Profile
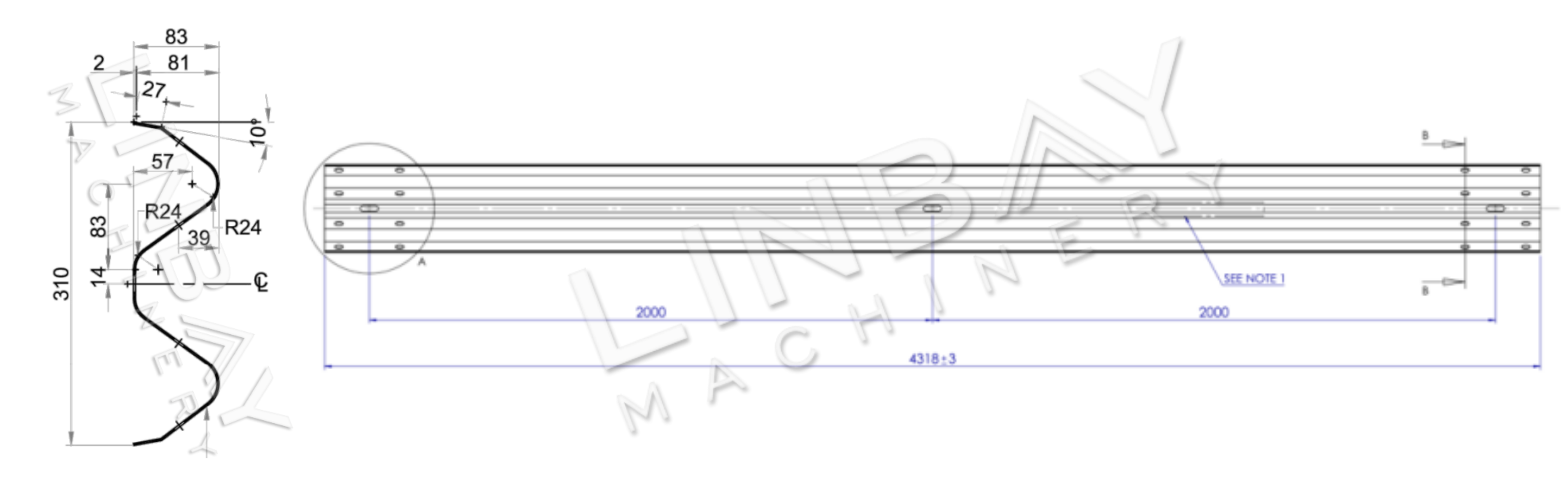
The W-beam guardrail is a frequently utilized safety barrier in various transportation engineering projects, including highways, expressways, and bridges. Its name derives from its "W" shape, characterized by its twin peaks. This guardrail is generally manufactured from galvanized or hot-rolled steel with a thickness of 2-4mm.
Each W-beam section usually measures 4 meters in length and comes with pre-punched holes at both ends to facilitate installation. Based on customer needs regarding production speed and available floor space, we offer customizable hole-punching solutions that can be seamlessly incorporated into the main roll forming machine production line.
Real case-Main Technical Parameters
Flow chart: Hydraulic decoiler-Guiding-Leveler-Hydraulic punch-Roll former-Hydralic cut-Out table

1.Line speed: 0-8m/min, adjustable
2.Suitable material:Hot rolled steel, cold rolled steel
3.Material thickness: 2-4mm
4.Roll forming machine: Cast-iron structure and universal joint
5.Driving system: Gearbox driving system with universal joint cardan shaft.
6.Cutting system: Cut before roll forming, roll former doesn’t stop when cutting.
Machinery
1.Hydraulic decoiler*1
2.Leveler(Equipped on the roll forming machine)*1
3.Hydraulic punch machine*1
4.Roll forming machine*1
5.Hydraulic cutting machine*1
6.Out table*2
7.PLC control cabinet*1
8.Hydraulic station*2
9.Spare parts box(Free)*1
Container size: 2x40GP
Real case-Description
Hydraulic Decoiler
The decoiler comes with two key safety features: a press arm and an outward coil retainer. When replacing coils, the press arm holds the coil in place to prevent it from springing up and causing injury to workers. The outward coil retainer ensures that the coil does not slip and fall during the unwinding process.
The decoiler is equipped with a standard four-piece core expansion mechanism that can adjust to fit varying coil inner diameters, ranging from 460mm to 520mm.
Leveler & Press Head
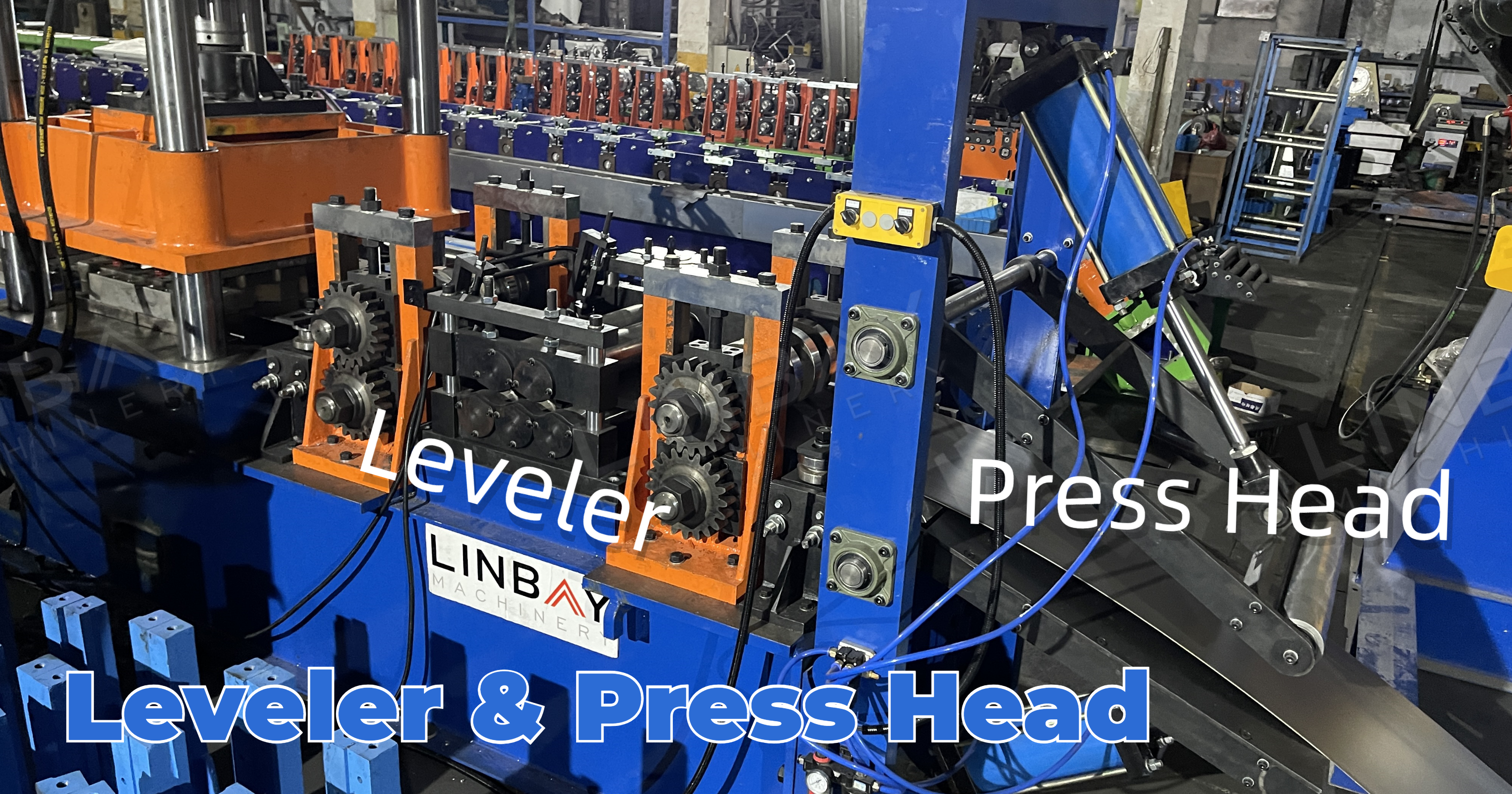
A platform positioned in front of the leveler, adjustable vertically via a hydraulic bar, aids in guiding the coil into the production line.
For profiles exceeding 1.5mm in thickness that require punching, it is crucial to use a leveler to flatten the coil and relieve internal stress to achieve uniform thickness, which enhances punching and forming quality. In this scenario, the leveler is incorporated into the main roll forming machine, sharing the same base.
To meet higher production speed demands, we provide a standalone leveler that marginally enhances the leveling speed, though it extends the total length of the production line by about 3 meters.
Hydraulic punch
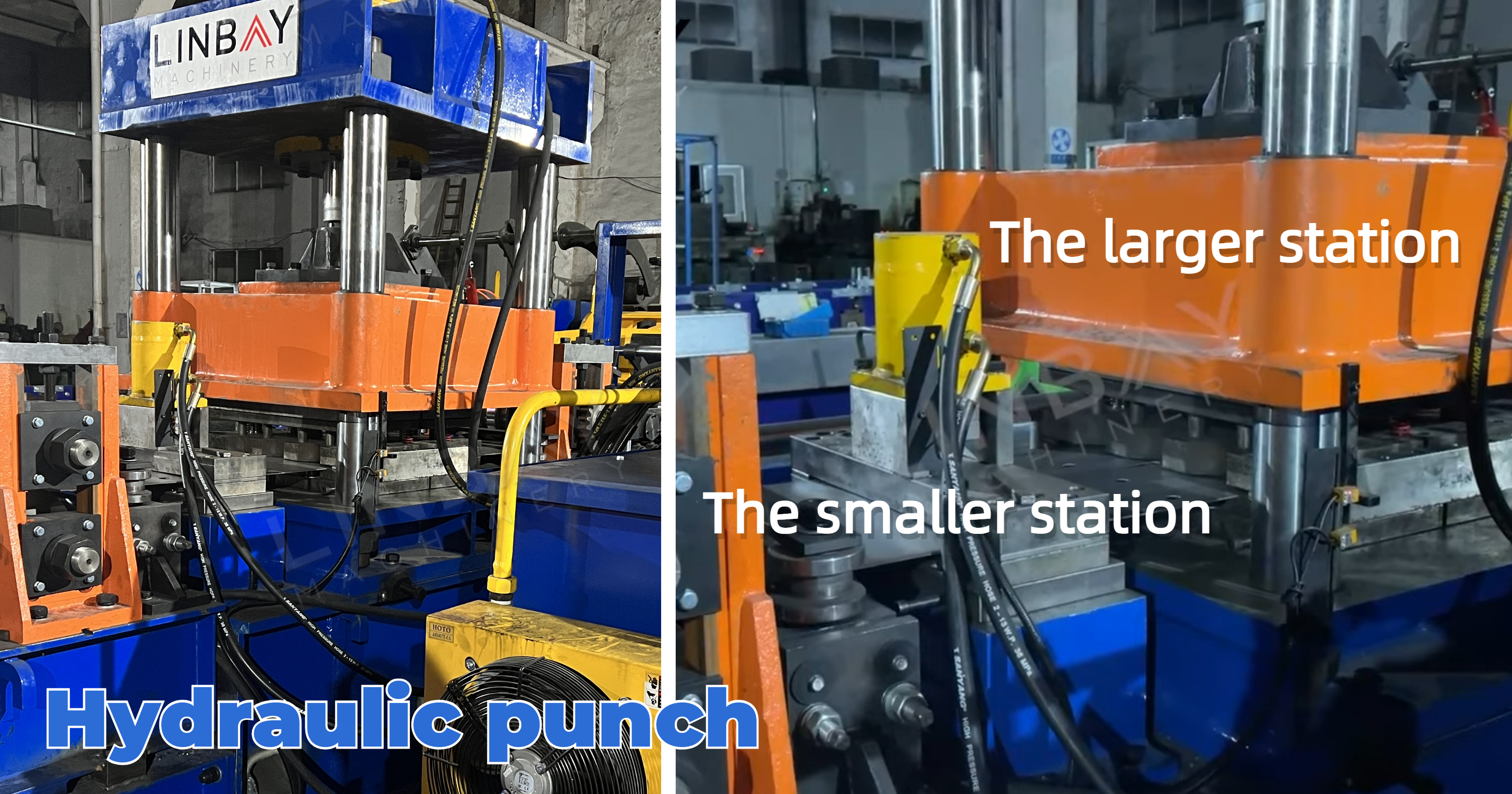
For efficiency and cost-effectiveness, punching operations can be split between two dies (two stations). The larger station can punch up to 16 holes simultaneously, while the second station handles holes that occur only once per beam.
Roll forming machine
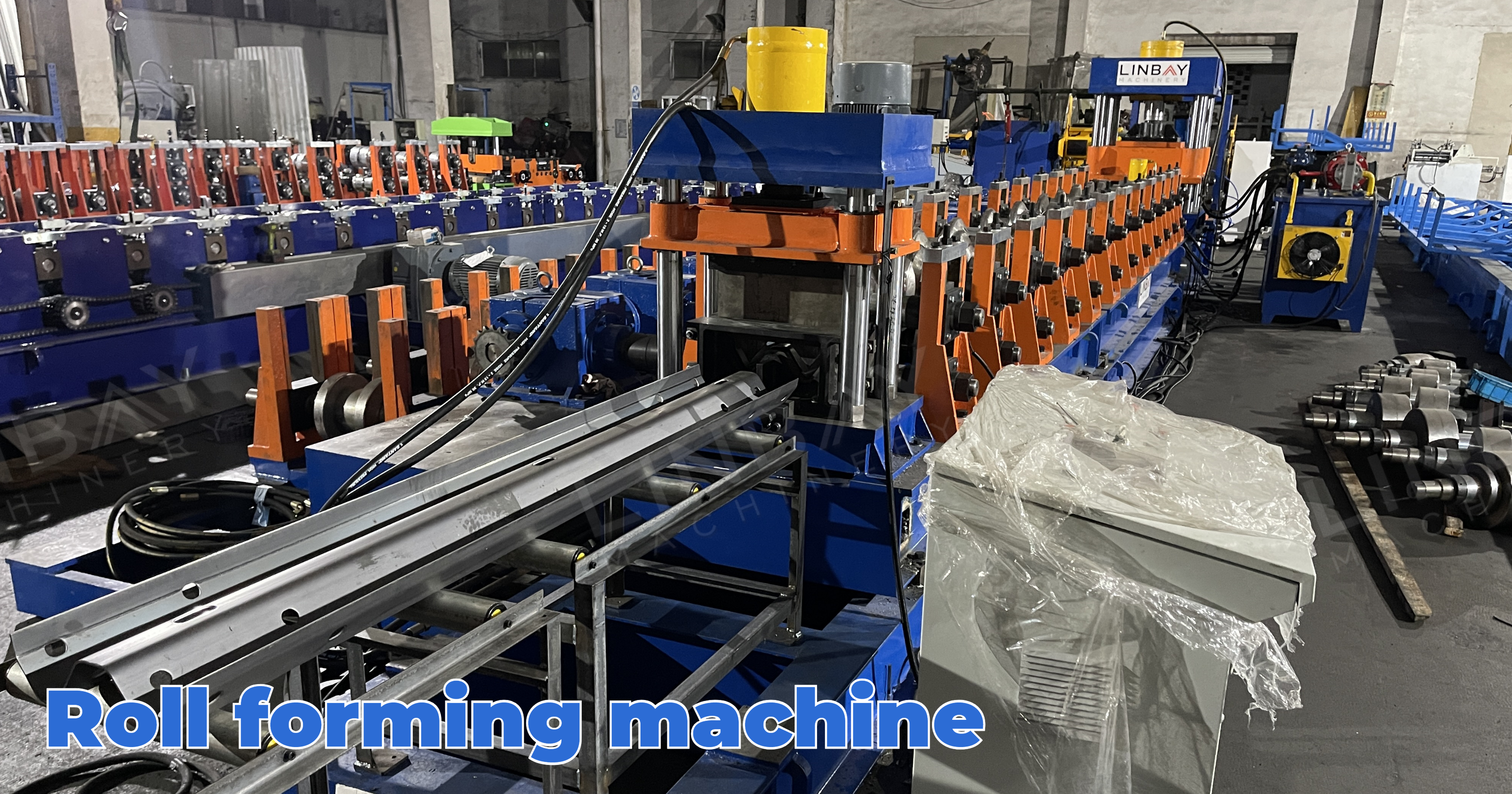
This roll former is constructed with a cast-iron frame, utilizing universal shafts to connect the forming rollers and gearbox. This design ensures durability and effectively meets the demands of forming guardrail panels with thicknesses ranging from 2 to 4mm. The steel coil progresses through a series of 12 forming stations to achieve the precise shape outlined in the drawings.
Hydraulic cutting machine
Since cutting takes place after forming, the cutting die must match the shape of the W-beam to minimize burrs and edge deformation. Designed for the stop-and-cut operation of the cutting machine, the forming process briefly pauses during cutting.
Pre-cut solution VS Post-cut solution
Production Speed: Normally, guardrail beams are 4 meters in length. Pre-cutting operates at a speed of 12 meters per minute, resulting in a production rate of 180 beams per hour. Post-cutting runs at 6 meters per minute, yielding 90 beams per hour.
Cutting Wastage: During cutting, the pre-cut method produces zero waste or loss. In contrast, the post-cut method generates waste of 18-20mm per cut, as specified in the design.
Line layout length: In the pre-cut method, a transfer platform is necessary after cutting, potentially resulting in a slightly longer production line layout compared to the post-cut method.
Impact on roll life: The post-cut method offers better roller life when processing heavy gauge and high-strength steel, as the leading edge in the pre-cut method impacts the forming rollers with each part.
Minimum Length:
In the pre-cut method, there is a requirement for a minimum cutting length to ensure that at least three sets of forming rollers are engaged with the steel coil. This ensures sufficient friction to drive the coil forward. However, in the post-cut method, there is no restriction on the minimum cutting length since the roll forming machine is always filled with steel coil. Given that the W-beam length is typically around 4 meters, exceeding the minimum length requirement, there is no concern regarding the choice between pre-cut and post-cut methods for this roll forming machine.
Kind Advice:
We recommend that our clients choose a suitable production line based on their production quantity requirements. For suppliers of guardrail beam profiles, the pre-cut method is advisable. Although the pre-cut method has a slightly higher cost compared to the post-cut method, its advantages in output can quickly offset this price disadvantage.
If you are procuring for a traffic construction project, the post-cut method is more suitable. It requires less space and comes at a slightly lower cost.
1. Decoiler
2. Feeding
3.Punching
4. Roll forming stands
5. Driving system
6. Cutting system
Others
Out table