video
Profiel
Kruisversteviging is cruciaal voor zware stellingsystemen en biedt diagonale ondersteuning tussen twee staanders. Het helpt wiebelen te voorkomen en zorgt voor een goede uitlijning van de constructie bij zware belasting. Kruisversteviging wordt doorgaans gemaakt van warmgewalst, koudgewalst of gegalvaniseerd staal met een dikte van 1,5 tot 2 mm.
Traditioneel werden dwarsverbanden geproduceerd met behulp van buigmachines. De rolvormmachinelijn, die afrollen, nivelleren, rolvormen, ponsen en snijden omvat, biedt echter een hogere mate van automatisering en lagere arbeidskosten. Deze oplossing is voor veel klanten de voorkeurskeuze geworden vanwege de efficiëntie en kosteneffectiviteit.
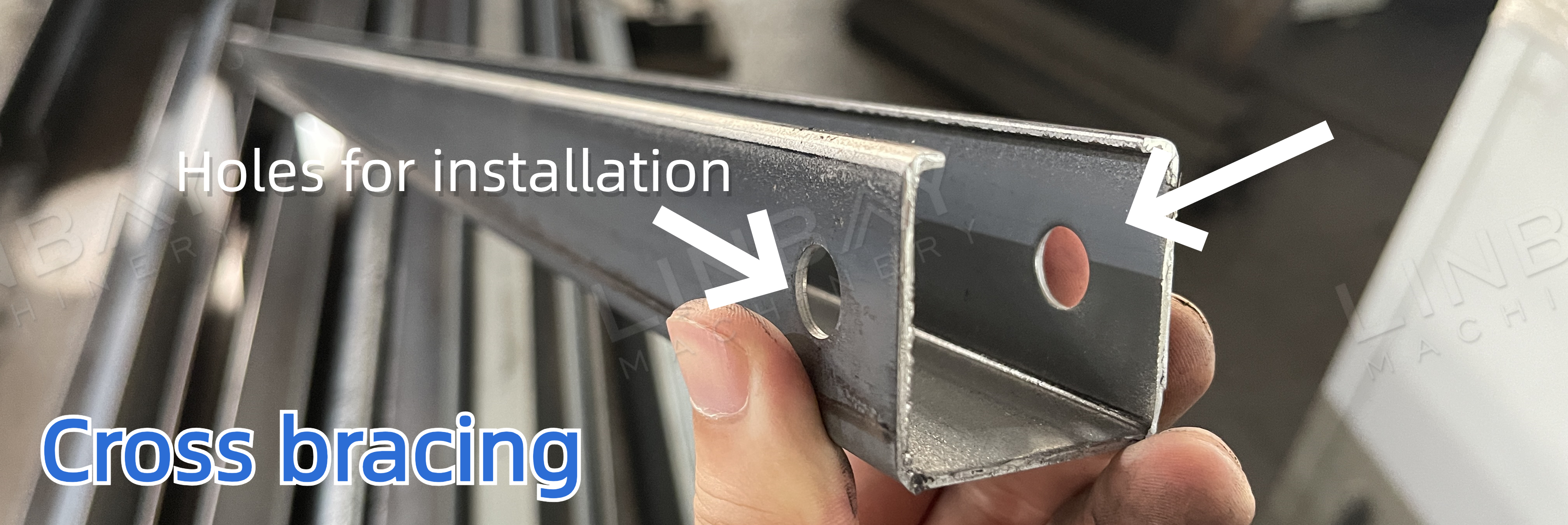
De perforatiestijlen variëren afhankelijk van de installatiemethode:
Installatiemethode 1: Er wordt één enkele beugel in de rekstaander geïnstalleerd, waarbij op de hoogte van de beugel vooraf gaten moeten worden geboord voor de schroefinstallatie.
Installatiemethode 2: Er worden twee beugels in de rekstaander geïnstalleerd. Voor de schroefinstallatie moeten er vooraf gaten in de onderkant van de beugels worden geboord.
Echte zaak - Belangrijkste technische parameters
Stroomdiagram: Decoiler--Servofeeder--Hydraulische pons--Geleiding--Rolvormmachine--Vliegende hydraulische snij--Uitvoertafel

Vergeleken met twee productielijnen met één rij, bespaart een productielijn met twee rijen u de kosten van een extra vormmachine, decoiler en servofeeder, evenals de ruimte die nodig is voor een extra productielijn. Bovendien vermindert de structuur met twee rijen de tijd die nodig is voor het wisselen van maten, in tegenstelling tot handmatige formaatwisselingen op één lijn, wat de efficiëntie verhoogt.
Echte zaak - Belangrijkste technische parameters
1. Lijnsnelheid: 4-6 m/min, instelbaar
2. Geschikt materiaal: warmgewalst staal, koudgewalst staal, gegalvaniseerd staal
3. Materiaaldikte: 1,5-2 mm.
4. Rolvormmachine: Gietijzeren structuur
5. Aandrijfsysteem: Versnellingsbak aandrijfsysteem
6. Snijsysteem: Vliegend hydraulisch snijsysteem, de rolvormer stopt niet tijdens het snijden.
7. PLC-kast: Siemens-systeem.
Echte case-Machines
1. Hydraulische decoiler*1
2. Servofeeder*1
3. Hydraulische ponsmachine*1
4. Rolvormmachine*1
5. Hydraulische snijmachine*1
6.Uit tabel*2
7. PLC-schakelkast*1
8. Hydraulisch station*2
9. Reserveonderdelendoos (gratis)*1
Echte casus-Beschrijving
Afwikkelaar
De centrale as van de decoiler ondersteunt de stalen coil en fungeert als expansie-inrichting, geschikt voor coils met een binnendiameter van 490-510 mm. De drukarm op de decoiler fixeert de coil tijdens het laden, voorkomt dat deze openspringt door interne spanning en waarborgt de veiligheid van de werknemers.
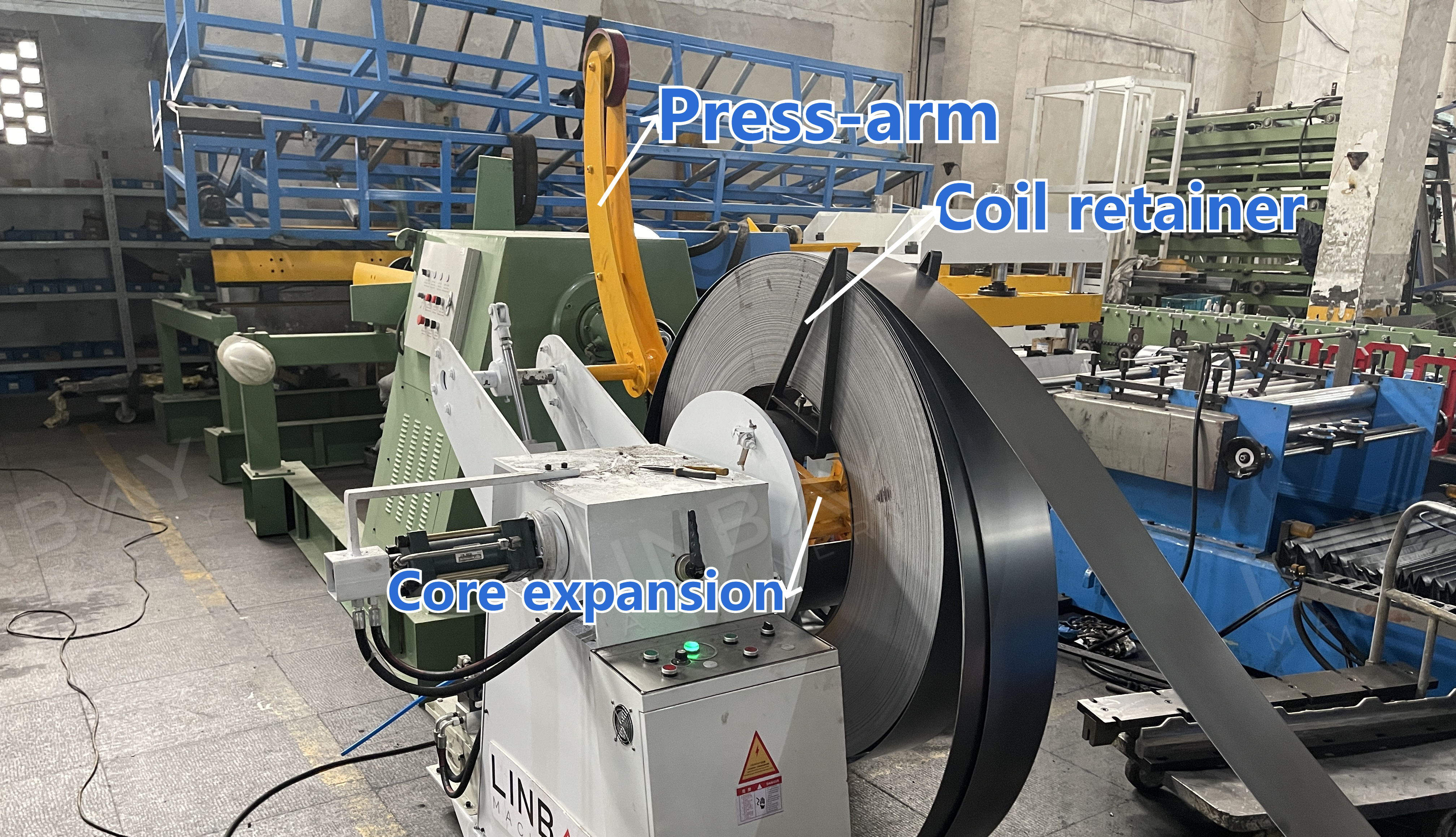
Hydraulische pons en servovoeder
De hydraulische pons, aangedreven door het hydraulische station, maakt gaten in de stalen rol. Aan beide uiteinden wordt een dwarsverband geponst, aan de flens of aan de onderkant, afhankelijk van de installatievereisten. Er zijn stand-alone en geïntegreerde hydraulische ponsmachines. Het geïntegreerde type deelt dezelfde basis met de rolvormmachine en zet andere machines stil tijdens het ponsen.
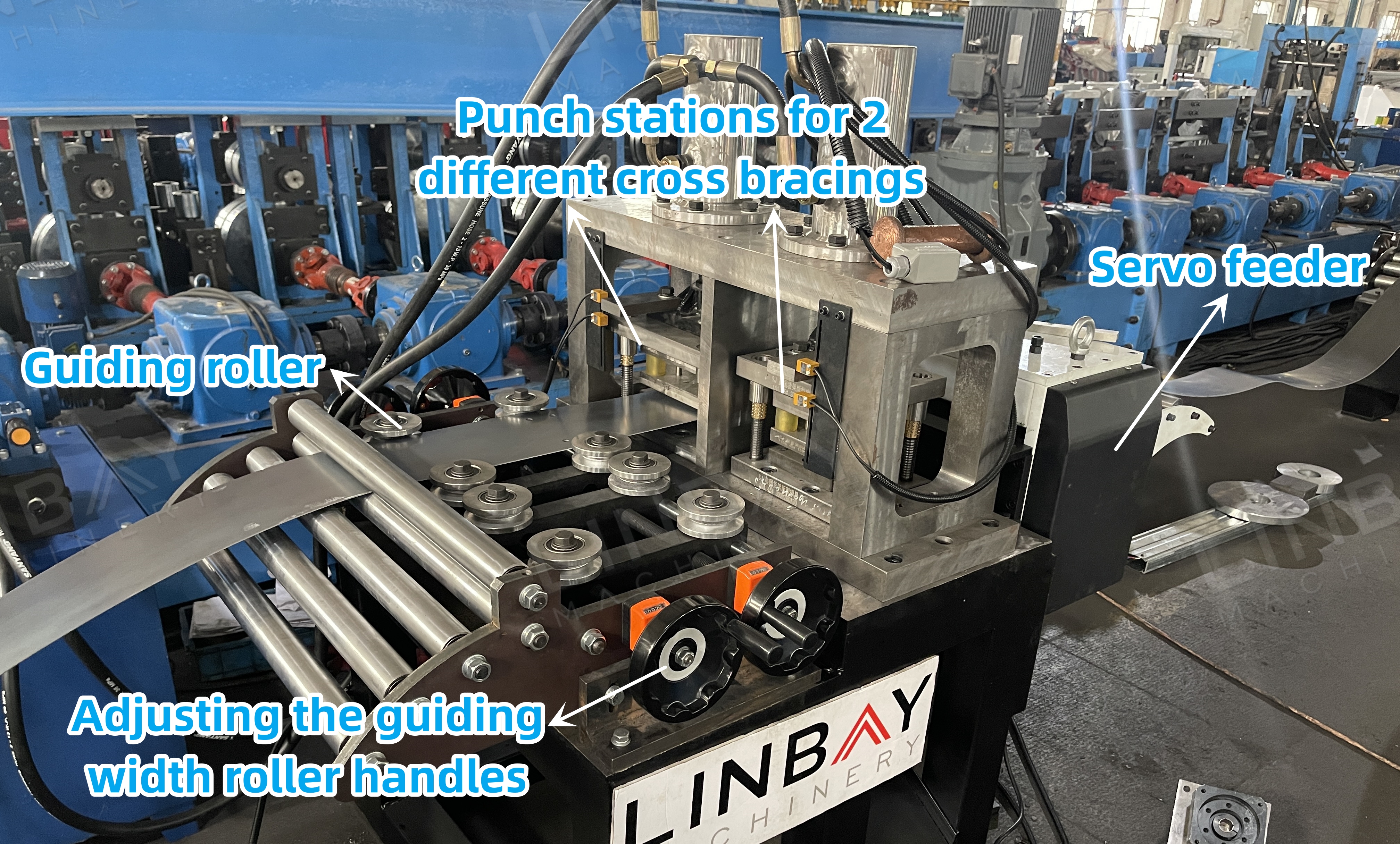
Deze productielijn maakt gebruik van de stand-alone versie, waardoor de decoiler en de vormmachine continu kunnen werken tijdens het ponsen, wat een ononderbroken productie garandeert. De stand-alone versie is voorzien van een servoaanvoer, aangedreven door een servomotor. Deze minimaliseert start-stopvertragingen en regelt de doorvoerlengte van de coil nauwkeurig voor nauwkeurig ponsen. Het pneumatische aanvoermechanisme in de aanvoer beschermt het coiloppervlak tegen krassen.
Begeleiding
Geleiderollen zorgen voor een juiste uitlijning van de spoel en de machine, zodat er geen vervorming optreedt tijdens het vormen. De rechtheid van de dwarsverbindingen heeft namelijk direct invloed op de algehele stabiliteit van het schap.
Rolvormmachine
Deze vormmachine heeft een gietijzeren constructie en een tandwielkast. Het is belangrijk om te weten dat beide rijen niet gelijktijdig kunnen werken. Voor een hogere productiecapaciteit adviseren wij een aparte productielijn voor elke maat.
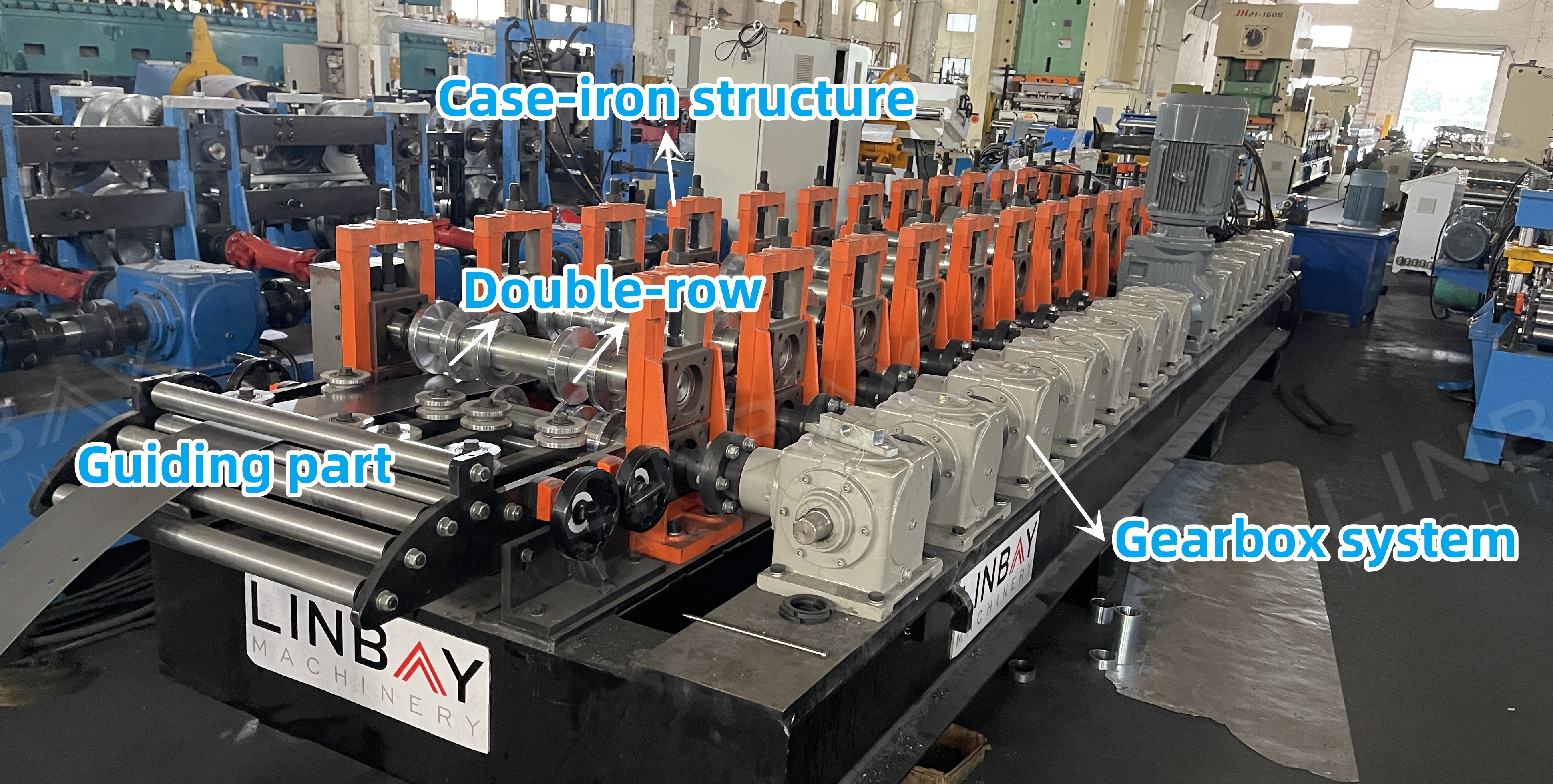
Vliegend hydraulisch snijden
Dankzij het "vliegende" ontwerp kan de basis van de snijmachine langs een spoor bewegen, waardoor er continu rollen door de vormmachine kunnen worden gevoerd zonder dat de machine hoeft te stoppen om te snijden. Dit verbetert de algehele snelheid van de lijn.
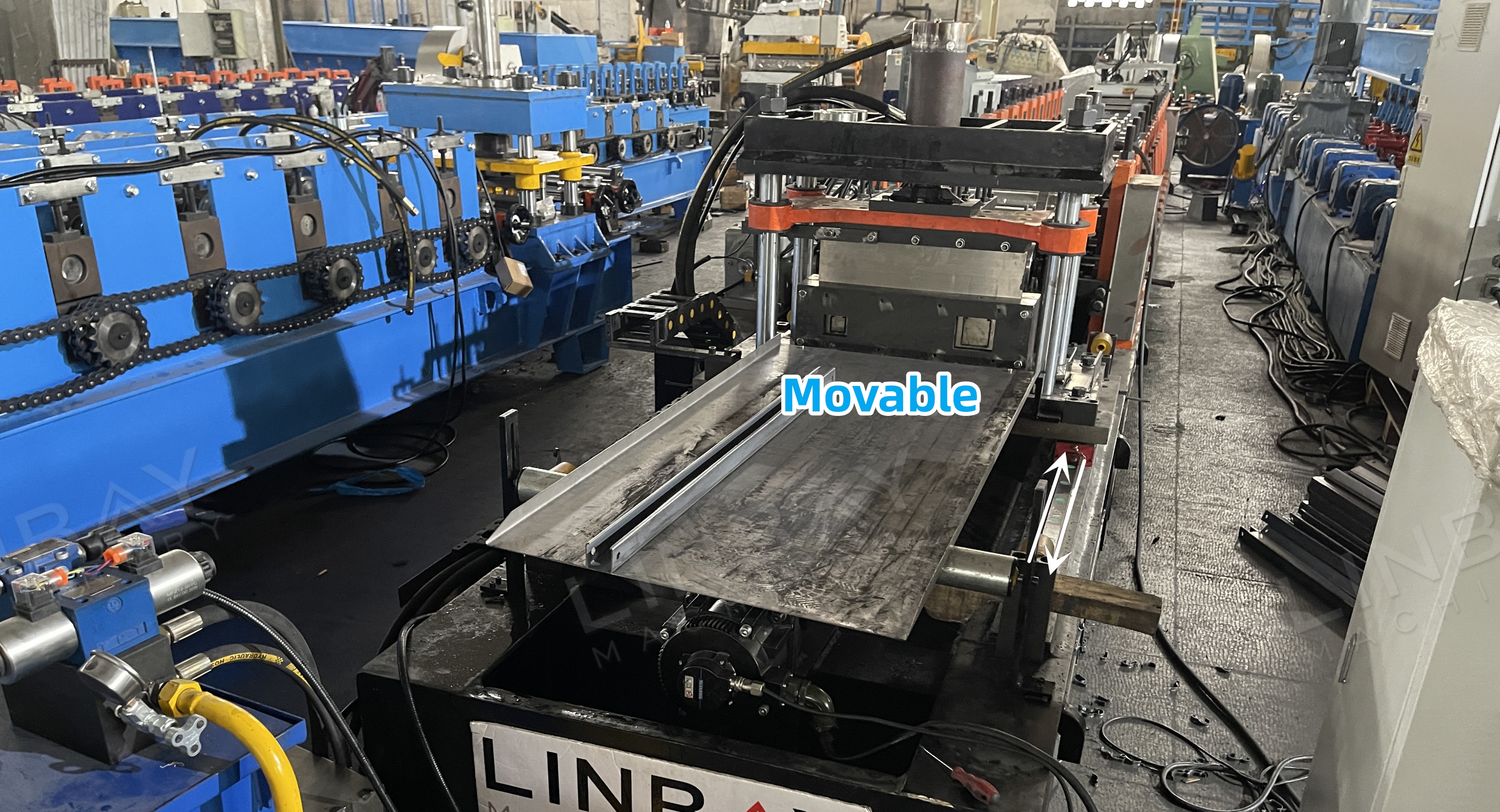
Het snijblad moet worden afgestemd op de profielvorm. Dit betekent dat voor elke maat een apart zaagblad nodig is.
Optioneel apparaat: Schaar-stomplasapparaat
De schaarlasmachine integreert zowel knip- als lasfuncties, waardoor nieuwe en oude stalen coils met elkaar verbonden kunnen worden. Dit vermindert materiaalverspilling, minimaliseert de coilwisseltijd en vereenvoudigt de afstelling. De machine maakt gebruik van TIG-lassen voor soepele en vlakke verbindingen.
Hydraulisch station
Het hydraulische station is voorzien van koelventilatoren voor effectieve warmteafvoer, wat zorgt voor continue werking en een hogere productiviteit. Het staat bekend om zijn betrouwbaarheid en duurzame prestaties.
PLC-schakelkast en encoder
De encoder zet de gemeten spoellengte om in elektrische signalen voor de PLC-schakelkast. Deze regelt de productiesnelheid, de output per cyclus en de snijlengte. Dankzij de nauwkeurige feedback van de encoder bereikt de snijmachine een snijnauwkeurigheid van ±1 mm.
1. Afwikkelaar
2. Voeding
3.Ponsen
4. Rolvormstandaards
5. Aandrijfsysteem
6. Snijsysteem
Anderen
Uit tafel