VIDEO
Profiel
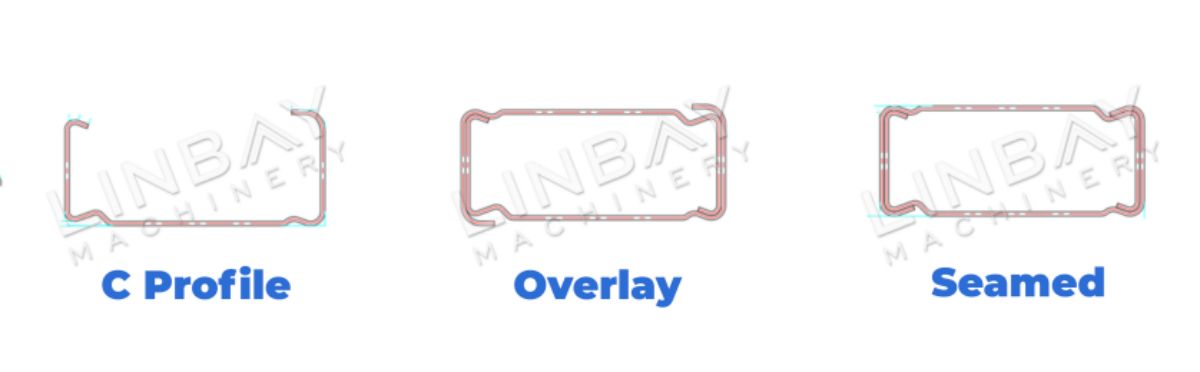
De kokerbalk is een robuuste optie, speciaal ontworpen voorzwaar uitgevoerdtoepassingen. Concreet presenteren we eentweedelige kokerbalkTer overweging. Meestal gesmeed uit koudgewalst of warmgewalst staal met een dikte van 1,5 tot 2 mm, ondergaat het een nauwkeurige bewerking.rolvormenvoordat ze worden gecoat om een balans te garanderen tussen visuele aantrekkingskracht en duurzame sterkte. De montage omvat het stevig verbindentwee stukken gevormde C-vormige stalen profielen, wat resulteert in een stevige buisconstructie. Voor de productie van kokerbalken is de koudwalsmachine de voorkeurskeuze, omdat deze efficiëntie en precisie biedt.
Echte zaak - Belangrijkste technische parameters
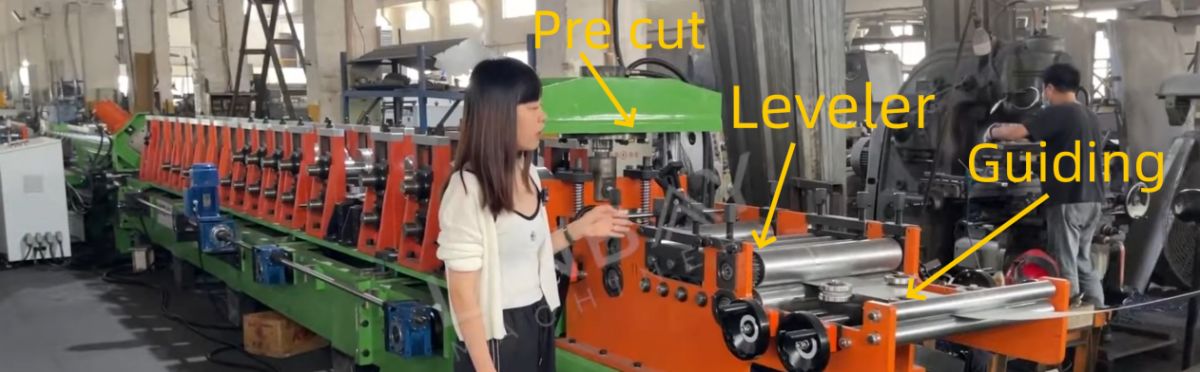
Geleiderollen zijn cruciaal bij het effectief handhaven van de uitlijning tussen de stalen rol en de machine.het voorkomen van vervormingvan de kokerbalk. Ze spelen ook een essentiële rol in het vormproces, omdat ze terugverende vervorming van de stalen rol voorkomen.De rechtheidvan de kokerbalk heeft aanzienlijke invloed opproductkwaliteit en het draagvermogenvan de gehele plank. Strategisch geplaatst langs de vormlijn zorgen geleiderollen voor een nauwkeurige uitlijning.MetingenDe afstand van elke geleiderol tot de rand is nauwkeurig vastgelegd in de handleiding. Hierdoor is het mogelijk om op basis van deze gegevens naadloze aanpassingen te doen, zelfs bij kleine verschuivingen tijdens het transport of de productie.
Waterpas
Na de voorgaande fase gaat de stalen rol over naar het nivelleerproces. Hier wordt de nivelleermachine ijverig ingezet.elimineert elke kromming die aanwezig is in de stalen spoel, waardoor de vlakheid en parallelliteit worden verbeterd, wat vervolgens de kwaliteit van het eindproduct - de kokerbalk - verbetert. Uitgerust met 2 boven- en 3 onderwalsen, garandeert de walsmachine een nauwkeurige voorbereiding van de stalen rol voor de volgende productiestappen.
Hydraulisch voorgesneden
Deze productielijn omvatporiëneen hydraulisch voorsnij-apparaat,vereenvoudiging van het vervangen van stalen rollen met verschillende breedtes en diktes, terwijl tegelijkertijdhet minimaliseren van spoelafval.
Rolvormmachine
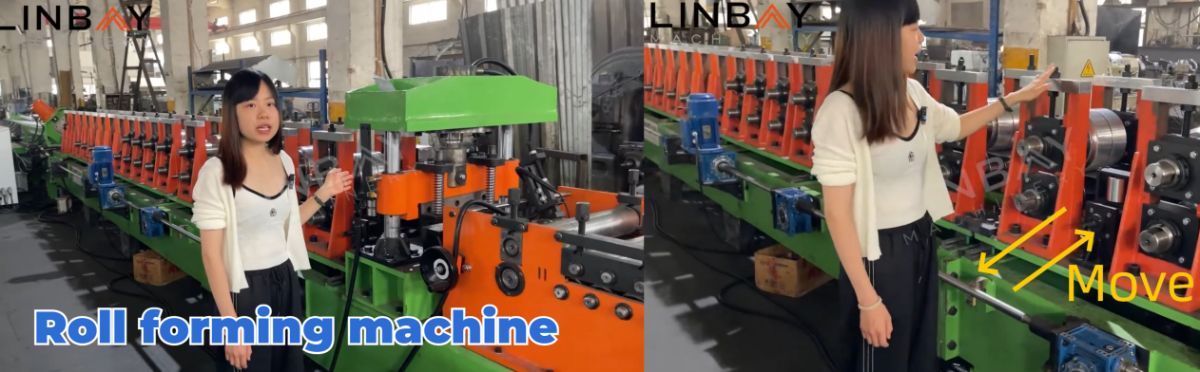
Stroomdiagram

Handmatige afwikkelaar--Geleiding--Nivelleringsapparaat--Hydraulische voorsnijding--Rolvormmachine--Vliegende hydraulische snede--Platform--Naadmachine--Uitvoertafel
Belangrijkste technische parameters
1. Lijnsnelheid: 0-4 m/min, instelbaar
2. Profielen: Verschillende maten - dezelfde hoogte van 50 mm en verschillende breedtes van 80, 100, 120 mm
3. Materiaaldikte: 1,5-2 mm
4. Geschikt materiaal: warmgewalst staal, koudgewalst staal, gegalvaniseerd staal
5. Rolvormmachine: Gietijzeren structuur
ketting- en kettingaandrijfsysteem.
6. Aantal vormstations: 18
7. Snijsysteem: Hydraulisch snijden, rolvormer stopt niet tijdens het snijden.
8. Formaat wijzigen: Automatisch.
9. PLC-kast: Siemens-systeem.

Echte casus-Beschrijving
Handmatige decoiler
De handmatige decoiler is uitgerust met eenremsysteemZorgvuldig ontworpen om de spanning van de afwikkelende rol te regelen en een soepel afwikkelproces te garanderen. Om het risico op plotselinge terugslag te beperken, met name bij stalen coils met een dikte van meer dan 1,5 mm,een persarmwordt gebruikt om de stalen spoel stevig op zijn plaats te houden. Bovendien zijn er strategisch geplaatste stalen beschermbladen om te voorkomen dat de spoel wegglijdt tijdens het afrollen. Dit doordachte ontwerp verhoogt niet alleen de veiligheid, maar biedt ookhoge kosteneffectiviteit, waardoor een betrouwbare en efficiënte werking wordt gegarandeerd.
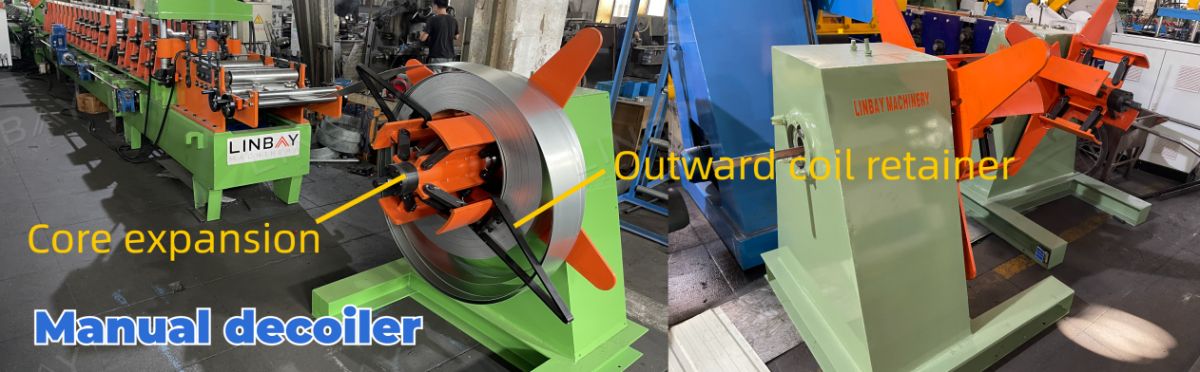
In dit scenario is een handmatige decoilerzonder eigen energiebronwordt gebruikt. Voor hogere productiesnelheidsvereisten bieden wij een optionelehydraulische decoileraangedreven door een hydraulisch station.
Begeleiding
Het hart van de gehele productielijn wordt gevormd door de rolvormmachine, een onmisbaar onderdeel. Gemaakt uit één stukgietijzerDeze machine heeft een robuuste structuur en wordt aangedreven door een betrouwbarekettingsysteemDe veelzijdigheid maakt de productie van verschillende formaten met een consistente hoogte mogelijk. Operators voeren moeiteloos geplande afmetingen in op het PLC-bedieningsscherm, waardoorautomatische aanpassingenvan vormstations naar precieze posities. Ervaren medewerkers hebben doorgaans ongeveer 60 minuten nodig om het volledige maatveranderingsproces uit te voeren, inclusief zowel de automatische verplaatsing van de vormstations als het handmatig vervangen van de stalen rol.
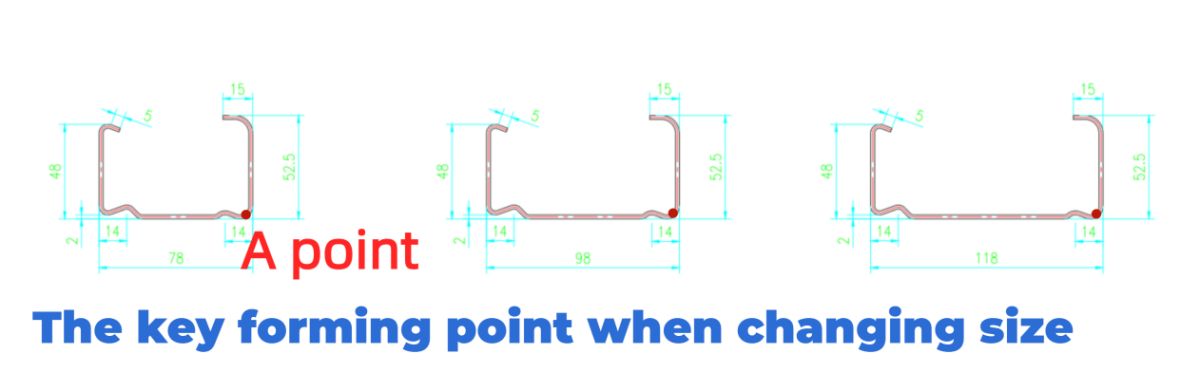
DeEen puntfungeert als een draaipunt voor breedteaanpassingen. Terwijl rolvormstations over de rails bewegen, verschuiven ze dynamisch de positie van dit kritieke vormpunt, waardoor de productie vandoos balken met verschillende breedtes.
Voor het materiaal van de vormrollen is gekozen voor GCR15, een chroomhoudend staal met een hoog koolstofgehalte dat bekendstaat om zijn uitzonderlijke hardheid en slijtvastheid. Deze rollen worden verchroomd om hun levensduur te verlengen, terwijl de assen, vervaardigd uit 40Cr-materiaal, een warmtebehandeling ondergaan voor extra duurzaamheid.
Vliegende hydraulische snede

Na het rolvormingsproces vormt de stalen rol zich geleidelijk tot een C-vormig profiel. Vervolgens wordt deze met een hydraulische snijmachine nauwkeurig op de gewenste lengte gesneden, waarbij eensnijlengtefout binnen 1 mmDit snijproces minimaliseert efficiënt het verlies van staalrollen en synchroniseert met de productiesnelheid van de rolvormmachine, waardoor een naadloze en ononderbroken werking wordt gegarandeerd.
Platform
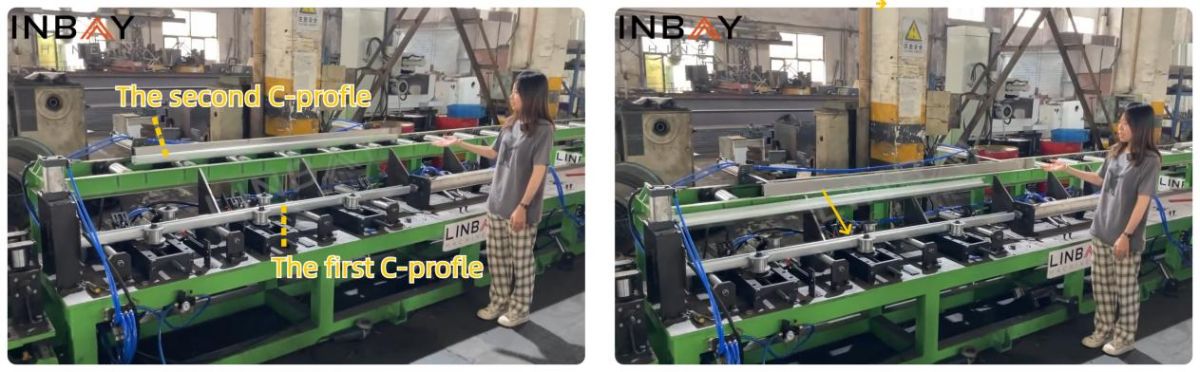
Het eerste C-profiel wordt naar het bovenste platform getransporteerd en vervolgens op het onderste platform geduwd. Vervolgens wordt het tweede C-profiel voorzichtig op de middelste helling geduwd, waar een kantelmechanisme het roteert. Door deze handeling worden de twee C-profielen uitgelijnd en netjes verticaal gestapeld.
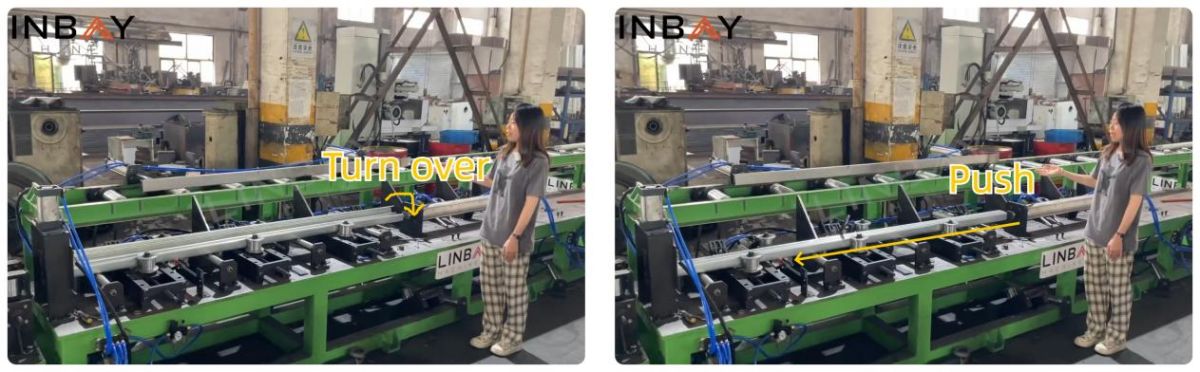
Geleiderollen zorgen voor de uitlijning van de twee C-profielen en pneumatische duwstangen duwen ze in de felsmachine.
Naaimachine
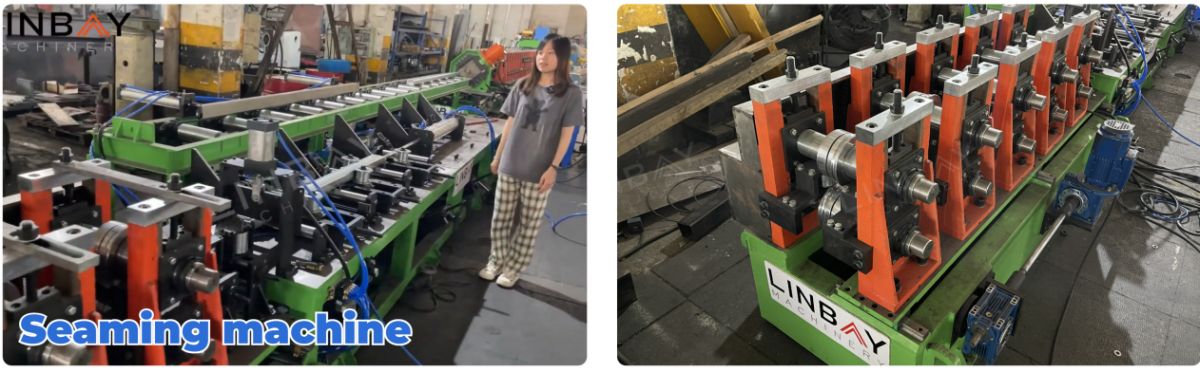
De naaimachine weerspiegelt de structuur van de rolvormmachine en beschikt over eengietijzeren constructie en kettingaandrijfsysteemHet past de posities van de naaistations autonoom aan op basis van de breedte van de kokerbalk. Deze innovatiemaakt een lasser overbodig, zoals traditioneel het geval was, moest een arbeider de twee C-profielen na het walsen tot een kokerbalk lassen.
Encoder en PLC
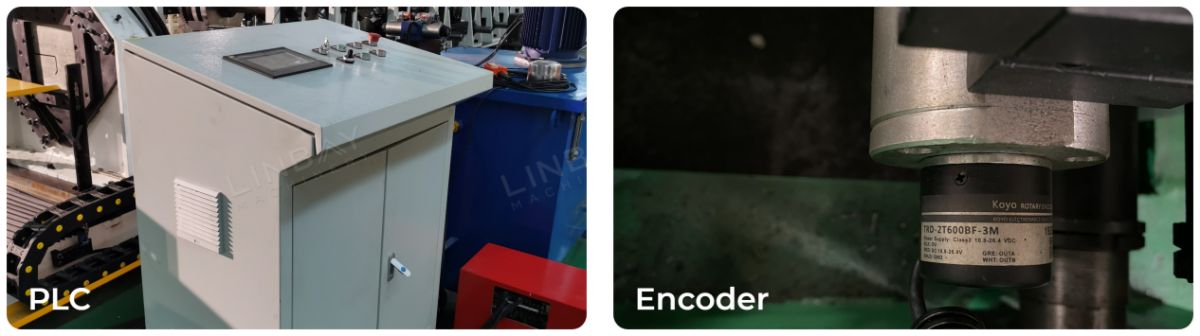
De rolvormmachine is uitgerust met eenJapanse Koyo-encoder, die de spoellengte nauwkeurig omzet in elektrische signalen voor de PLC-schakelkast. Deze precisie garandeertsnijfouten zijn beperkt tot 1 mm, wat zorgt voor hoogwaardige kokerbalken en minder afval. Operators kunnen de productiesnelheid regelen, afmetingen, snijlengtes en meer instellen via het PLC-scherm. De kast slaat ook veelgebruikte parameters op en biedt bescherming tegen overbelasting, kortsluiting en faseverlies. De taalinstellingen op het PLC-scherm kunnen worden aangepast aan de voorkeuren van de klant.
Hydraulisch station
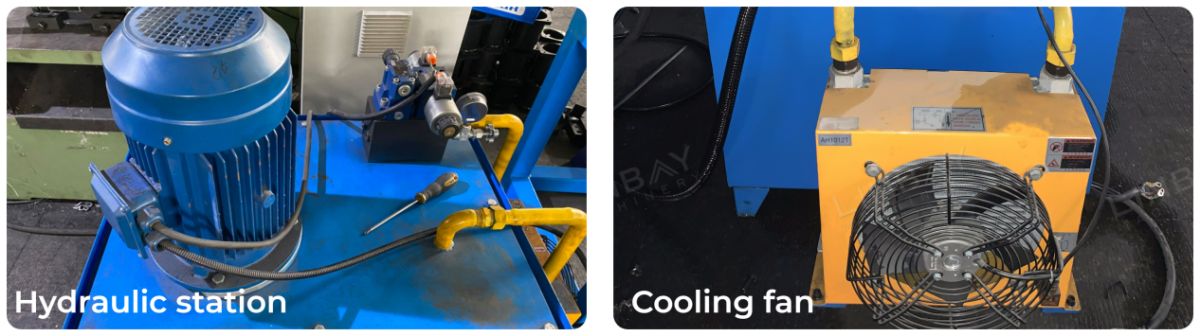
Ons hydraulische station, uitgerust met elektrische koelventilatoren, voert warmte efficiënt af, wat zorgt voor een langdurige en betrouwbare werking met een laag uitvalpercentage.
Garantie
Bij verzending geeft het naamplaatje duidelijk de leverdatum aan, waardoor er eentwee jaar garantie op de gehele productielijn en een indrukwekkende garantie van vijf jaar op rollen en assen.
1. Afwikkelaar
2. Voeding
3.Ponsen
4. Rolvormstandaards
5. Aandrijfsysteem
6. Snijsysteem
Anderen
Uit tafel