پروفائل
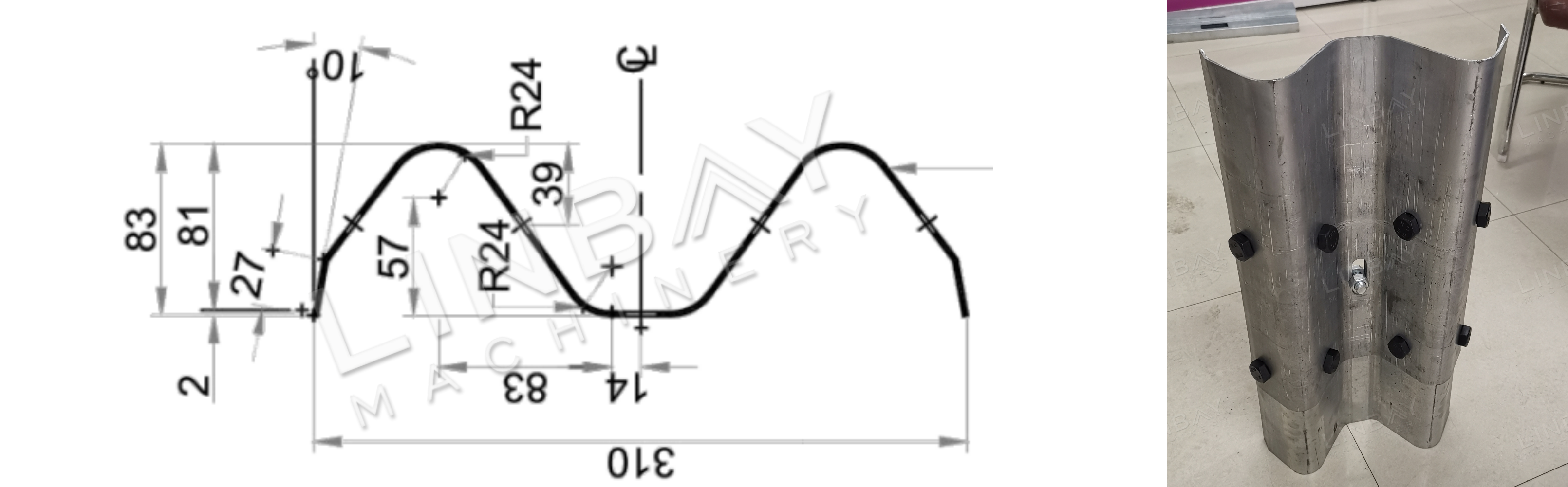
W-beam guardrail نقل و حمل کے بنیادی ڈھانچے کے منصوبوں جیسے ہائی ویز، ایکسپریس ویز، اور پلوں میں ایک اہم حفاظتی خصوصیت ہے۔ اس کا نام اس کی مخصوص "W" شکل سے آیا ہے، جس میں دوہری چوٹیاں ہیں۔ عام طور پر جستی یا گرم رولڈ اسٹیل سے تیار کیا جاتا ہے، W-beam guardrail کی موٹائی 2 سے 4mm تک ہوتی ہے۔
ایک معیاری ڈبلیو بیم سیکشن لمبائی میں 4 میٹر تک پھیلا ہوا ہے اور آسان تنصیب کے لیے دونوں سروں پر پہلے سے پنچڈ سوراخ رکھتا ہے۔ پیداوار کی رفتار اور فرش کی جگہ کے لیے صارفین کی مختلف ضروریات کو پورا کرنے کے لیے، ہم حسب ضرورت ہول پنچنگ حل فراہم کرتے ہیں جو بغیر کسی رکاوٹ کے بنیادی بنانے والی مشین پروڈکشن لائن میں ضم ہو جاتے ہیں۔
اصلی کیس-مین ٹیکنیکل پیرامیٹرز
فلو چارٹ: ہائیڈرولک ڈیکوائلر -- لیولر -- سروو فیڈر -- ہائیڈرولک پنچ -- پری کٹ -- پلیٹ فارم -- گائیڈنگ -- رول سابق -- آؤٹ ٹیبل
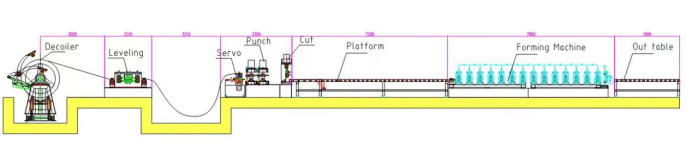
1. لائن کی رفتار: 0-12m/منٹ، ایڈجسٹ
2. مناسب مواد: گرم رولڈ اسٹیل، کولڈ رولڈ اسٹیل
3. مواد کی موٹائی: 2-4 ملی میٹر
4. رول بنانے والی مشین: کاسٹ آئرن ڈھانچہ اور یونیورسل جوائنٹ
5. ڈرائیونگ سسٹم: یونیورسل جوائنٹ کارڈن شافٹ کے ساتھ گیئر باکس ڈرائیونگ سسٹم۔
6. کٹنگ سسٹم: رول بننے سے پہلے کاٹیں، رول سابقہ کاٹتے وقت نہیں رکتا۔
7.PLC کابینہ: سیمنز سسٹم۔
مشینری
1. ڈیکوائلر*1
2. لیولر*1
3. سروو فیڈر*1
4. ہائیڈرولک پنچ مشین*1
5. ہائیڈرولک کاٹنے والی مشین*1
6۔پلیٹ فارم*1
7. رول بنانے والی مشین*1
8. آؤٹ ٹیبل*2
9.PLC کنٹرول کابینہ*2
10. ہائیڈرولک اسٹیشن*2
11. اسپیئر پارٹس باکس(مفت)*1
کنٹینر کا سائز: 2x40GP
اصلی کیس کی تفصیل
ہائیڈرولک ڈیکوائلر
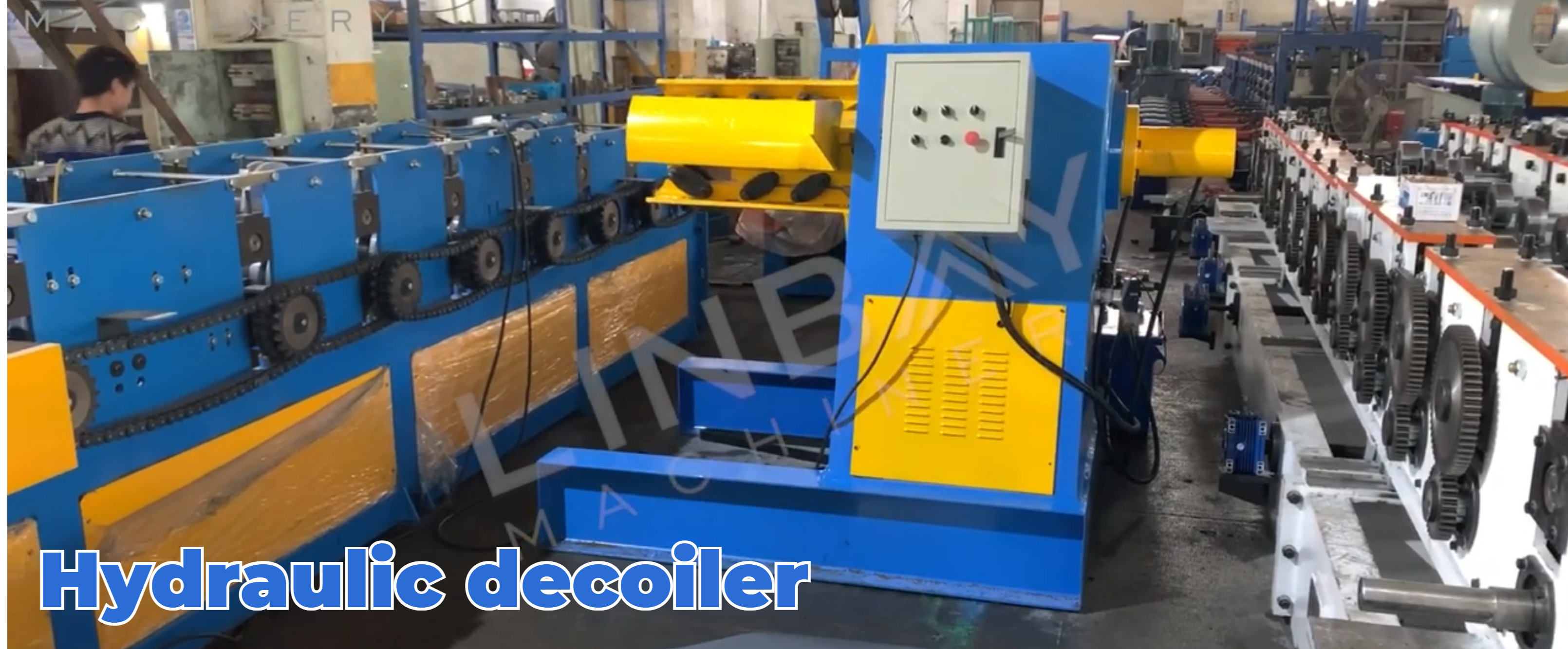
ہائیڈرولک ڈیکوائلر میں دو اہم حفاظتی اجزاء شامل ہیں: پریس بازو اور ظاہری کوائل ریٹینر۔ کنڈلی کو تبدیل کرتے وقت، پریس بازو کوائل کو محفوظ طریقے سے اپنی جگہ پر رکھتا ہے، اندرونی تناؤ کی وجہ سے اسے کھلنے سے روکتا ہے۔ اس کے ساتھ ہی، ظاہری کنڈلی کو برقرار رکھنے والا اس بات کو یقینی بناتا ہے کہ کنڈلی کو کھولنے کے عمل کے دوران مستحکم رہے۔
ڈیکوائلر کا بنیادی توسیعی آلہ سایڈست ہے، 460 ملی میٹر سے 520 ملی میٹر تک کے کوائل کے اندرونی قطر کو ایڈجسٹ کرنے کے لیے کنٹریکٹ یا توسیع کرنے کے قابل ہے۔
لیولر
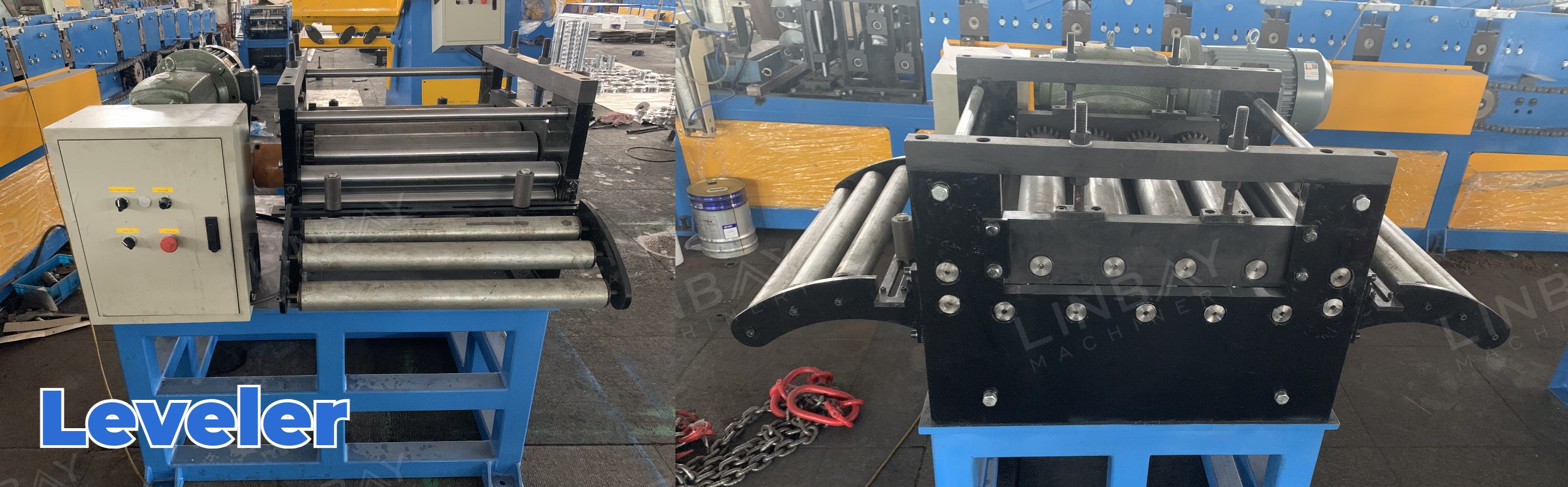
لیولر کنڈلی کو چپٹا کرنے اور مستقل موٹائی کو برقرار رکھنے کے لیے ضروری ہے۔ علیحدہ لیولر کا استعمال بہترین کارکردگی کو یقینی بناتا ہے۔
ہم جگہ اور اخراجات کو بچانے کے لیے ایک مشترکہ ڈیکوائلر اور لیولر (2-in-1 decoiler) بھی پیش کرتے ہیں۔ یہ مربوط حل الائنمنٹ، فیڈنگ، انسٹالیشن، اور ڈیبگنگ کو آسان بناتا ہے۔
سروو فیڈر
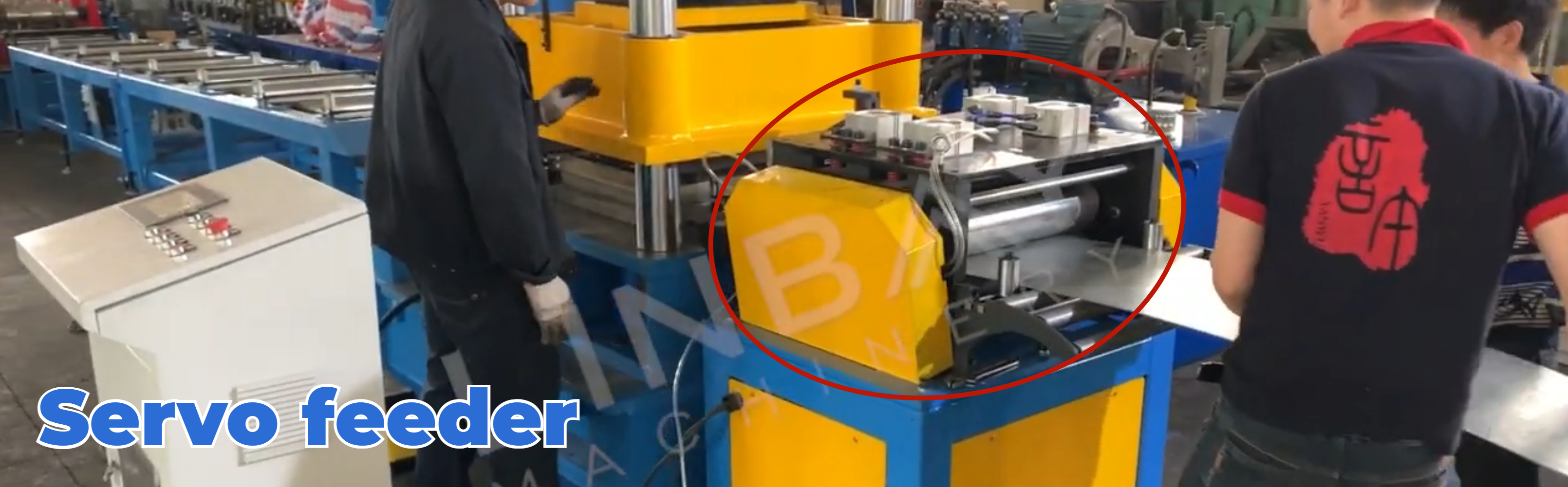
ایک سروو موٹر سے لیس، فیڈر عملی طور پر بغیر کسی سٹارٹ اسٹاپ تاخیر کے کام کرتا ہے، جس سے درست چھدرن کے لیے کوائل فیڈ کی لمبائی کا درست کنٹرول ہوتا ہے۔ اندرونی طور پر، نیومیٹک فیڈنگ کنڈلی کی سطح کو کھرچنے سے بچاتی ہے۔
ہائیڈرولک پنچ اور پری کٹ ہائیڈرولک کٹنگ مشین
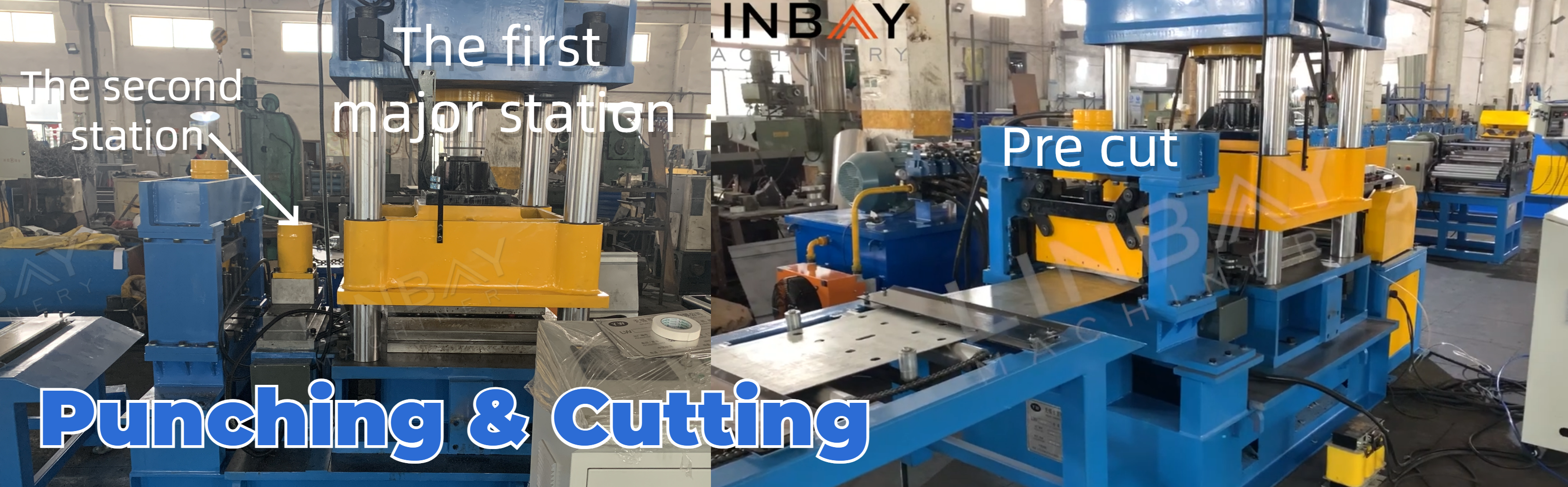
کارکردگی اور لاگت کی تاثیر کو بڑھانے کے لیے، چھدرن کے عمل کو دو ہائیڈرولک اسٹیشنوں (دو سانچوں) کے ذریعے سنبھالا جاتا ہے۔
پہلا بڑا اسٹیشن ایک وقت میں 16 سوراخ کر سکتا ہے۔ دوسرے اسٹیشن پر چھیڑے گئے سوراخ ہر بیم پر صرف ایک بار ظاہر ہوتے ہیں، جس سے چھوٹے اسٹیشن کو زیادہ موثر حل بنایا جاتا ہے۔
رول بنانے سے پہلے پہلے سے کاٹنا رول بنانے والی مشین کے بلاتعطل آپریشن کو یقینی بناتا ہے، اس طرح پیداوار کی رفتار میں اضافہ ہوتا ہے۔ مزید برآں، یہ حل سٹیل کوائل کے ضیاع کو کم کرتا ہے۔
رہنمائی کرنا
رول بنانے والی مشین کے سامنے رکھے گائیڈنگ رولرس سٹیل کوائل اور مشین کے درمیان سیدھ کو یقینی بناتے ہیں، تشکیل کے عمل کے دوران کنڈلی کو مسخ ہونے سے روکتے ہیں۔
رول بنانے والی مشین
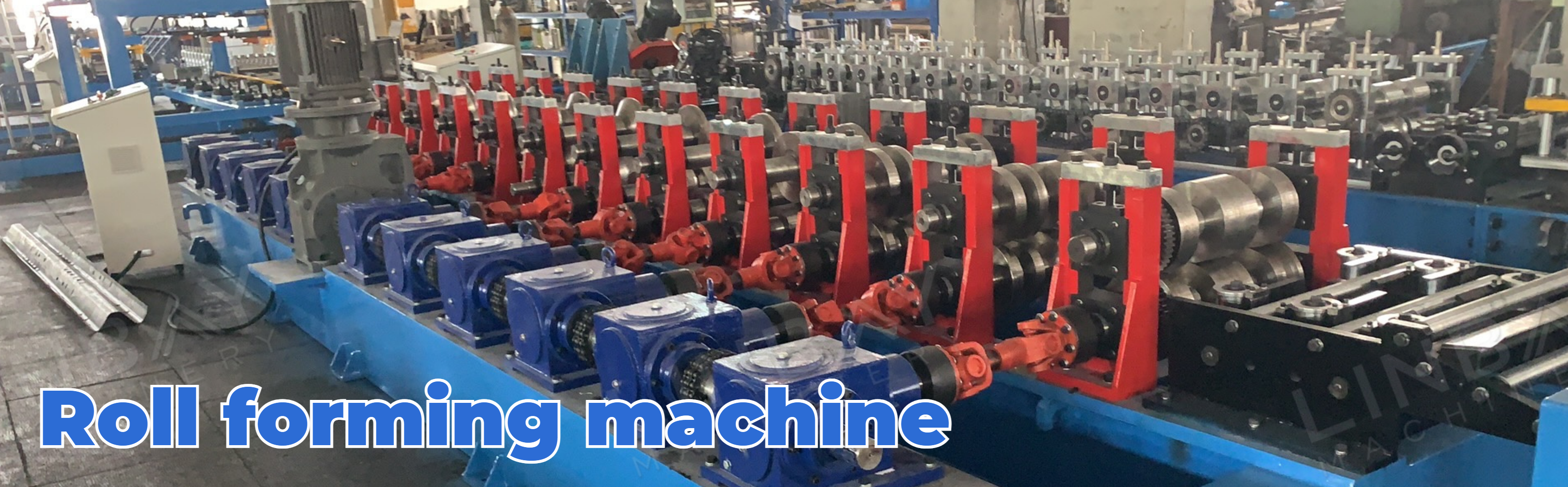
یہ رول بنانے والی مشین میں کاسٹ آئرن کا ڈھانچہ ہے، جس میں یونیورسل شافٹ رولرس اور گیئر باکسز کو جوڑتے ہیں۔ اسٹیل کوائل کل 12 تشکیل دینے والے اسٹیشنوں سے گزرتی ہے، جب تک کہ یہ گاہک کی ڈرائنگ میں بیان کردہ W-beam کی شکل کے مطابق نہ ہو جائے تب تک خرابی سے گزرتا ہے۔
تشکیل دینے والے رولرس کی سطح کو ان کی حفاظت اور ان کی عمر بڑھانے کے لیے کروم چڑھایا جاتا ہے۔
اختیاری: آٹو اسٹیکر
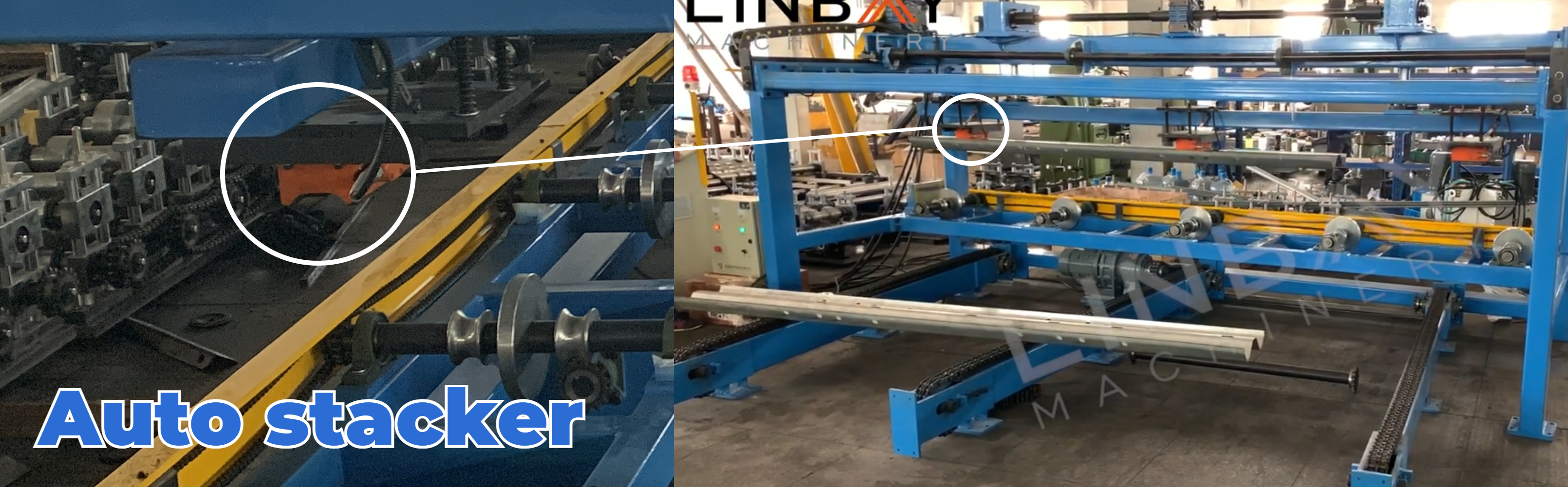
پروڈکشن لائن کے اختتام پر، آٹو اسٹیکر کا استعمال تقریباً دو کارکنوں کی دستی مزدوری کے اخراجات کو کم کر سکتا ہے۔ مزید برآں، 4 میٹر طویل ڈبلیو بیم کے وزن کی وجہ سے، دستی ہینڈلنگ سے حفاظتی خطرات لاحق ہوتے ہیں۔
ایک آٹو اسٹیکر ایک عام اور کارآمد آپشن ہے جو رول بنانے والی پروڈکشن لائنوں کی لمبائی پر مبنی قیمتوں کے ساتھ کارکردگی اور حفاظت دونوں کو بڑھاتا ہے۔ مختلف پروفائلز کو الگ الگ اسٹیکنگ طریقوں کی ضرورت ہوتی ہے۔ اس پروڈکشن لائن میں، ایک 4 میٹر لمبا آٹو اسٹیکر تین سکشن کپ سے لیس ہے جو ڈبلیو کے سائز کے پروفائلز کے لیے تیار کیے گئے ہیں۔ یہ سکشن کپ محفوظ طریقے سے ڈبلیو بیم کو پکڑتے ہیں اور اسے احتیاط سے کنویئر پر رکھ دیتے ہیں تاکہ نقل و حمل میں آسانی ہو۔
پری کٹ سلوشن VS پوسٹ کٹ سلوشن
پیداوار کی رفتار:عام طور پر، گارڈریل بیم 4 میٹر لمبے ہوتے ہیں۔ پری کٹنگ 12 میٹر فی منٹ کی رفتار سے کام کرتی ہے، جس سے 180 بیم فی گھنٹہ کی پیداوار ممکن ہوتی ہے۔ کاٹنے کے بعد، 6 میٹر فی منٹ کی رفتار سے چلنے سے، فی گھنٹہ 90 بیم حاصل ہوتی ہے۔
بربادی کاٹنا:کاٹنے کے دوران، پری کٹ محلول صفر فضلہ یا نقصان پیدا کرتا ہے۔ اس کے برعکس، پوسٹ کٹ سلوشن ڈیزائن کی وضاحتوں کے مطابق 18-20 ملی میٹر فی کٹ کا فضلہ پیدا کرتا ہے۔
لائن لے آؤٹ کی لمبائی:پری کٹ سلوشن میں، کاٹنے کے بعد ایک ٹرانسفر پلیٹ فارم ضروری ہوتا ہے، جو پوسٹ کٹ سلوشن کے مقابلے میں تھوڑا طویل پروڈکشن لائن لے آؤٹ کا باعث بن سکتا ہے۔
کم از کم لمبائی:پری کٹ سلوشن میں، اس بات کو یقینی بنانے کے لیے کم از کم کاٹنے کی لمبائی کی ضرورت ہوتی ہے کہ اسٹیل کوائل رولرز کے کم از کم تین سیٹوں پر پھیلا ہوا ہے، جو اسے آگے بڑھانے کے لیے کافی رگڑ فراہم کرتا ہے۔ اس کے برعکس، پوسٹ کٹ سلوشن میں کٹنگ کی لمبائی کی کم از کم پابندی نہیں ہے کیونکہ رول بنانے والی مشین کو مسلسل سٹیل کوائل سے کھلایا جاتا ہے۔
تاہم، یہ دیکھتے ہوئے کہ ڈبلیو بیم کی لمبائی عام طور پر 4 میٹر کے لگ بھگ ہوتی ہے، جو لمبائی کی کم از کم ضرورت سے زیادہ ہوتی ہے، اس رول بنانے والی مشین کے لیے پری کٹ اور پوسٹ کٹ سلوشنز کے درمیان انتخاب W بیم کے لیے ڈیزائن کیا گیا کم اہم ہو جاتا ہے۔
قسم کا مشورہ:ہم تجویز کرتے ہیں کہ کلائنٹ اپنی مخصوص پیداواری مقدار کی ضروریات کی بنیاد پر پروڈکشن لائن منتخب کریں۔ گارڈریل بیم پروفائلز کے سپلائرز کے لیے، پری کٹ سلوشن کی سفارش کی جاتی ہے۔ پوسٹ کٹ حل کے مقابلے اس کی قدرے زیادہ لاگت کے باوجود، اس کی بہتر پیداواری صلاحیتیں لاگت کے کسی بھی فرق کو تیزی سے پورا کر سکتی ہیں۔
اگر آپ ٹریفک کی تعمیر کے منصوبے کے لیے خریداری کر رہے ہیں، تو کٹ کے بعد کا حل زیادہ موزوں ہے۔ یہ کم جگہ لیتا ہے اور عام طور پر قدرے کم قیمت پر دستیاب ہوتا ہے۔
1. ڈیکوائلر
2. کھانا کھلانا
3. مکے مارنا
4. رول بنانے کے اسٹینڈز
5. ڈرائیونگ سسٹم
6. کاٹنے کا نظام
دوسرے
آؤٹ ٹیبل