Systems: Located not just at the feeding point but also throughout the forming machine to ensure the tube remains straight during production.
· Routine Calibration: Regular calibration of the guiding systems is necessary, especially after transportation or extended periods of use.
· Pre-Shipment Documentation: The Linbay team carefully measures and records the guiding width before shipment, providing these details in the user manual to facilitate accurate calibration upon the client's receipt.
Roll Former
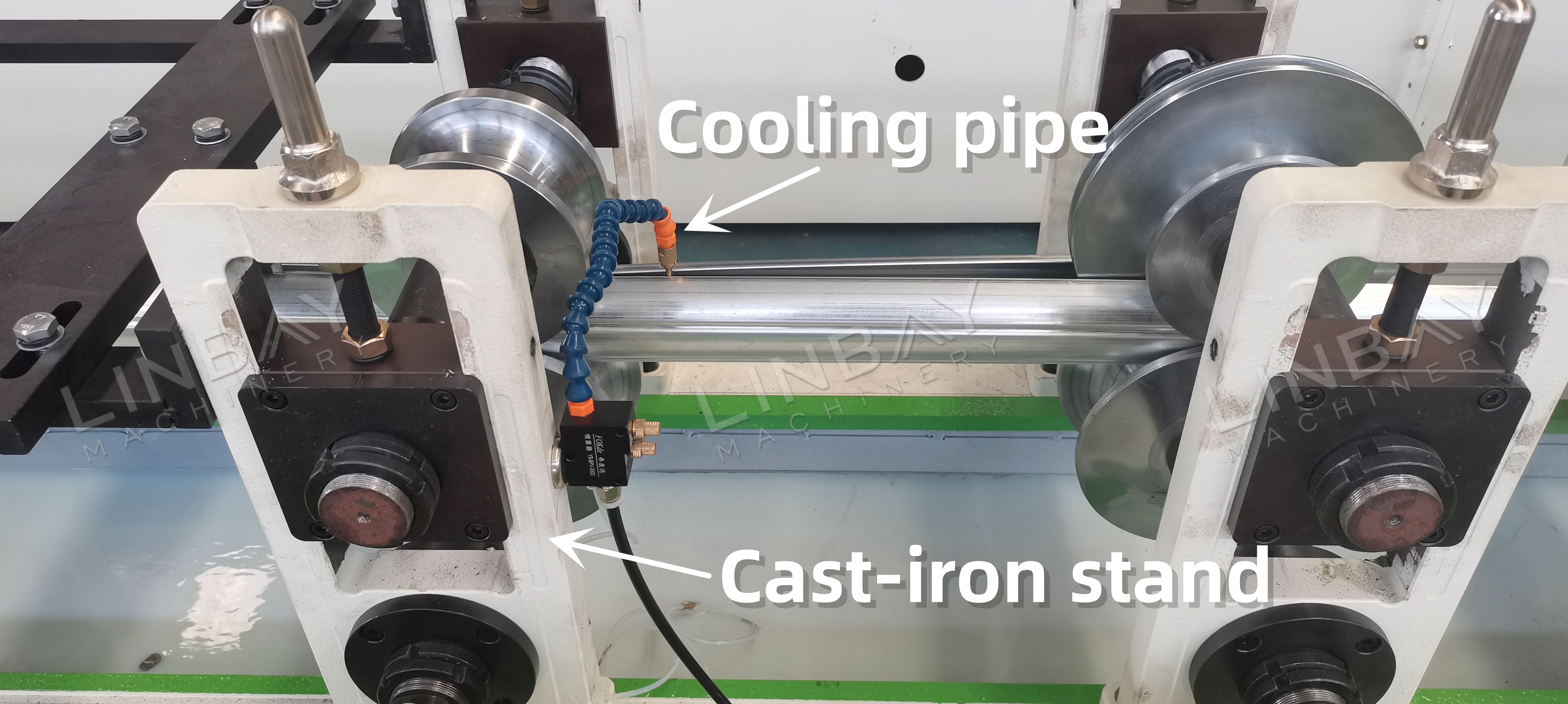
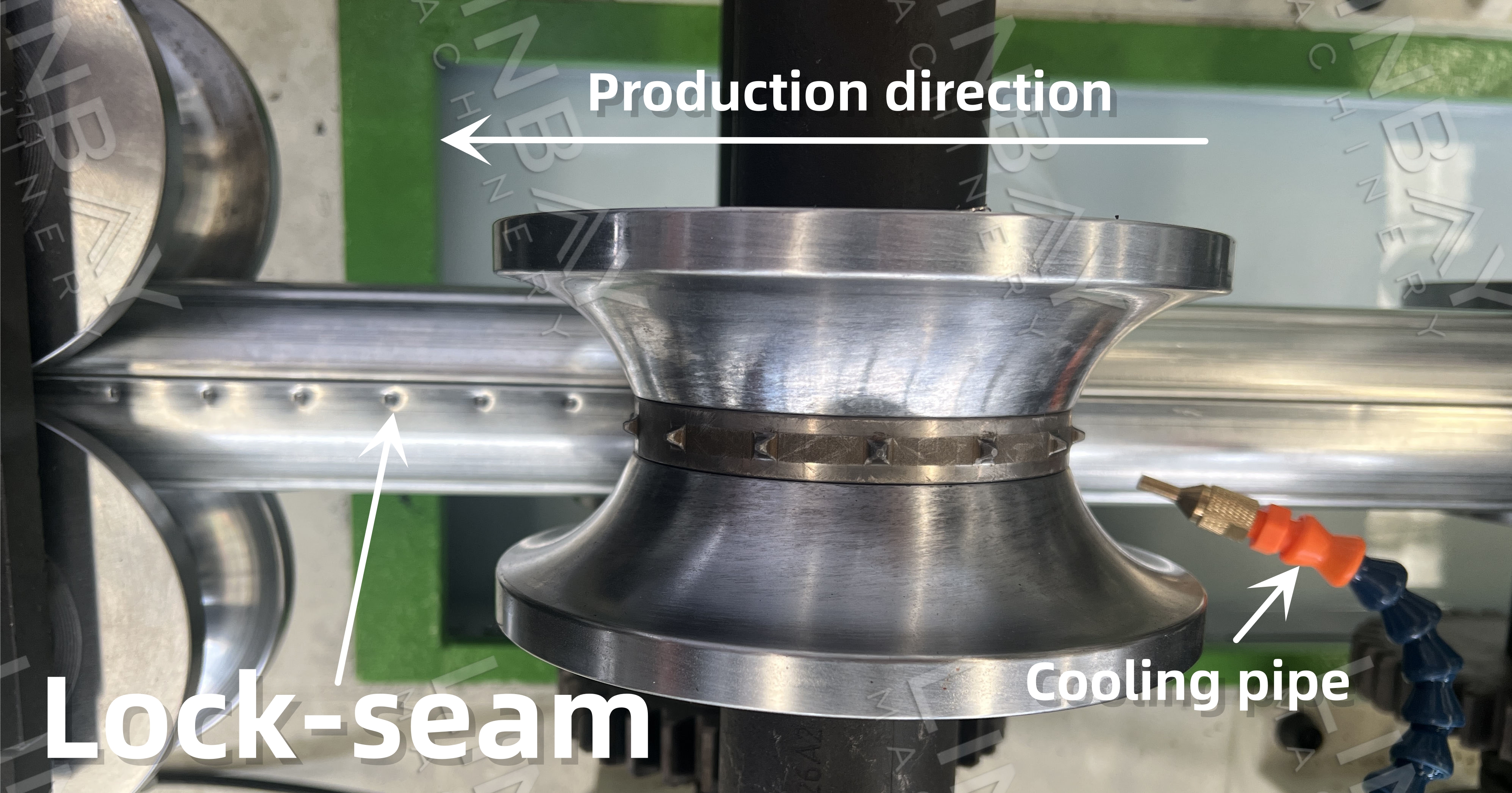
· Robust Construction: Features a cast-iron stand for enhanced durability.
· Powerful Drive System: Equipped with a gearbox and universal joint that deliver strong driving force to the rollers, ensuring smooth and consistent forming of steel coils.
· Flexible Production: A single roll forming machine base accommodates different cassettes, each tailored to specific round tube diameters. Simply switch cassettes to produce tubes of varying sizes.
· Cost Efficiency: Offers a more economical solution by eliminating the need for separate production lines for different tube diameters.
· Secure Seam: Guarantees a tight lock seam that remains intact, preventing any potential seam failures.
· Sustainable Cooling System: Utilizes a recirculating coolant system to keep roller temperatures low, enhancing forming quality and prolonging roller life.
Flying Saw Cut
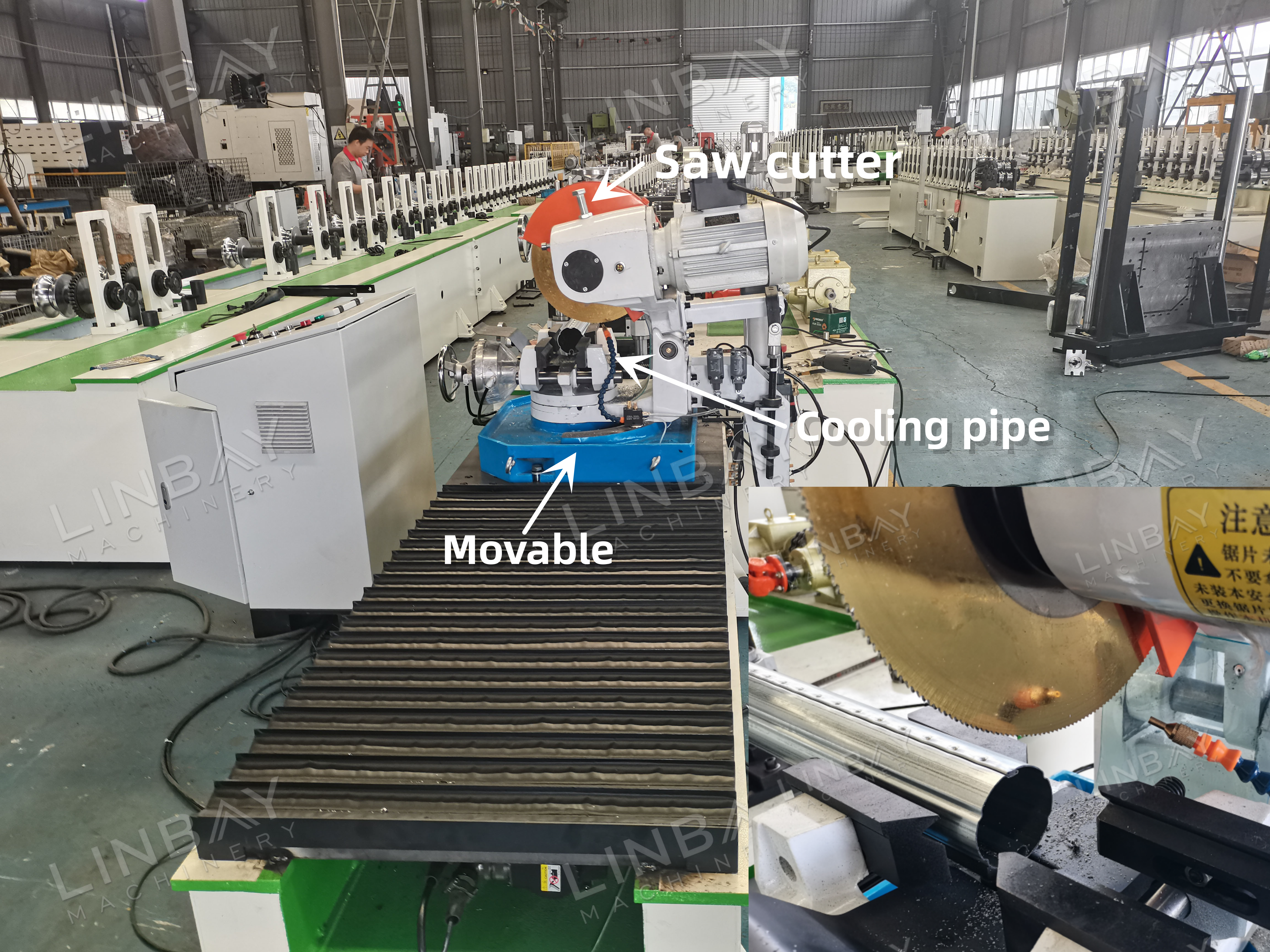
· Multi-Diameter Saw: Designed to accommodate various round tube sizes, helping to minimize blade replacement costs.
· Precision Cutting: Ensures clean, deformation-free cuts with smooth, burr-free edges.
· Material Efficiency: Eliminates waste with each cut, optimizing steel coil usage and reducing costs.
· Enhanced Production Speed: The cutter unit travels along a track at the same speed as the forming process, enabling uninterrupted operation.
· High Accuracy: Integrated with a servo motor and motion controller, maintaining cutting precision within a ±1mm tolerance.
· Efficient Cooling System: Recirculates coolant to keep the saw blade cool, ensuring consistent cutting quality during continuous use and prolonging the blade's life.
1. Decoiler
2. Feeding
3.Punching
4. Roll forming stands
5. Driving system
6. Cutting system
Others
Out table