VIDEO
Perfil
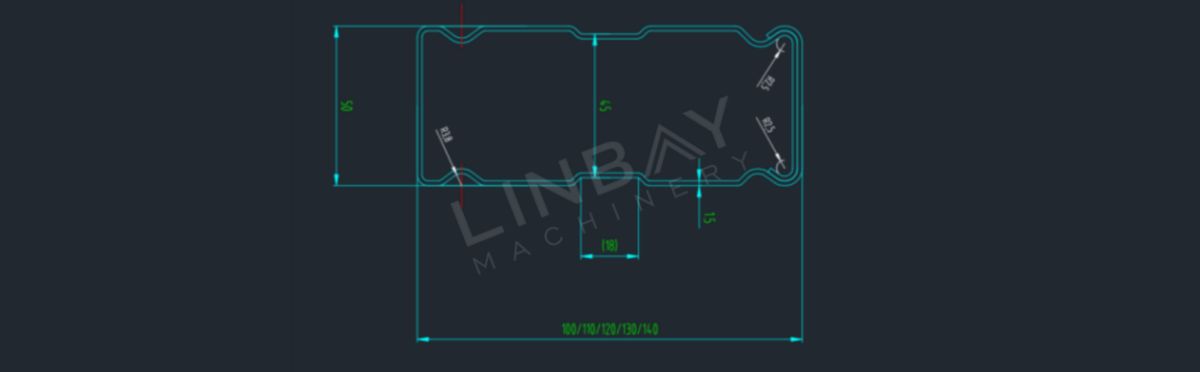
The one-piece beam is a key component in heavy-duty rack systems, featuring a rectangular box-like cross-section. It's assembled using connecting plates and screws, creating a sturdy framework with rack uprights. This design ensures shelf stability and robustness, capable of supporting substantial loads.
In manufacturing, a single steel coil is used to create the one-piece box beam. Cold rolled steel, hot rolled steel, or galvanized steel with a thickness of 1.5-2mm is commonly employed for production.
Real case-Main Techinical Parameters
The manual decoiler is designed with a brake device to adjust expansion and ensure smooth uncoiling within a range of φ460-520 mm. A press arm is included to prevent steel coil bulk, while steel protection leaves prevent coil slippage, enhancing both cost-effectiveness and safety.
In this instance, a manual decoiler without its own power source is used. For increased production capacity, we offer an optional hydraulic decoiler powered by a hydraulic station.
Guiding
Guiding rollers are essential for maintaining alignment between the steel coil and the machine, preventing tube beam distortion. They also help prevent rebound deformation of the steel coil during the forming process. The straightness of the tube box beam significantly influences product quality and the racking system's load-bearing capacity. Guiding rollers are strategically positioned along the entire forming line to ensure precise alignment. Measurements of each guiding roller's distance to the edge are meticulously documented in the manual, simplifying adjustments based on this data, even if minor displacements occur during transportation or production.
Leveler
Afterward, the steel coil progresses to the leveler, where its curvature is effectively removed to improve flatness and parallelism, ensuring high-quality final products. The leveler features 3 upper and 4 lower leveling rollers to accomplish this task efficiently.
Flow chart

Manual decoiler--Guiding--Leveler--Roll forming machine--Flying saw cut--Out table
Main Techinical Parameters
1.Line speed: 5-6meters/min dependeson the cutting length
2.Profiles: Multiple sizes-same height of 50mm, and different width of 100, 110, 120, 130, 140mm
3.Material thickness:1.9mm (in this case)
4.Suitable material:Hot rolled steel, cold rolled steel, galvanized steel
5.Roll forming machine: Cast-iron structure and chain driving system.
6.No. Of forming station: 28
7.Cutting system: Saw cutting, roll former doesn’t stop when cutting.
8.Changing size: Automatically.
9.PLC cabinet: Siemens system.
Real case-Description
Manual Decoiler
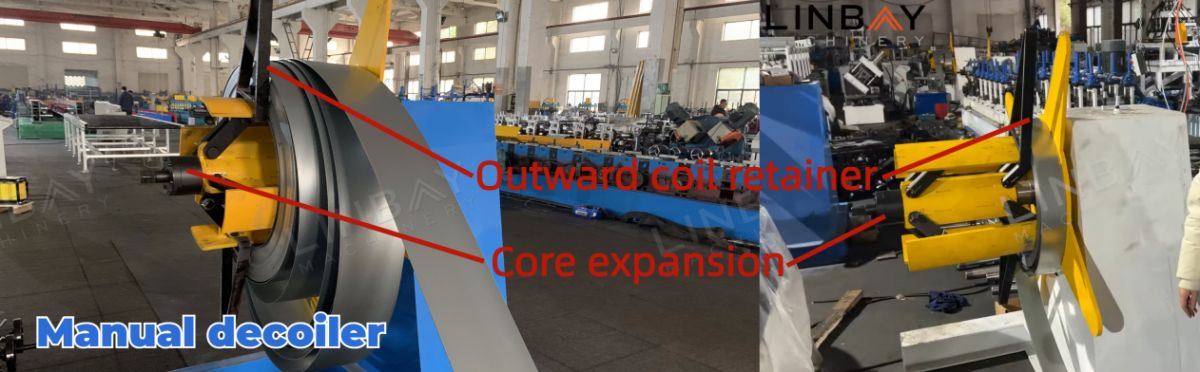
Roll Forming Machine
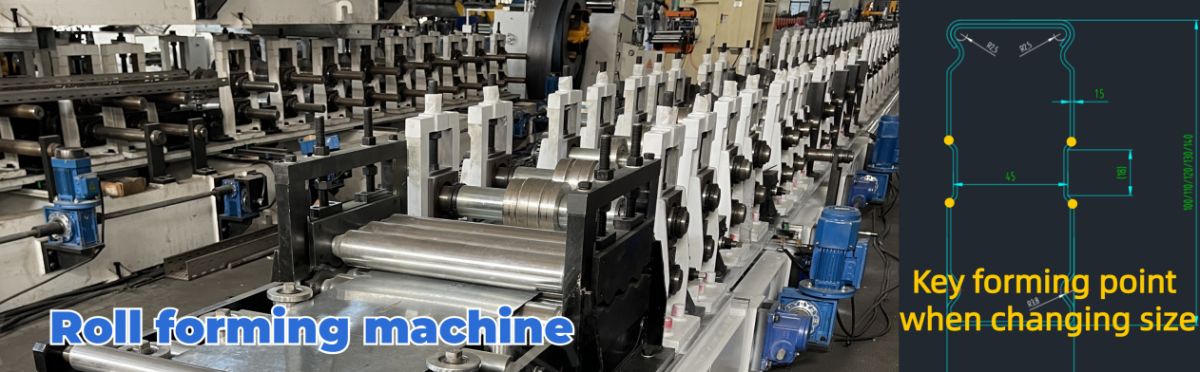
The roll forming machine stands as the cornerstone of the production line, boasting 28 sets of forming stations and a solid cast-iron structure. Driven by a robust chain system, it efficiently produces box beams of various sizes with uniform height and widths ranging from 100 to 140mm. Operators can effortlessly input desired sizes via the PLC control screen, triggering automatic adjustments of forming stations for precise positioning. This automated process, including size changes, takes approximately 10 minutes, facilitated by the movement of forming stations along the rail, adjusting 4 key forming points for different widths.
Forming rollers are crafted from Gcr15, a high-carbon chromium-bearing steel prized for its hardness and wear resistance. These rollers are chrome-plated for prolonged durability, while the shafts, made of 40Cr material, undergo meticulous heat treatment for added strength.
Flying Saw Cut
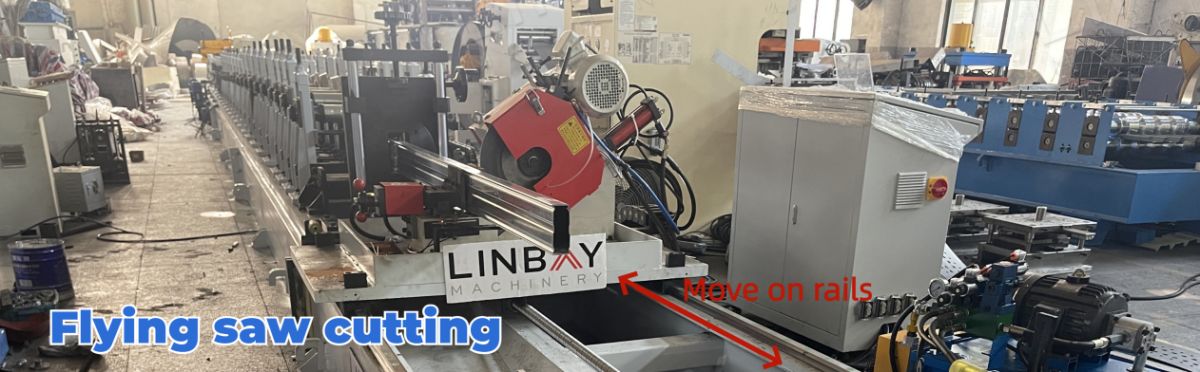
The closed shape of the box beam requires precise saw cutting to maintain structural integrity and prevent deformation of the cut edges. This method minimizes steel coil waste, ensuring smooth cutting surfaces without burrs. High-quality saw blades guarantee accuracy and hardness, while a cooling system prolongs their lifespan for continuous operation.
Although saw cutting speed is slightly slower than hydraulic shearing, our mobile function ensures synchronization with the forming machine's production speed, enabling uninterrupted operation and efficient workflow.
Encoder & PLC
The roll forming machine integrates a Japanese Koyo encoder to accurately translate coil lengths into electrical signals for the PLC control cabinet. A motion controller within ensures seamless movement of the shearing machine, maintaining precise cutting lengths without acceleration or deceleration. This results in consistently smooth and stable welding marks, preventing profile cracking and ensuring premium-grade step beam production.
Operators have full control over production parameters via the PLC control cabinet screen, including production speed, profile dimensions, cutting length, and quantity. With memory storage for commonly used parameters, operators can streamline production without repetitive parameter entry. Additionally, the PLC screen language can be customized to suit individual preferences.
Hydraulic Station
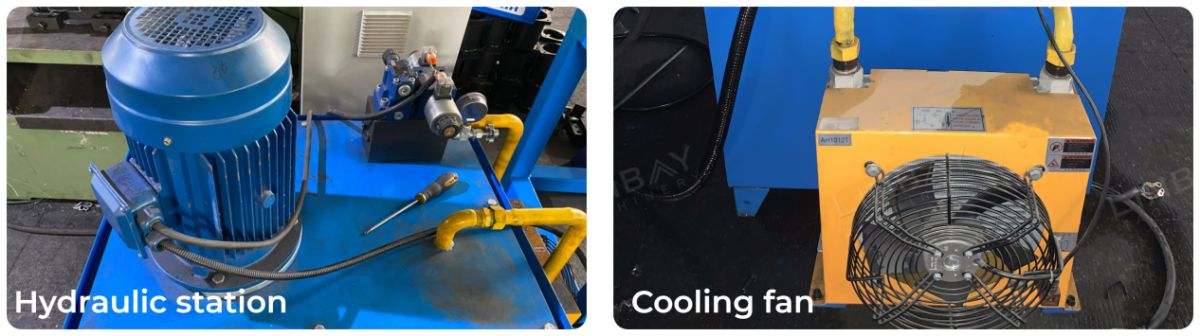
Our hydraulic station, equipped with cooling electric fans, efficiently dissipates heat, ensuring prolonged and reliable operation with a low failure rate.
Warranty
On the day of shipment, the current date will be engraved on the metal nameplate, marking the commencement of a two-year guarantee for the entire production line and a five-year warranty for rollers and shafts.
1. Decoiler
2. Feeding
3.Punching
4. Roll forming stands
5. Driving system
6. Cutting system
Others
Out table