VIDEO
Profil
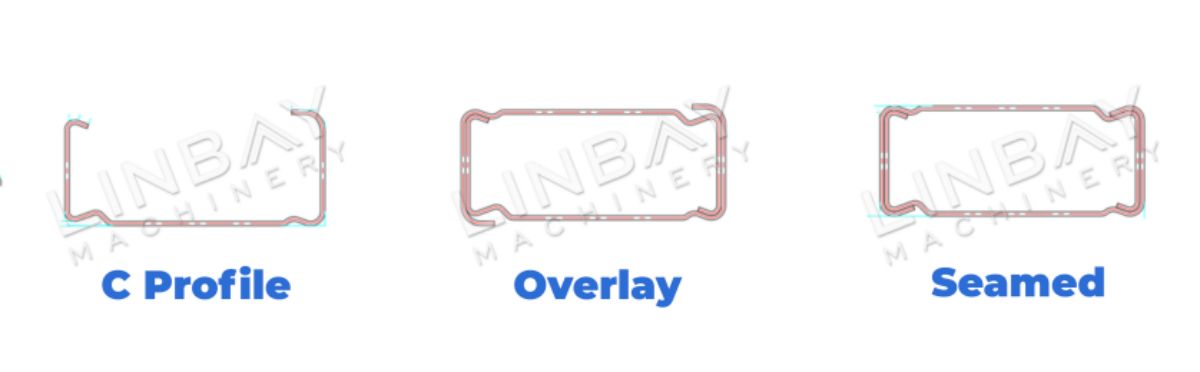
Der Kastenträger ist eine robuste Option, zugeschnitten aufSchwerlastAnwendungen. Konkret präsentieren wir einezweiteiliger Kastenträgerfür Ihre Überlegung. Typischerweise aus kaltgewalztem oder warmgewalztem Stahl mit einer Dicke von 1,5 bis 2 mm geschmiedet, wird es einer präzisenRollformenvor der Beschichtung, um ein Gleichgewicht zwischen optischer Attraktivität und dauerhafter Festigkeit zu gewährleisten. Die Montage beinhaltet das sichere Verbindenzwei Stücke geformter C-förmiger Stahlprofile, wodurch eine stabile Rohrstruktur entsteht. Für die Herstellung von Kastenträgern erweist sich die Kaltwalzformmaschine als die bevorzugte Wahl, da sie Effizienz und Präzision bietet.
Realer Fall - Wichtigste technische Parameter
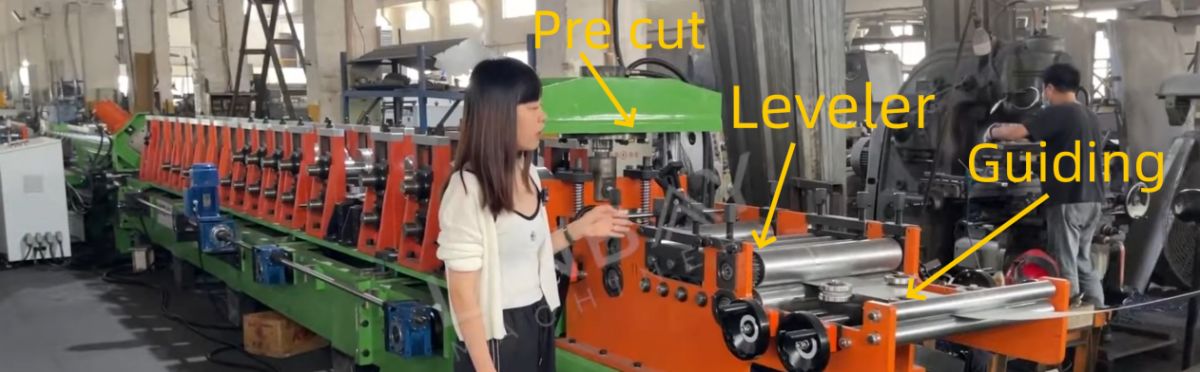
Führungsrollen sind entscheidend für die Ausrichtung zwischen der Stahlspule und der Maschine, effektivVermeidung von Verzerrungendes Kastenträgers. Sie spielen auch eine wichtige Rolle im Formungsprozess, indem sie eine Rückprallverformung der Stahlspule verhindern.Die Geradlinigkeitdes Kastenträgers hat erheblichen Einfluss aufProduktqualität und die Tragfähigkeitdes gesamten Regals. Strategisch entlang der Formlinie positionierte Führungsrollen gewährleisten eine genaue Ausrichtung.MessungenDer Abstand jeder Führungsrolle zur Kante ist im Handbuch genau dokumentiert, sodass selbst bei geringfügigen Verschiebungen während des Transports oder der Produktion eine reibungslose Anpassung auf Basis dieser Daten möglich ist.
Leveler
Nach der vorhergehenden Stufe gelangt die Stahlspule zum Richtprozess. Hier richtet die Richtmaschine sorgfältigeliminiert jegliche Krümmung in der Stahlspule, wodurch die Ebenheit und Parallelität verbessert und somit die Qualität des Endprodukts – des Kastenträgers – gesteigert wird. Ausgestattet mit zwei oberen und drei unteren Richtwalzen sorgt die Richtmaschine für höchste Präzision bei der Vorbereitung der Stahlspule für die nachfolgenden Fertigungsschritte.
Hydraulischer Vorschnitt
Diese Produktionslinie umfasstPoreneine hydraulische Vorschneideeinrichtung,Vereinfachung des Austauschs von Stahlcoils mit unterschiedlichen Breiten und Dicken, während gleichzeitigMinimierung des Coil-Abfalls.
Rollformmaschine
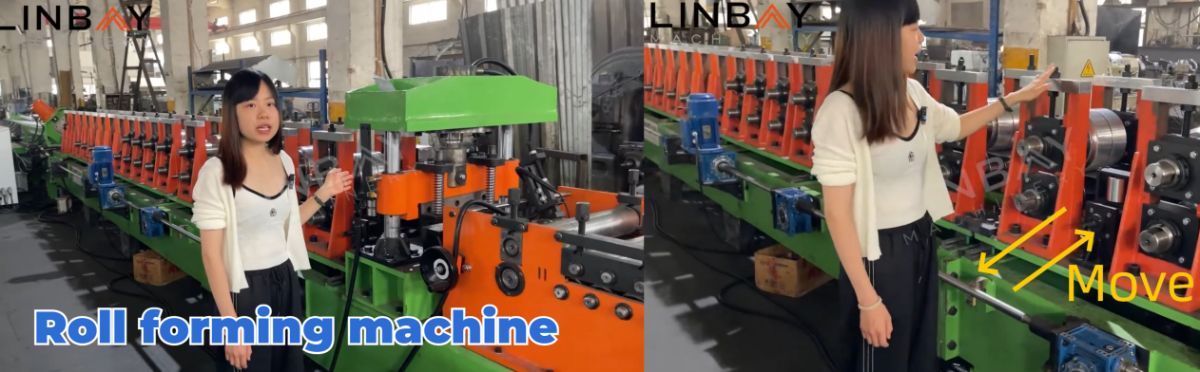
Flussdiagramm

Manuelle Abwickelhaspel - Führung - Richtmaschine - Hydraulischer Vorschnitt - Rollformmaschine - Fliegender hydraulischer Schnitt - Plattform - Falzmaschine - Auslauftisch
Wichtigste technische Parameter
1.Liniengeschwindigkeit: 0-4 m/min, einstellbar
2.Profile: Mehrere Größen – gleiche Höhe von 50 mm und unterschiedliche Breiten von 80, 100, 120 mm
3.Materialstärke: 1,5-2 mm
4. Geeignetes Material: Warmgewalzter Stahl, kaltgewalzter Stahl, verzinkter Stahl
5.Rollformmaschine: Gusseisen-Stru
Struktur und Kettenantriebssystem.
6.Anzahl der Formstationen: 18
7. Schneidsystem: Hydraulisches Schneiden, Rollformer stoppt beim Schneiden nicht.
8.Größenänderung: Automatisch.
9.SPS-Schrank: Siemens-System.

Realfall-Beschreibung
Manuelle Abwickelhaspel
Der manuelle Abwickelhaspel ist ausgestattet mit einemBremssystemSorgfältig konstruiert, um die Spannung der Abwickelrolle zu regulieren und einen reibungslosen Abwickelvorgang zu gewährleisten. Um das Risiko eines plötzlichen Rückstoßes, insbesondere bei Stahlrollen mit einer Dicke von mehr als 1,5 mm, zu verringern,ein Pressarmwird verwendet, um die Stahlspule sicher an ihrem Platz zu halten. Darüber hinaus sind Stahlschutzblätter strategisch angebracht, um ein Verrutschen der Spule beim Abwickeln zu verhindern. Dieses durchdachte Design erhöht nicht nur die Sicherheit, sondern bietet auchhohe Wirtschaftlichkeit, wodurch ein zuverlässiger und effizienter Betrieb gewährleistet wird.
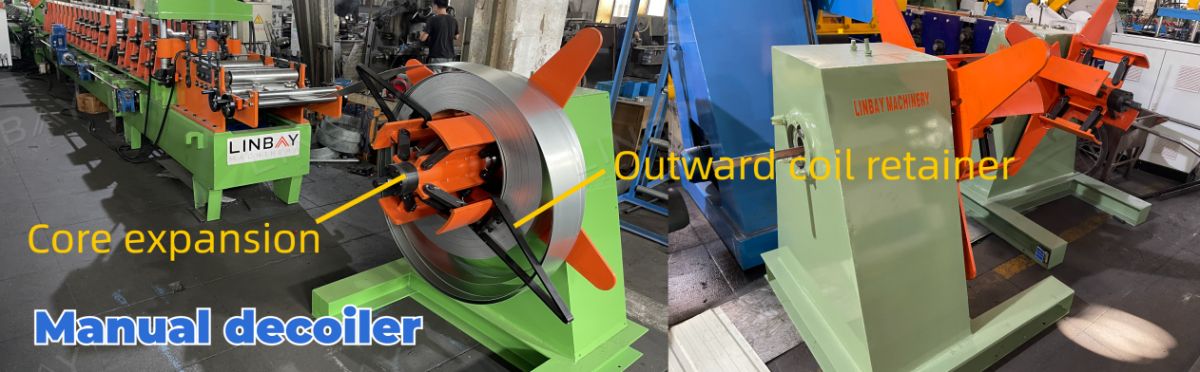
In diesem Szenario wird ein manueller Abwicklerohne eigene Stromquelleeingesetzt. Für höhere Anforderungen an die Produktionsgeschwindigkeit bieten wir optional einehydraulische Abwickelhaspelangetrieben durch eine Hydraulikstation.
Führung
Das Herzstück der gesamten Produktionslinie ist die Rollformmaschine, eine unverzichtbare Komponente. Sie besteht aus einem massiven StückGusseisenDiese Maschine zeichnet sich durch eine robuste Konstruktion aus und wird von einem zuverlässigenKettensystemSeine Vielseitigkeit ermöglicht die Produktion unterschiedlicher Größen mit gleichbleibender Höhe. Bediener geben die geplanten Abmessungen mühelos auf dem SPS-Steuerungsbildschirm ein und lösenautomatische Anpassungenvon Formstationen auf präzise Positionen. Üblicherweise benötigen erfahrene Arbeiter etwa 60 Minuten, um den gesamten Dimensionswechselprozess durchzuführen, der sowohl die automatische Bewegung der Formstationen als auch den manuellen Austausch der Stahlspule umfasst.
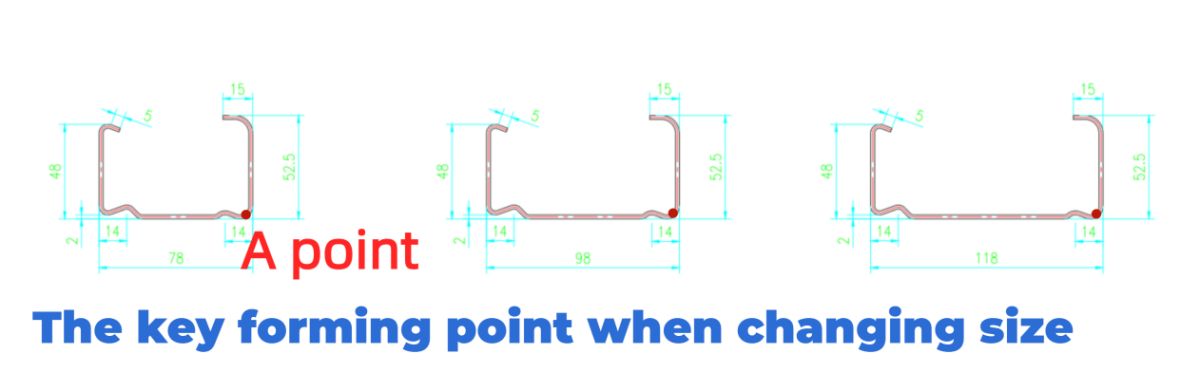
DerEin Punktfungiert als Drehpunkt für die Breitenanpassung. Während sich die Rollformstationen entlang der Schienen bewegen, verschieben sie die Position dieses kritischen Formpunkts dynamisch und ermöglichen so die Herstellung vonKasten Balken mit unterschiedlichen Breiten.
Als Material für die Formwalzen wurde Gcr15 gewählt – ein kohlenstoffreicher Chromstahl, der für seine außergewöhnliche Härte und Verschleißfestigkeit bekannt ist. Die Walzen werden verchromt, um ihre Langlebigkeit zu erhöhen, während die Wellen aus 40Cr-Material für zusätzliche Haltbarkeit wärmebehandelt werden.
Fliegender hydraulischer Schnitt

Nach dem Rollformprozess nimmt die Stahlspule allmählich ein C-förmiges Profil an. Anschließend wird sie von einer hydraulischen Schneidemaschine präzise auf die gewünschte Länge zugeschnitten, wobei einSchnittlängenfehler innerhalb von 1 mm. Dieser Schneidevorgang minimiert effizient den Stahlcoil-Verschwendung und ist mit der Produktionsgeschwindigkeit der Rollformmaschine synchronisiert, wodurch ein nahtloser und unterbrechungsfreier Betrieb gewährleistet wird.
Plattform
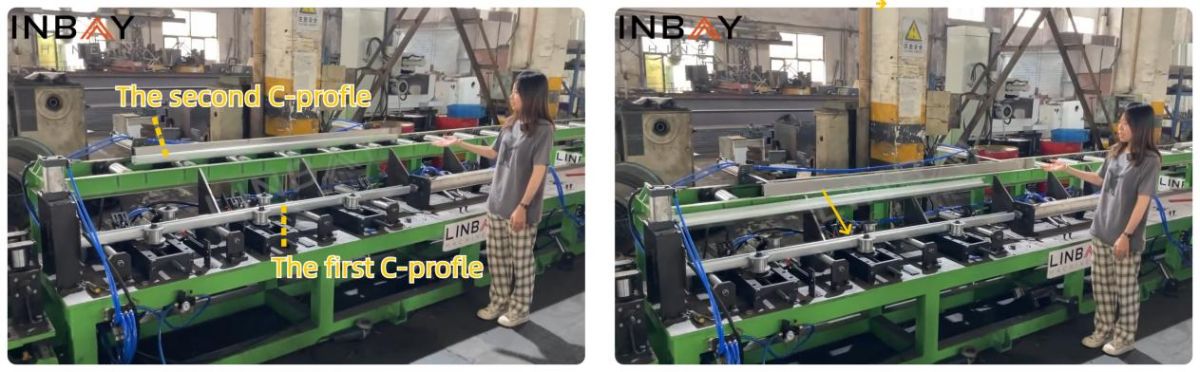
Das erste C-Profil wird zur oberen Plattform befördert und anschließend auf die untere Plattform geschoben. Anschließend wird das zweite C-Profil vorsichtig auf die mittlere Schräge geschoben und dort von einer Wendevorrichtung gedreht. Dadurch werden die beiden C-Profile vertikal ausgerichtet und sauber gestapelt.
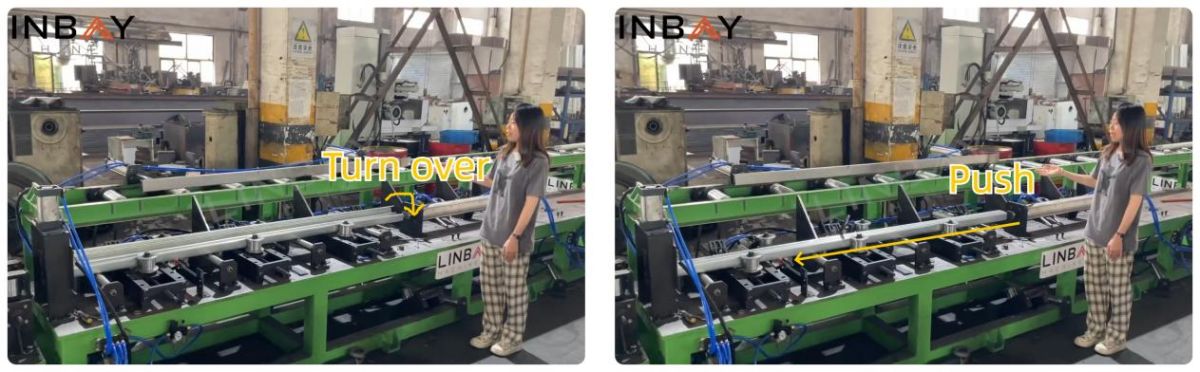
Führungsrollen sorgen für die Ausrichtung der beiden C-Profile und pneumatische Schubstangen schieben sie in die Falzmaschine.
Falzmaschine
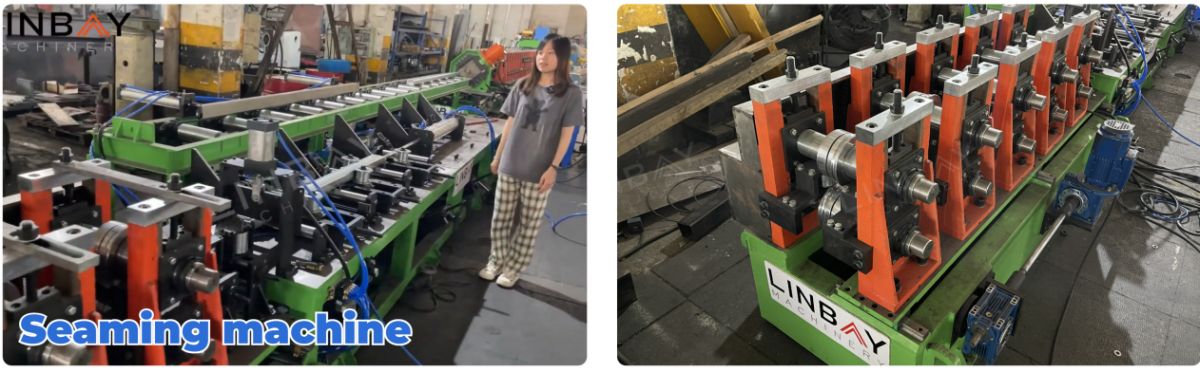
Die Falzmaschine ist im Aufbau der Rollformmaschine identisch und verfügt über eineGusseisenstruktur und Kettenantriebssystem. Es passt die Positionen der Falzstationen automatisch an die Breite des Kastenträgers an. Diese Innovationmacht einen Schweißer überflüssig, da traditionell ein Arbeiter erforderlich war, um die beiden C-Profile nach dem Rollformen zu einem Kastenträger zu verschweißen.
Encoder und SPS
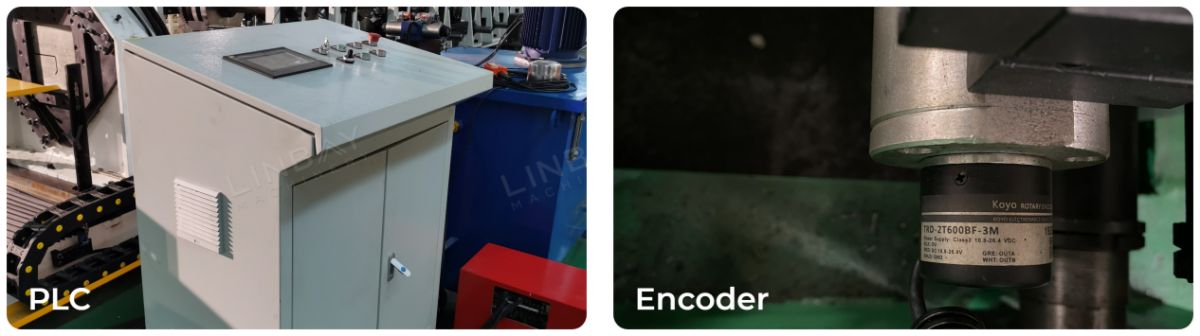
Die Rollformmaschine ist ausgestattet mit einemJapanischer Koyo-Encoder, das die Spulenlänge präzise in elektrische Signale für den SPS-Schaltschrank umwandelt. Diese Präzision garantiertSchnittfehler sind auf 1 mm begrenzt, wodurch hochwertige Kastenträger gewährleistet und Abfall reduziert werden. Bediener können Produktionsgeschwindigkeit, eingestellte Abmessungen, Schnittlänge und mehr über den SPS-Bildschirm steuern. Der Schrank speichert außerdem häufig verwendete Parameter und bietet Schutz vor Überlastung, Kurzschluss und Phasenausfall. Die Spracheinstellungen auf dem SPS-Bildschirm können an Kundenwünsche angepasst werden.
Hydraulikstation
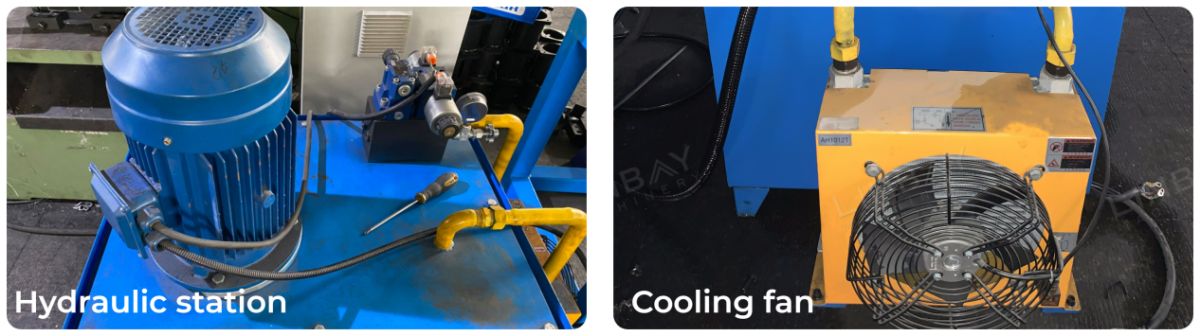
Unsere Hydraulikstation ist mit elektrischen Kühllüftern ausgestattet, die die Wärme effizient ableiten und so einen langen und zuverlässigen Betrieb mit geringer Ausfallrate gewährleisten.
Garantie
Bei der Auslieferung ist auf dem Typenschild das Lieferdatum deutlich angegeben und bietet einezwei Jahre Garantie auf die gesamte Produktlinie und beeindruckende fünf Jahre Garantie auf Walzen und Wellen.
1. Abwickelhaspel
2. Fütterung
3.Stanzen
4. Rollformständer
5. Antriebssystem
6. Schneidsystem
Sonstiges
Out-Tabelle