Profile
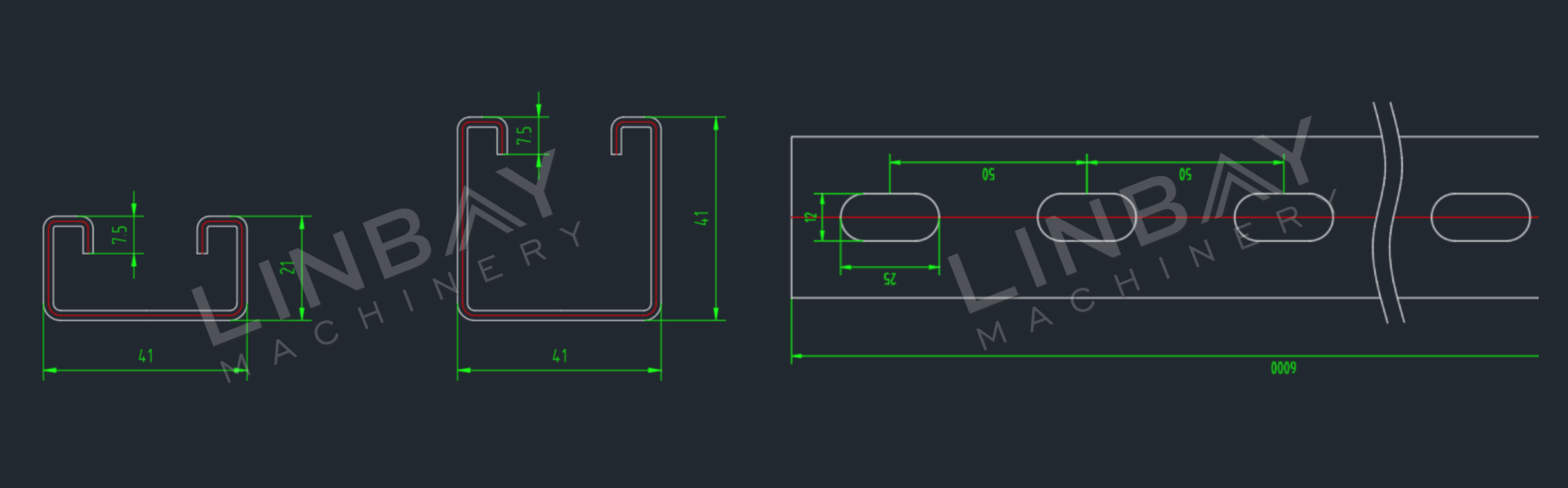
Strut channels are typically made of galvanized steel with thicknesses of 1.5-2.0mm or 2.0-2.5mm, or stainless steel with thicknesses of 1.5-2.0mm. They are designed with regularly spaced holes or slots along their length, facilitating the easy attachment of bolts, nuts, or other fasteners.
A production line with automatic size adjustment is ideal for manufacturing multiple sizes, such as common dimensions like 41*41, 41*21, 41*52, 41*62, 41*72, and 41*82mm. The higher the height of the strut channel, the more forming stations are required, which in turn increases the price of the roll forming machine.
Real case-Main Technical Parameters
Flow chart

Hydraulic decoiler with leveler--Servo feeder--Punch press--Guiding--Roll forming machine--Flying hydraulic cut--Out table
Main Techinical Parameters
1.Line speed: 15m/min, adjustable
2.Dimension: 41*41mm and 41*21mm.
3.Material thickness: 1.5-2.5mm
4.Suitable material: galvanized steel
5.Roll forming machine: Cast-iron structure and gearbox driving system.
6.Cutting and bending system: Flying hydraulic cut. Roll former doesn’t stop when cutting.
7.Changing size: Automatically.
8.PLC cabinet: Siemens system.
Real case-Description
Hydraulic decoiler with leveler
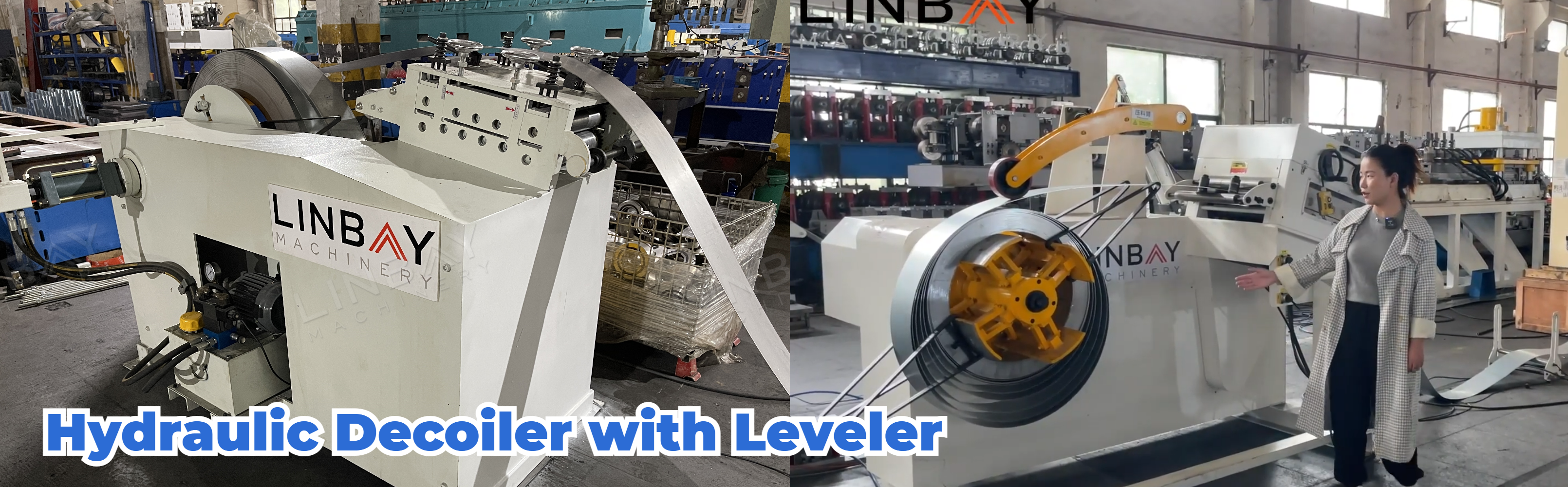
This type of decoiler, also known as a "2-in-1 decoiler and leveler," features a compact design that can save up to approximately 3 meters of production line space, thereby reducing factory land costs for our clients. Additionally, the shorter distance between the decoiler and leveler minimizes setup difficulties, making coil feeding and operation more convenient.
Servo Feeder & Punch Press
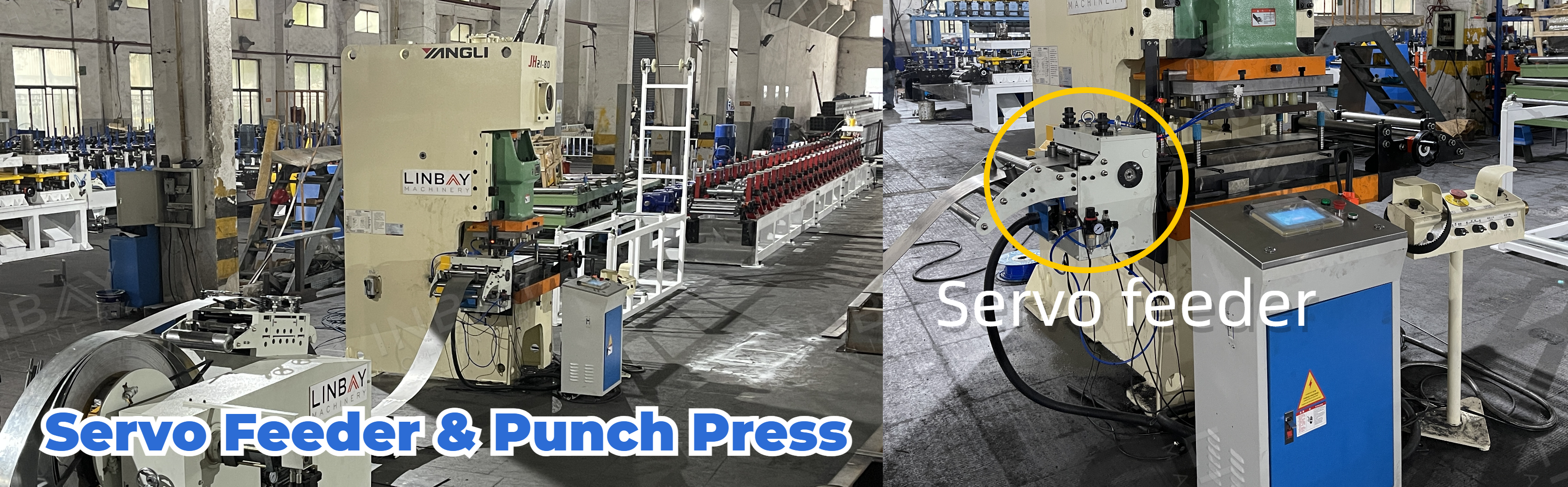
The servo motor operates with virtually no start-stop time delay, enabling precise control of the coil's feed length for accurate punching. Internally, pneumatic feeding within the feeder effectively protects the coil surface from abrasion.
Typically, the hole spacing of the strut channel is 50mm, with a punching pitch of 300mm. Compared to hydraulic punch machines with equivalent punching force, the punch press achieves a faster punching rate of approximately 70 times per minute.
While the initial investment costs for punch presses might be higher than for hydraulic punches, they offer better long-term cost-effectiveness, especially for high-volume production. Additionally, maintenance costs for punch presses may be lower due to their simpler mechanical components.
We have selected the Yangli brand punch press from China as our primary and long-term choice because Yangli has multiple offices worldwide, offering timely after-sales support and service to our clients.
Guiding
Guiding rollers ensure that the coil and the machine are aligned along the same centerline, guaranteeing that the coil remains undistorted throughout the forming process.
Roll forming machine
This forming machine employs a cast-iron structure and a gearbox driving system. The steel coil passes through a total of 28 forming stations, undergoing deformation until it matches the specifications in the drawings.
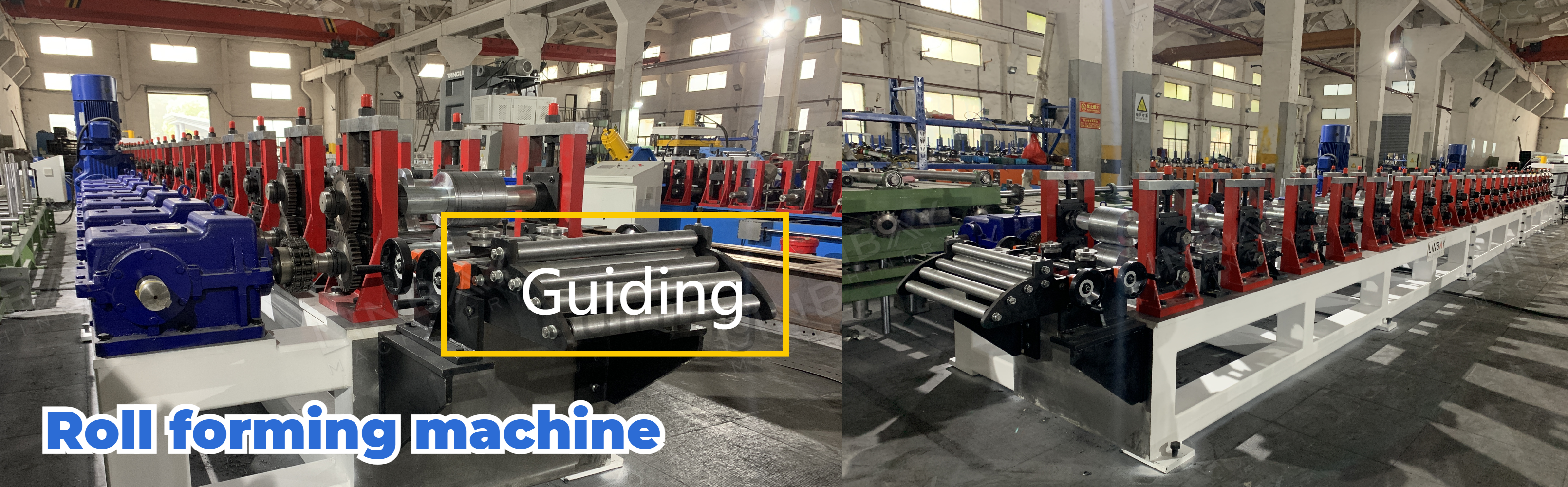
Once workers set the dimensions on the PLC control panel, the forming stations of the roll forming machine will automatically adjust to the correct positions, with the forming point moving in tandem with the rollers.
For safety during the movement of forming stations, two distance sensors are positioned on both the left and right sides. These sensors correspond to the outermost and innermost positions to which the forming stations can be adjusted. They detect the base of the forming stations: the innermost sensor prevents the forming stations from approaching too closely and causing roller collisions, while the outermost sensor prevents the forming stations from disengaging from the rails and falling.
The surface of the forming rollers is chrome-plated to protect it and extend the lifespan of the rollers.
Flying hydraulic cut
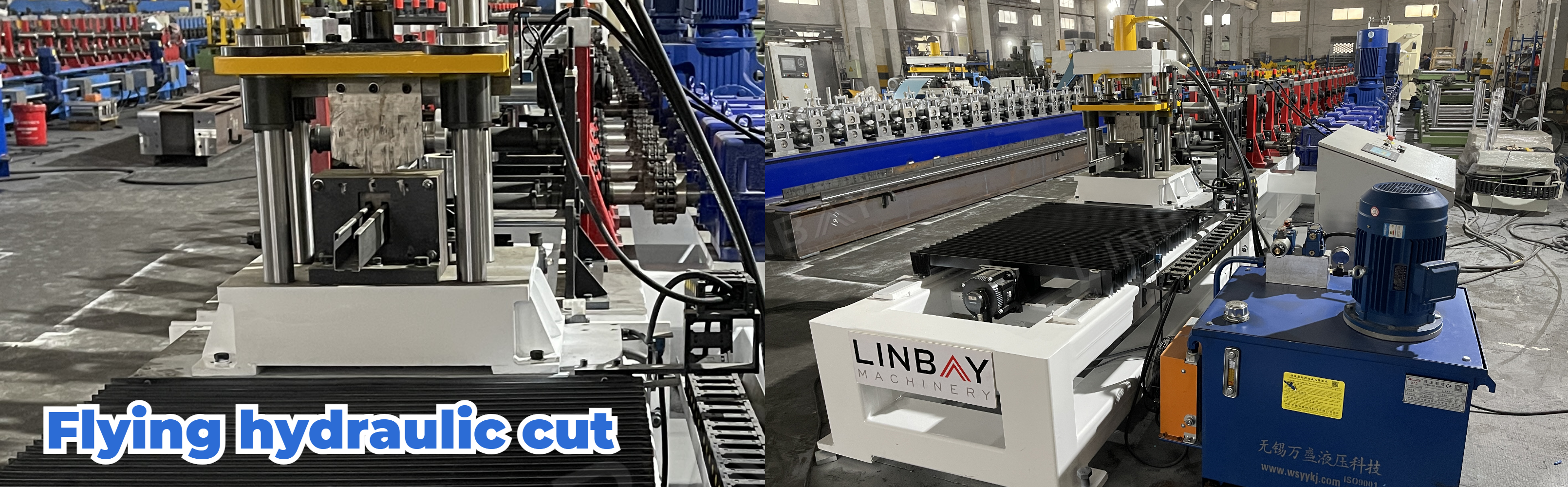
The base of the cutting machine can move back and forth on the track, enabling the steel coil to advance continuously through the roll forming machine. This setup eliminates the need to stop the roll forming machine, thereby increasing the overall speed of the production line.The cutting blade molds are tailored to match the shape of each specific profile. Therefore, each size requires its own set of cutting blade molds.
1. Decoiler
2. Feeding
3.Punching
4. Roll forming stands
5. Driving system
6. Cutting system
Others
Out table